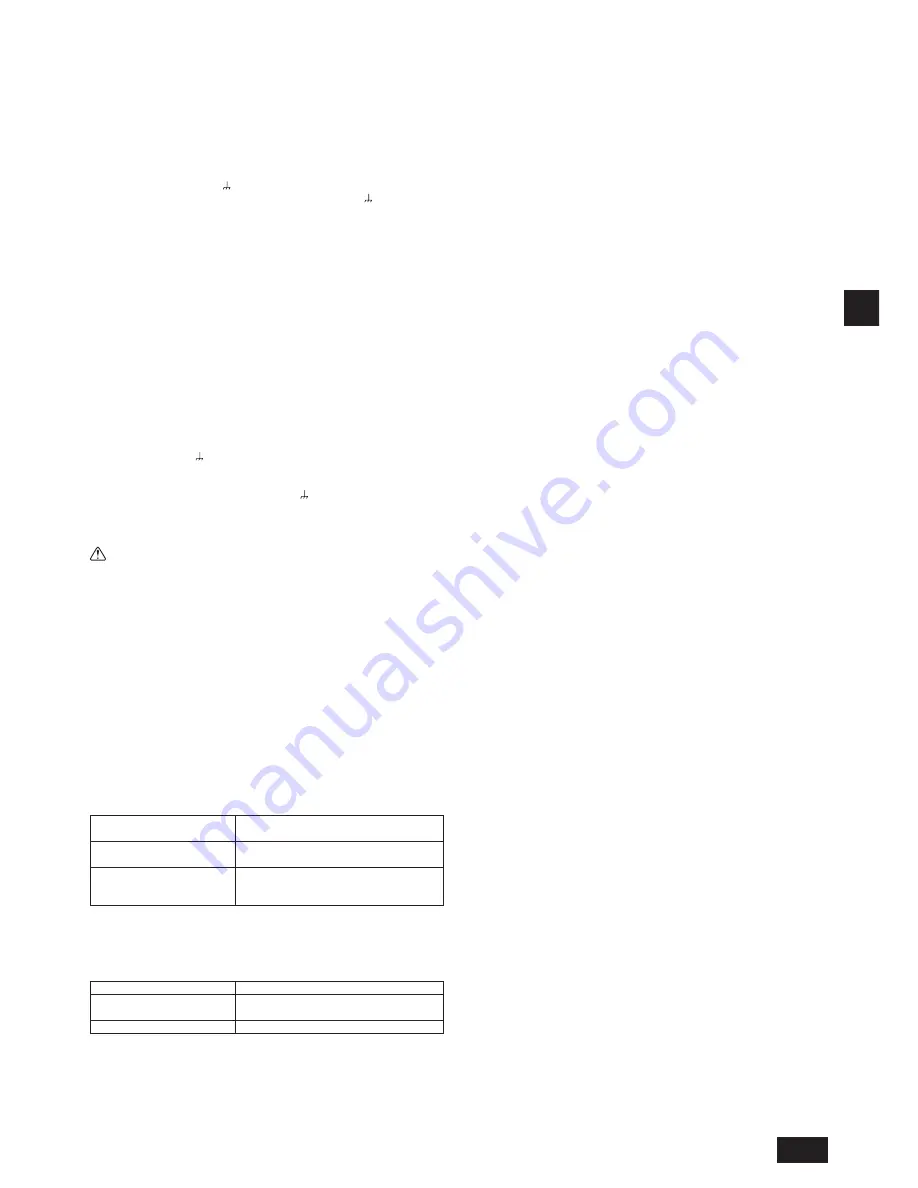
31
GB
11.2. Control box and connecting position
of wiring
1
Heat source unit
1. Remove the front panel of the heat source unit by unscrewing the screws,
and pushing it up, then pulling it out.
2. Connect the indoor - heat source transmission line to the terminal block
(TB3).
If multiple heat source units are connected in the same refrigerant system,
daisy-chain TB3 (M1, M2,
Terminal) on the heat source units. Connect
the indoor - heat source transmission line to TB3 (M1, M2,
Terminal) of
only one of the heat source units.
3. Connect the transmission lines for centralized control (between the
centralized control system and the heat source unit of different refrigerant
systems) to the terminal block for centralized control (TB7). If the multiple
heat source units are connected to the same refrigerant system, daisy-chain
TB7 (M1, M2, S Terminal) on the heat source units. (*1)
*1: If TB7 on the heat source unit in the same refrigerant system is not
daisy-chained, connect the transmission line for centralized control to
TB7 on the OC (*2). If the OC is out of order, or if the centralized control
is being conducted during the power supply shut-off, daisy-chain TB7
on the OC, OS1, and OS2 (In the case that the heat source unit whose
power supply connector CN41 on the control board has been replaced
with CN40 is out of order or the power is shut-off, centralized control will
not be conducted even when TB7 is daisy-chained).
*2: OC, OS1, and OS2 of the heat source units in the same refrigerant
system are automatically identified. They are identified as OC, OS1, and
OS2 in descending order of capacity (If the capacity is the same, they
will be in ascending order of their address number).
4. The indoor-heat source transmission line, connect the shield ground to the
grounding terminal (
). For the centralized transmission lines, connect to
the shield terminal (S) on the terminal block (TB7). If the heat source units
whose power supply connector CN41 is replaced with CN40, short circuit the
shield terminal (S) and the ground terminal ( ) in addition to the above.
5. Attach the connected wires securely with the cable strap at the bottom of the
terminal block. External force applied to the terminal block may damage it,
resulting in a short circuit, ground fault, or a fire.
Caution:
Tighten terminal screws to the specified torque.
- Poor wire contact caused by loose screws may result in overheating and
resultant fire.
- The use of the unit with a damaged circuit board may result in overheating and
resultant fire.
Note:
• Tighten terminal screws to the specified torque.
(*1)
*1: Terminal block (TB1 (TLMU: M8 screw)) : 6 ~ 15 [N·m]
Terminal block (TB1 (YLMU: M6 screw)) : 2.5 ~ 2.9 [N·m]
Terminal block (TB3, TB7 (M3.5 screw)) : 0.82 ~ 1.0 [N·m]
•
Make sure that the spring washers are parallel to the terminal block.
•
Make sure that the wires are securely fastened to the terminal screws.
•
Drive the screws straight down, and use caution not to damage the
screw heads.
•
Install the ring terminals back to back so that the screws can be driven
straight down.
•
Make an alignment mark with a permanent marker across the screw
head, washer, and terminal after tightening the screws.
[Fig. 11.2.1] (P.14)
A
Power source
B
Transmission line
C
Ground terminal
[Fig. 11.2.2] (P.14)
A
Terminal block with loose screws
B
Properly installed terminal block
C
Spring washers must be parallel to the terminal block.
[Fig. 11.2.3] (P.14)
A
Power wires, transmission lines
B
Daisy-chain (transmission lines only)
C
Terminal blocks (TB1, TB3, TB7)
D
Make an alignment mark.
E
Install the ring terminals back to back.
[Fig. 11.2.4] (P.14)
A
Cable strap
B
Power source cable
C
Ground terminal for field wiring connection
2
Conduit tube installation
•
Hammer the knockout holes for the conduit tube located on the base and the
bottom part of the front panel.
•
When installing the conduit tube directly through the knockout holes, remove
burrs and protect the tube with masking tape.
•
Use the conduit tube to narrow the opening if there is a possibility of small
animals entering the unit.
11.3. Wiring transmission cables
1
Types of control cables
1. Wiring transmission cables
•
Types of transmission cables: Shielding wire CVVS, CPEVS or MVVS
•
Cable diameter: More than 1.25 mm
2
[AWG16]
•
Maximum wiring length: Within 200 m [656ft]
•
Maximum length of transmission lines for centralized control and indoor/heat source transmission lines: 500 m [1640ft] at the maximum
The maximum length of wiring between power supply unit for transmission lines (for centralized control), and each heat source unit and system controller is 200 m [656ft].
2. Remote control cables
•
ME Remote Controller
Type of remote control cable
Sheathed 2-core cable
(CVV, shielded CVVS, CPEVS, or MVVS)
Cable diameter
0.3 to 1.25 mm
2
[AWG 22 to 16]
(0.75 to 1.25 mm
2
[AWG 18 to 16])*
Remarks
When 10 m [32ft] is exceeded, use cable
with the same specifications as 1. Wiring
transmission cables.
* Connected with simple remote controller.
CVVS, MVVS: PVC insulated PVC jacketed shielded control cable
CPEVS: PE insulated PVC jacketed shielded communication cable
CVV: PVC insulated PVC sheathed control cable
•
MA Remote Controller
Type of remote control cable
Sheathed 2-core cable (unshielded) CVV
Cable diameter
0.3 to 1.25 mm
2
[AWG 22 to 16]
(0.75 to 1.25 mm
2
[AWG 18 to 16])*
Remarks
Within 200 m [656ft]
* Connected with simple remote controller.