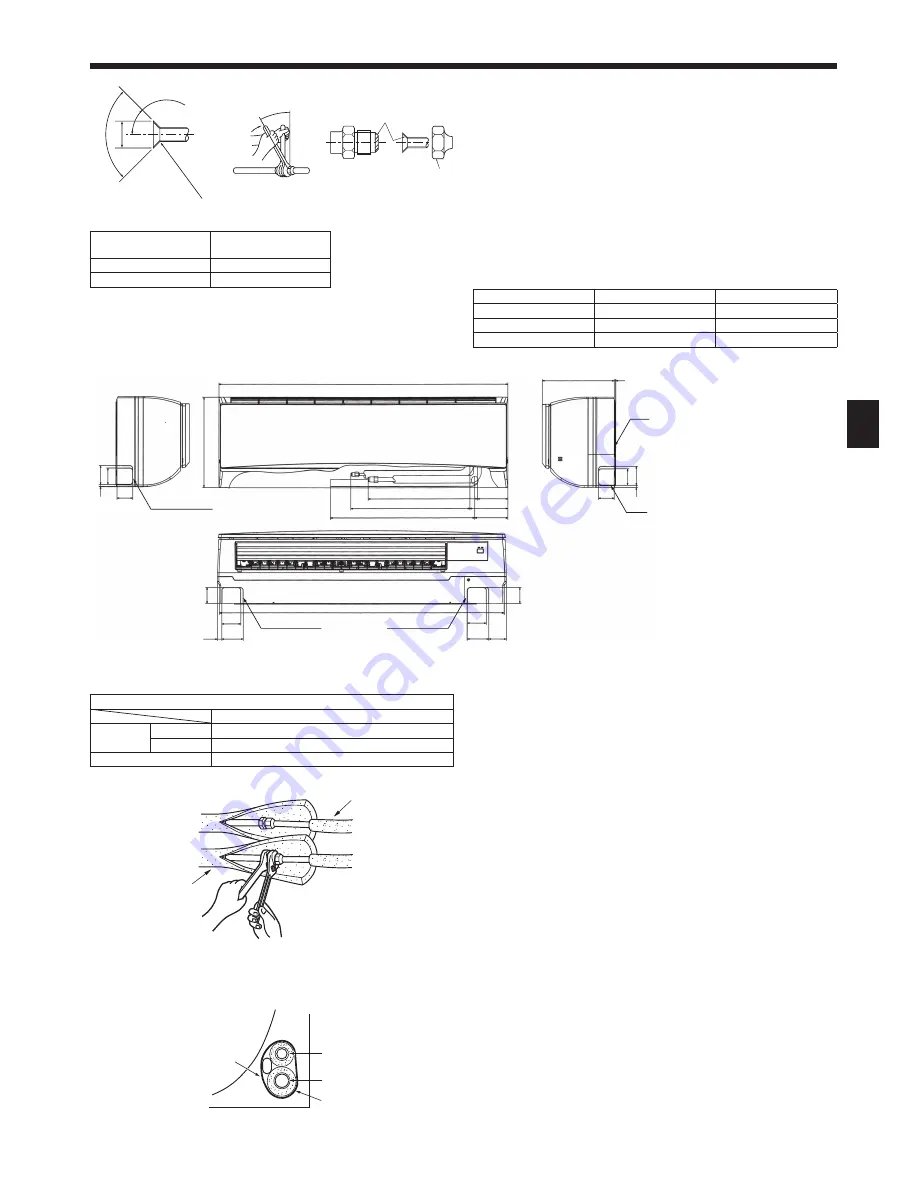
7
4. Installing the refrigerant piping
A
Flare cutting dimensions
Copper pipe O.D.
(mm)
Flare dimensions
øA dimensions (mm)
ø9.52
12.8 - 13.2
ø15.88
19.3 - 19.7
øA
45±2°
Fig. 4-1
Fig. 4-2
D
65
77
7.8
67
365
1170
444 (
A
)*
123
482 (
B
)
154
585 (
C
)
1155
65
65
77
87
F
F
77
87
71.2
18.2
134
295
5
65
67 77
7.8
G
E
4.1. Connecting pipes (Fig. 4-1)
• When commercially available copper pipes are used, wrap liquid and gas pipes
with commercially available insulation materials (heat-resistant to 100 °C or
more, thickness of 12 mm or more).
• The indoor parts of the drain pipe should be wrapped with polyethylene foam
insulation materials (specific gravity of 0.03, thickness of 9 mm or more).
• Apply thin layer of refrigerant oil to pipe and joint seating surface before
tightening flare nut.
• Use two wrenches to tighten piping connections.
• Use refrigerant piping insulation provided to insulate indoor unit connections.
Insulate carefully.
B
Flare nut tightening torque
C
Do not apply refrigerating machine oil to the screw portions.
(This will make the flare nuts more apt to loosen.)
D
Be certain to use the flare nuts that are attached to the main unit.
(Use of commercially-available products may result in cracking.)
Copper pipe O.D.
Flare nut O.D.
Tightening torque
(mm)
(mm)
(N·m)
ø9.52
22
34 - 42
ø15.88
29
68 - 82
PKA-RP60, 71, 100KAL
Fig. 4-3
Fig. 4-4
PKA-RP60, 71, 100KAL
B
A
D
C
B
A
4.2. Indoor unit
Refrigerant and Drainage Piping Sizes
Item
Model
PKA-RP60, 71, 100KAL
Refrigerant
piping
Liquid
ODø9.52 (3/8")
Gas
ODø15.88 (5/8")
Drainage piping
ODø16
4.3. Positioning refrigerant and drain piping (Fig. 4-2)
PKA-RP60, 71, 100KAL
A
Gas pipe
* Indicates the condition with accessories mounted.
B
Liquid pipe
C
Drain hose
D
Left-side piping knockout hole
E
Right-side piping knockout hole
F
Lower piping knockout hole
G
Mount board
1
4.4. Refrigerant piping (Fig. 4-3)
Indoor unit
1. Remove the flare nut and cap of the indoor unit.
2. Make a flare for the liquid pipe and gas pipe and apply refrigerating machine oil
(available from your local supplier) to the flare sheet surface.
3. Quickly connect the on site cooling pipes to the unit.
4. Wrap the pipe cover that is attached to the gas pipe and make sure that the
connection join is not visible.
5. Wrap the pipe cover of the unit’s liquid pipe and make sure that it covers the
insulation material of the on site liquid pipe.
6. The portion where the insulation material is joined is sealed by taping.
A
Site-side refrigerant piping
B
Unit side refrigerant piping
4.4.1. Storing in the piping space of the unit (Fig.4-4)
1. Wrap the supplied felt tape in the range of the refrigerant piping which will be
housed within the piping space of the unit to prevent dripping.
2. Overlap the felt tape at one-half of the tape width.
3. Fasten the end portion of the wrapping with vinyl tape, etc.
A
Gas pipe
B
Liquid pipe
C
Indoor/outdoor connection cable
D
Felt tape
3
R0.4~R0.8
90°±0.5°