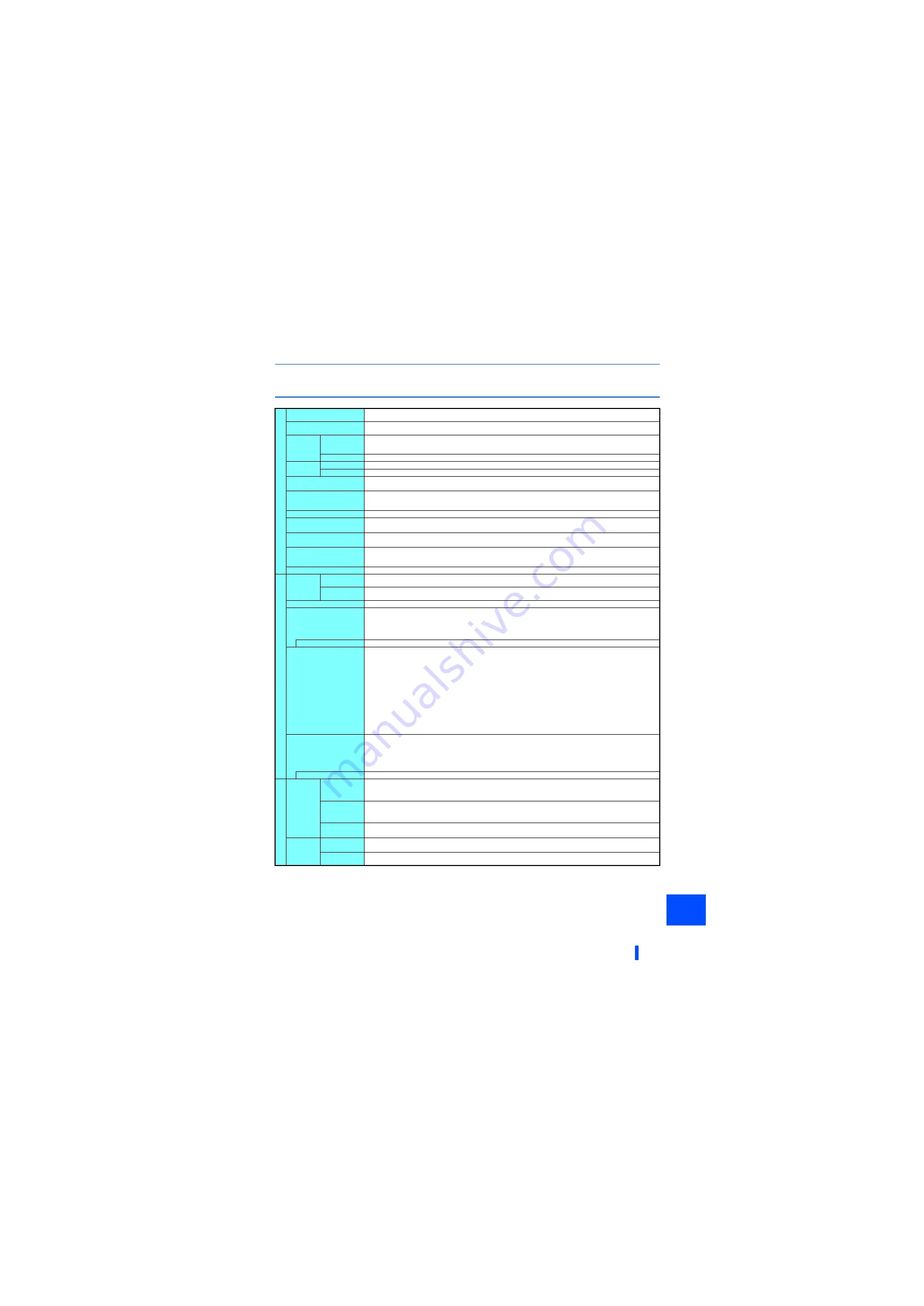
Common specifications
111
6
6.2
Common specifications
C
o
nt
ro
l s
p
e
ci
fi
ca
ti
on
s
Control method
Soft-PWM control, high carrier frequency PWM control (selectable among V/F control, Advanced magnetic flux vector
control, Real sensorless vector control), Optimum excitation control, and vector control
Output frequency range
0.2 to 590 Hz (The upper frequency limit is 400 Hz (200 Hz for the SND rating) under Advanced magnetic flux vector
control, Real sensorless vector control, and vector control
Frequency
setting
resolution
Analog input
0.015 Hz/60 Hz (terminal 2, 4: 0 to 10 V/12 bits)
0.03 Hz/60 Hz (0 to 5 V/11 bits or 0 to 20 mA/approx. 11 bits for terminals 2 and 4, 0 to
±
10 V/12 bits for terminal 1)
0.06 Hz/60 Hz (0 to
±
5 V/11 bits for terminal 1)
Digital input
0.01 Hz
Frequency
accuracy
Analog input
Within
±
0.2% of the max. output frequency (25°C
±
10°C)
Digital input
Within 0.01% of the set output frequency
Voltage/frequency
characteristics
Base frequency can be set from 0 to 590 Hz. Constant-torque/variable-torque pattern can be selected.
Starting torque
SLD rating: 120% 0.3 Hz, LD rating: 150% 0.3 Hz, SND rating: 150% 0.3 Hz, ND rating: 200%
0.3 Hz
(under Real sensorless vector control or vector control
Torque boost
Manual torque boost
Acceleration/deceleration
time setting
0 to 3600 s (acceleration and deceleration can be set individually), linear or S-pattern acceleration/deceleration mode,
backlash countermeasures acceleration/deceleration can be selected.
DC injection brake
(induction motor)
Operation frequency (0 to 120 Hz), operation time (0 to 10 s), operation voltage (0 to 30%) variable
Stall prevention operation
level
Activation range of stall prevention operation (SLD rating: 0 to 120%, LD rating: 0 to 150%, SND rating: 0 to 220%, ND
rating: 0 to 220%, HD rating: 0 to 280%). Whether to use the stall prevention or not can be selected. (V/F control,
Advanced magnetic flux vector control)
Torque limit level
Torque limit value can be set (0 to 400% variable). (Real sensorless vector control, vector control
)
Oper
at
ion
spe
c
if
ic
at
ions
Frequency
setting
signal
Analog input
Terminals 2 and 4: 0 to 10 V, 0 to 5 V, 4 to 20 mA (0 to 20 mA) are available.
Terminal 1: -10 to +10 V, -5 to 5 V are available.
Digital input
Input using the setting dial of the operation panel or parameter unit
Four-digit BCD or 16-bit binary (when used with option FR-A8AX)
Start signal
Forward and reverse rotation or start signal automatic self-holding input (3-wire input) can be selected.
Input signals (twelve
terminals)
Low-speed operation command, Middle-speed operation command, High-speed operation command, Second function
selection, Terminal 4 input selection, Jog operation selection, Selection of automatic restart after instantaneous power
failure, flying start, Output stop, Start self-holding selection, Forward rotation command, Reverse rotation command,
Inverter reset
The input signal can be changed using
Pr.178 to Pr.189 (input terminal function selection)
.
Pulse train input
100k pulses/s
Operational functions
Dancer feedback speed control, tension sensor feedback speed control, tension sensorless torque control, tension sensor
feedback torque control, winding diameter calculation, initial winding diameter calculation, actual line speed detection,
reduction ratio setting, maximum/minimum winding diameter setting, winding diameter / winding length storage, line speed
acceleration/deceleration function, dancer roll break detection, tension PI gain tuning, Speed control proportional gain
compensation, reel change function, taper function, inertia compensation function, mechanical loss compensation
function, maximum and minimum frequency settings, multi-speed operation, acceleration/deceleration pattern, thermal
protection, DC injection brake, starting frequency, JOG operation, output stop (MRS), stall prevention, regeneration
avoidance, frequency jump, rotation display, automatic restart after instantaneous power failure, retry function, carrier
frequency selection, fast-response current limit, forward/reverse rotation prevention, operation mode selection, slip
compensation, droop control, speed smoothing control, auto tuning, applied motor selection, gain tuning, RS-485
communication, Ethernet communication
, dancer control, cooling fan operation selection, stop selection (deceleration
stop/coasting), power-failure deceleration stop function, PLC function, life diagnosis, maintenance timer, current average
monitor, multiple rating, speed control, torque control, pre-excitation, torque limit, test run, 24 V power supply input for
control circuit, safety stop function
Output signal
Open collector output (five
terminals)
Relay output (two
terminals)
Inverter running, Up to frequency, Overload warning, Output frequency detection, Fault
The output signal can be changed using
Pr.190 to Pr.196 (output terminal function selection)
.
Fault codes of the inverter can be output (4 bits) from the open collector.
Pulse train output
50k pulses/s
Indic
at
io
n For meter
Pulse train
output (FM
type)
Max. 2.4 kHz: one terminal (output frequency)
The monitored item can be changed using
Pr.54 FM/CA terminal function selection
.
Current
output
(CA type)
Max. 20 mADC: one terminal (output current)
The monitored item can be changed using
Pr.54 FM/CA terminal function selection
.
Voltage
output
Max. 10 VDC: one terminal (output voltage)
The monitored item can be changed using
Pr.158 AM terminal function selection
.
Operation
panel
(FR-DU08)
Operating
status
Output frequency, output current, output voltage, frequency setting value
The monitored item can be changed using
Pr.52 Operation panel main monitor selection
.
Fault record
Fault record is displayed when a fault occurs. Past 8 fault records and the conditions immediately before the fault (output
voltage/current/frequency/cumulative energization time/year/month/date/time) are saved.
Содержание FR-A842-07700
Страница 71: ...MEMO 70 ...
Страница 91: ...MEMO 90 ...