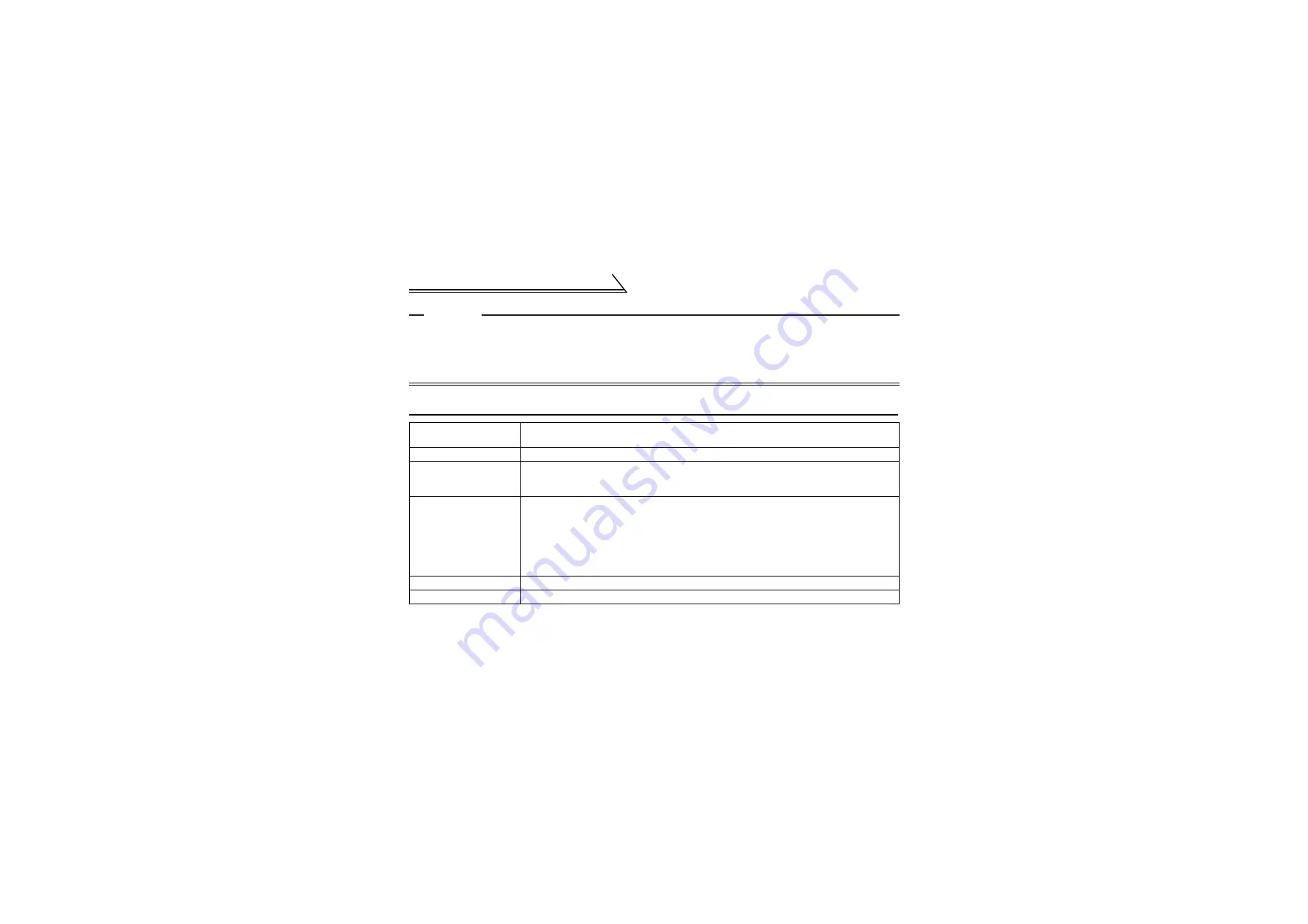
52
ENCODER FEEDBACK CONTROL—A500(L)
4.10 Specifications
*1 Load variation 100% indicates the maximum continuous operation torque value of the motor output characteristic
(refer to the relevent catalog or FR-A500 series technical information) to the running frequency.
CAUTION
During acceleration/deceleration, switching cannot be made using the S-shaped acceleration/
deceleration C switching terminal (X20). When X20 is switched either ON or OFF during either
acceleration or deceleration, the effect of the switch (to select a different acceleration or
deceleration shape) does not take effect until either the acceleration or deceleration has stopped
(i.e. a stable speed has been reached).
Speed variation ratio
±0.02% of the maximum speed (3600r/min) in vector control mode
(load variation 0 to 100% at 6Hz or more). (*1)
Speed control range
1:1000 in vector control mode.
Functions
•
Speed feedback range setting.
•
Feedback gain setting.
•
Encoder rotation direction setting.
DC power supply
A 5VDC power supply is required for the encoder and option unit.
The 5V power supply can be shared between orientation control and encoder feedback
control.
This power supply is optional.
Power supply 5VDC, current capacity 400mA or more.
(Normally approximately 350mA for encoder and 50mA for option unit)
<Power supply example> DENSEI LAMBDA EWS15-5 (5V 3A)
Maximum speed
3600r/min (120Hz)
Frequency response
10 to 20rad/s.