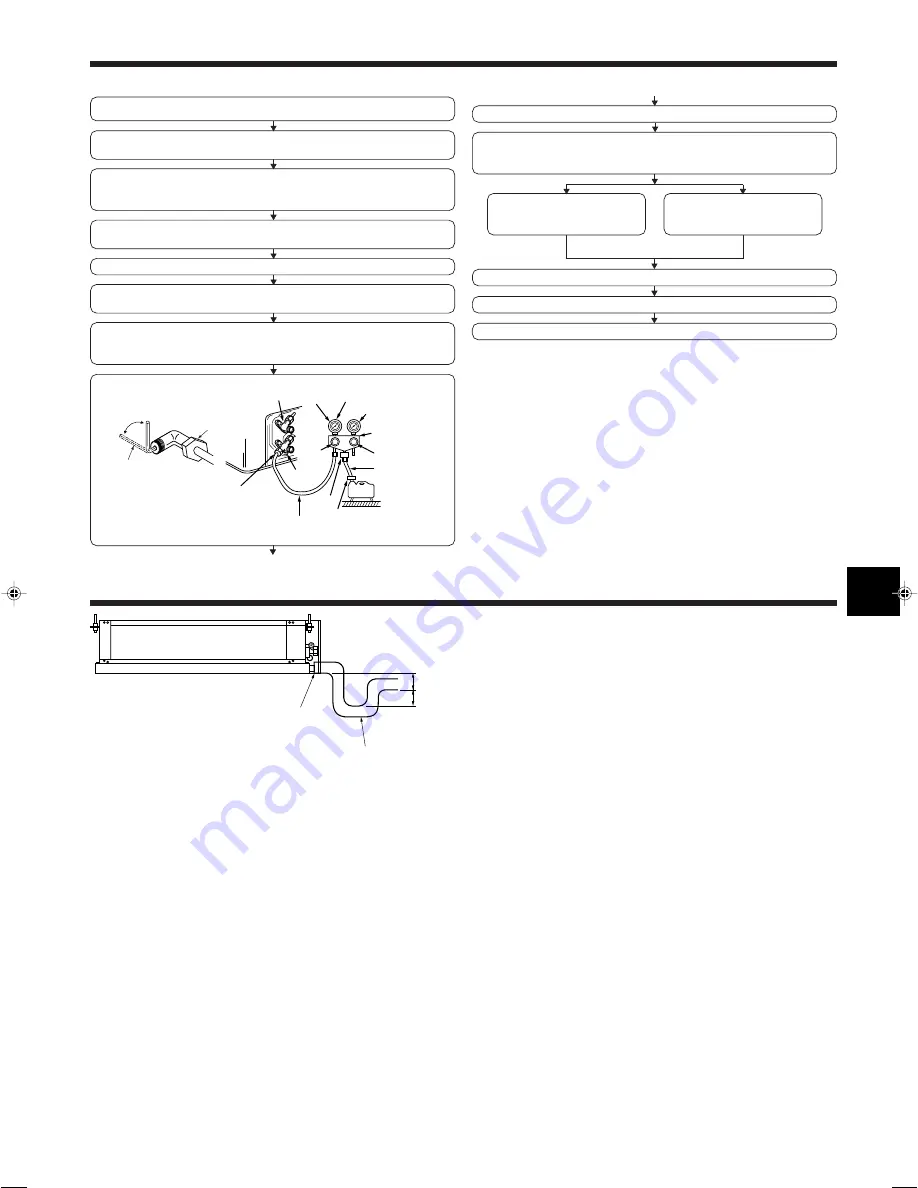
7
5. Refrigerant piping work
5.4. Purging procedures leak test
PURGING PROCEDURES
Connect the refrigerant pipes (both the liquid and gas pipes) between the indoor
and the outdoor units.
Remove the service port cap of the stop valve on the side of the outdoor unit gas pipe.
(The stop valve will not work in its initial state fresh out of the factory (totally closed
with cap on).)
Connect the gage manifold valve and the vacuum pump to the service port of the
stop valve on the gas pipe side of the outdoor unit.
Run the vacuum pump. (Vacuumize for more than 15 minutes.)
Check the vacuum with the gage manifold valve, then close the gage manifold valve,
and stop the vacuum pump.
Leave it as is for one or two minutes. Make sure the pointer of the gage manifold
valve remains in the same position. Confirm that the pressure gage show -0.101MPa
(-760 mmHg)
Pipe length :
7 m maximum
No gas charge is needed.
Pipe length exceeding 7 m
Charge the prescribed
amount of gas.
Remove the gage manifold valve quickly from the service port of the stop valve.
After refrigerant pipes are connected and evacuated, fully open all stop valves on
gas and liquid pipe sides.
Operating without fully opening lowers the performance and causes trouble.
Tighten the cap to the service port to obtain the initial status.
Retighten the cap
Leak test
*Close
*Open
Hexagonal wrench
Stop valve
*4 to 5 turns
Stop valve
(or the vacuum
pump with the
function to
prevent the back
flow)
Gauge manifold
valve (for R410A)
Pressure gauge
(for R410A)
Compound pressure
gauge (for R410A)
-0.101MPa
(-760 mmHg)
Handle
Low
Handle High
Window
Charge hose
(for R410A)
Vacuum
pump
Adapter for
preventing
the back flow
Charge hose
(for R410A)
Service port
Stop
valve
6. Drainage piping work
Fig. 6-1
6.1. Drainage pipe connection (Fig. 6-1)
Indoor unit’s drainage pipe
• The drainage pipe should be arranged so that the discharge end is lower than the
other end, as shown in the figure opposite.
• Place the trap outside the unit.
• After connecting the drainage pipe, make sure that water is discharged properly
and that there are no leaks.
A
Drainage piping connection 1 RP male.
B
Trap
Outdoor unit drainage pipe connection
When drainage piping is necessary, use the drain pan (supplied as an option).
A
B
H
1
H
2
H
1
: 50 mm or more
H
2
: 1/2 H
1
or more