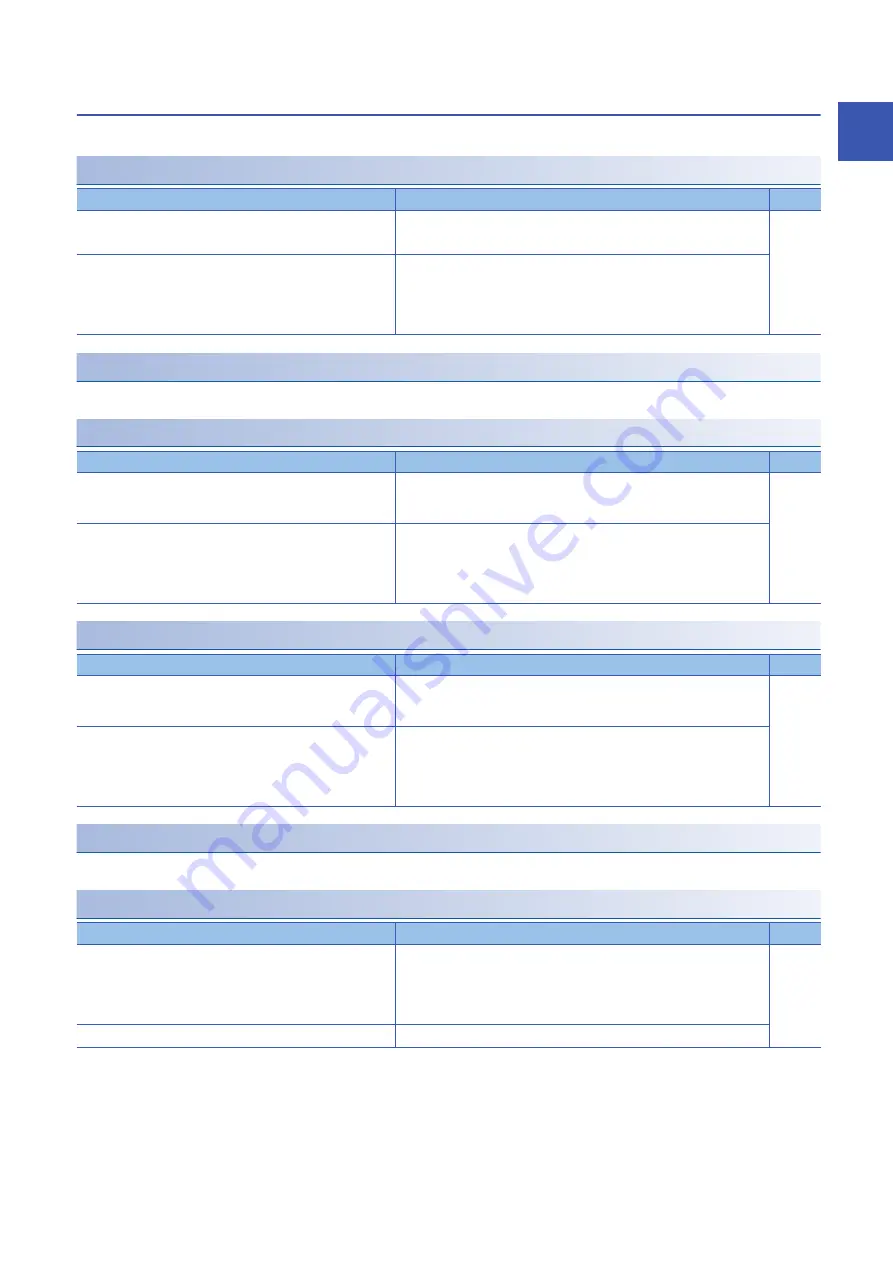
1 SERVO AMPLIFIER TROUBLESHOOTING
1.3 Handling methods for alarms/warnings
21
1
[AL. 017_Board error]
• There is a problem with an internal part of the servo amplifier.
[AL. 017.1_Board error 1]
[AL. 017.3_Board error 2]
Page 21 [AL. 017.1_Board error 1]
[AL. 017.4_Board error 3]
[AL. 017.5_Board error 4]
[AL. 017.7_Board error 7]
Page 21 [AL. 017.4_Board error 3]
[AL. 017.9_Board error 8]
Cause
Check/action method
Model
1.
There is a problem with the current detection
circuit.
Check that this alarm occurs in the servo-on status. If the alarm occurs, the
servo amplifier may have malfunctioned. Replace the servo amplifier.
[JET-G]
2.
There is a problem with the surrounding
environment.
Check the noise, ambient temperature, and other conditions, and implement
appropriate countermeasures for the cause.
If there is noise, take countermeasures to reduce the noise.
Refer to "Noise reduction techniques" in the following manual.
MR-JET User's Manual (Hardware)
Cause
Check/action method
Model
1.
The recognition signal of the servo amplifier
was not read properly.
Disconnect all cables except for those for the power supply, then check the
repeatability. If the failure continues, the servo amplifier may have
malfunctioned. Replace the servo amplifier.
[JET-G]
2.
There is a problem with the surrounding
environment.
Check the noise, ambient temperature, and other conditions, and implement
appropriate countermeasures for the cause.
If there is noise, take countermeasures to reduce the noise.
Refer to "Noise reduction techniques" in the following manual.
MR-JET User's Manual (Hardware)
Cause
Check/action method
Model
1.
There is a problem with rotary switches (SW1/
SW2).
After checking the conditions of the rotary switches, cycle the power, then
check the repeatability. If the failure continues, the servo amplifier may have
malfunctioned. Replace the servo amplifier.
[JET-G]
2.
There is a problem with the surrounding
environment.
Check the noise, ambient temperature, and other conditions, and implement
appropriate countermeasures for the cause.
If there is noise, take countermeasures to reduce the noise.
Refer to "Noise reduction techniques" in the following manual.
MR-JET User's Manual (Hardware)
Cause
Check/action method
Model
1.
There is a problem with the surrounding
environment.
Check the noise, ambient temperature, and other conditions, and implement
appropriate countermeasures for the cause.
If there is noise, take countermeasures to reduce the noise.
Refer to "Noise reduction techniques" in the following manual.
MR-JET User's Manual (Hardware)
[JET-G]
2.
The servo amplifier has malfunctioned.
Replace the servo amplifier.
Содержание MELSERVO-JET MR-JET G Series
Страница 1: ...MR JET User s Manual Troubleshooting MR JET _G MR JET _G N1 Mitsubishi Electric AC Servo System ...
Страница 2: ......
Страница 7: ...5 CONTENTS REVISIONS 104 WARRANTY 105 TRADEMARKS 106 ...
Страница 109: ......