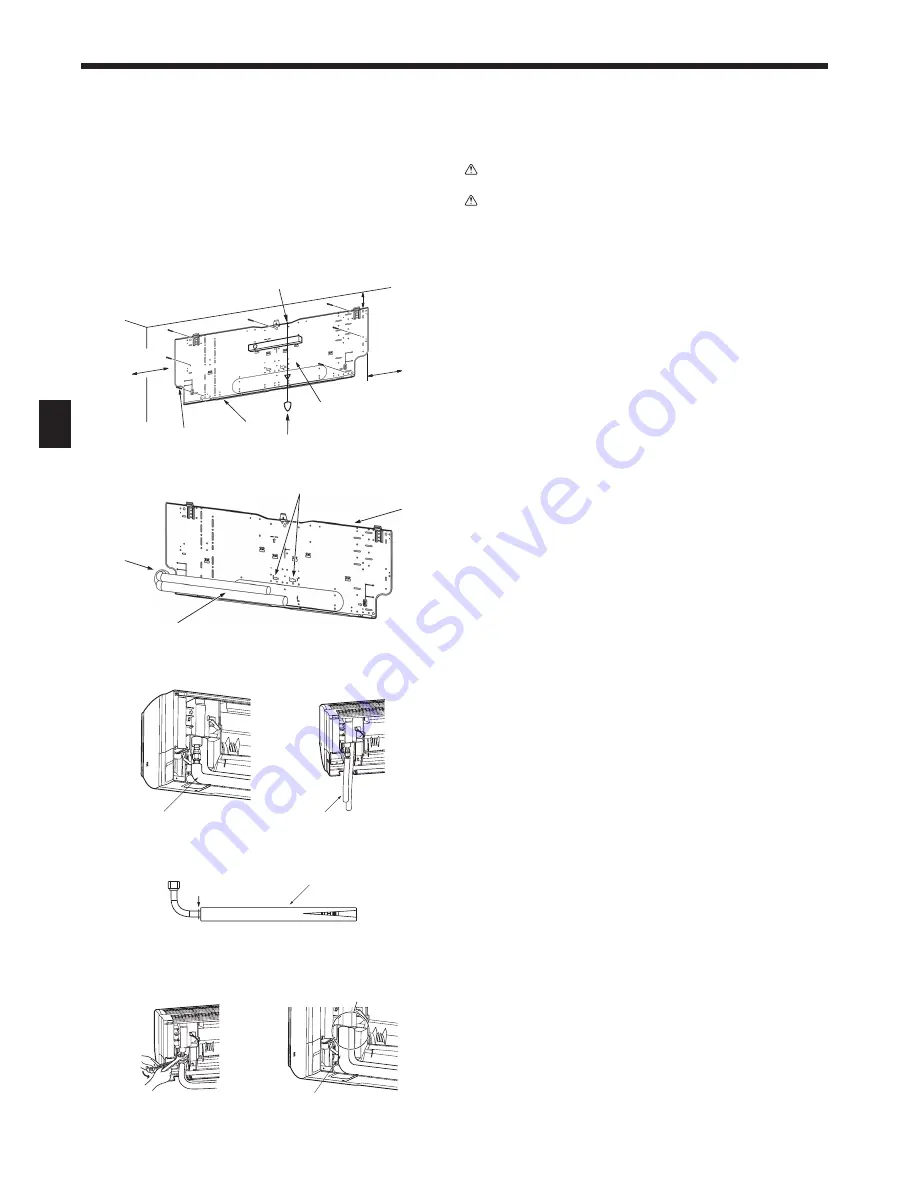
4
3. Installing the indoor unit
Fig. 3-4
A
B
C
D
I
G
F
H
E
PKA-RP60, 71, 100KAL
Fig. 3-5
Fig. 3-7
Fig. 3-6
A
A
Fig. 3-8
A
B
D
C
E
Fig. 3-10
Fig. 3-9
B
A
C
D
3.2.3. Installing the wall mounting fixture
►
Since the indoor unit weighs near 21 kg, selection of the mounting
location requires thorough consideration. If the wall does not seem to be
strong enough, reinforce it with boards or beams before installation.
►
The mounting fixture must be secured at both ends and at the centre, if
possible. Never fix it at a single spot or in any nonsymetrical way.
(If possible, secure the fixture at all the positions marked with a bold arrow.)
Warning:
If possible, secure the fixture at all positions indicated with a bold arrow.
Caution:
• The unit body must be mounted horizontally.
• Fasten at the holes marked with
▲
as shown by the arrows.
PKA-RP60, 71, 100KAL (Fig. 3-4)
A
Min. 120 mm (617.6 mm or greater with optional drain pump installation)
B
Min. 220 mm
C
Min. 70 mm (130 mm or greater with left, rear left, or lower left piping, and optional drain
pump installation)
D
Fixing screws (4 × 25)
2
E
Level
F
Fasten a thread to the hole.
G
Place the level against the horizontal reference line of the mount board and mount so that it is
level. Hang a weight from the thread and align with
▼
EPK of the mount board to permit leveling.
H
Weight
I
Mount board
1
3.3. When embedding pipes into the wall (Fig. 3-5)
• The pipes are on the bottom left.
• When the cooling pipe, drain pipes internal/external connection lines etc are to
be embedded into the wall in advance, the extruding pipes etc, may have to be
bent and have their length modified to suit the unit.
• Use marking on the mount board as a reference when adjusting the length of the
embedded cooling pipe.
• During construction, give the length of the extruding pipes etc some leeway.
A
Mount board
1
B
Reference marking for flare connection
C
Through hole
D
On-site piping
3.4. Preparing the indoor unit
* Check beforehand because the preparatory work will differ depending on the
exiting direction of the piping.
* When bending the piping, bend gradually while maintaining the base of the
piping exiting portion. (Abrupt bending will cause misshaping of the piping.)
PKA-RP60, 71, 100KAL
Attachment of L-shaped connection pipe
4
Right, left and rear piping (Fig. 3-6)
1. Remove the flare nut and cap of the indoor unit. (Gas pipe only)
2. Apply refrigerating machine oil to the flare sheet surface. (Preparation on
location)
3. Facing the direction in which the L-shaped connection pipe
4
will be removed,
make a quick connection to the indoor unit flare connection opening.
4. Tighten the flare nut using a double open-end wrench. (Fig. 3-9)
Tightening force: 68 to 82 N•m
5. Attach the charge nut
5
to the liquid pipe side joint portion, and check for
leakage of the L-shaped connection pipe
4
connection portion.
Remove the charge nut
5
after completion of the work.
Tightening force: 34 to 42 N•m
6. Cover the flare connection portion with the pipe cover of the L-shaped
connection pipe
4
so that it is not exposed. (Fig. 3-10)
A
L-shaped connection pipe
4
B
Cut-off position (Straight pipe portion)
C
Tightening direction
D
Cover with pipe cover
E
Cover the flare nut connection portion with the pipe cover.
Lower piping (Fig. 3-7)
1. Cut L-shaped connection pipe
4
at the position indicated in (Fig. 3-8).
2. Insert the flare nut that was removed earlier onto the straight pipe side of the cut
L-shaped connection pipe
4
and then flare the end of the pipe.
3. Remove the flare nut and cap of the indoor unit. (Gas pipe only)
4. Apply refrigerating machine oil to the flare sheet surface. (Preparation on
location)
5. Quickly connect the L-shaped connection pipe
4
that has been processed as
described in part 2) to the indoor unit flare connection opening.
6. Tighten the flare nut using a double open-end wrench. (Fig. 3-9)
Tightening force: 68 to 82 N•m
7. Attach the charge nut
5
to the liquid pipe side joint portion, and check for
leakage of the L-shaped connection pipe
4
connection portion.
Remove the charge nut
5
after completion of the work.
Tightening force: 34 to 42 N•m
8. Cover the flare connection portion with the pipe cover of the L-shaped
connection pipe
4
so that it is not exposed. (Fig. 3-10)