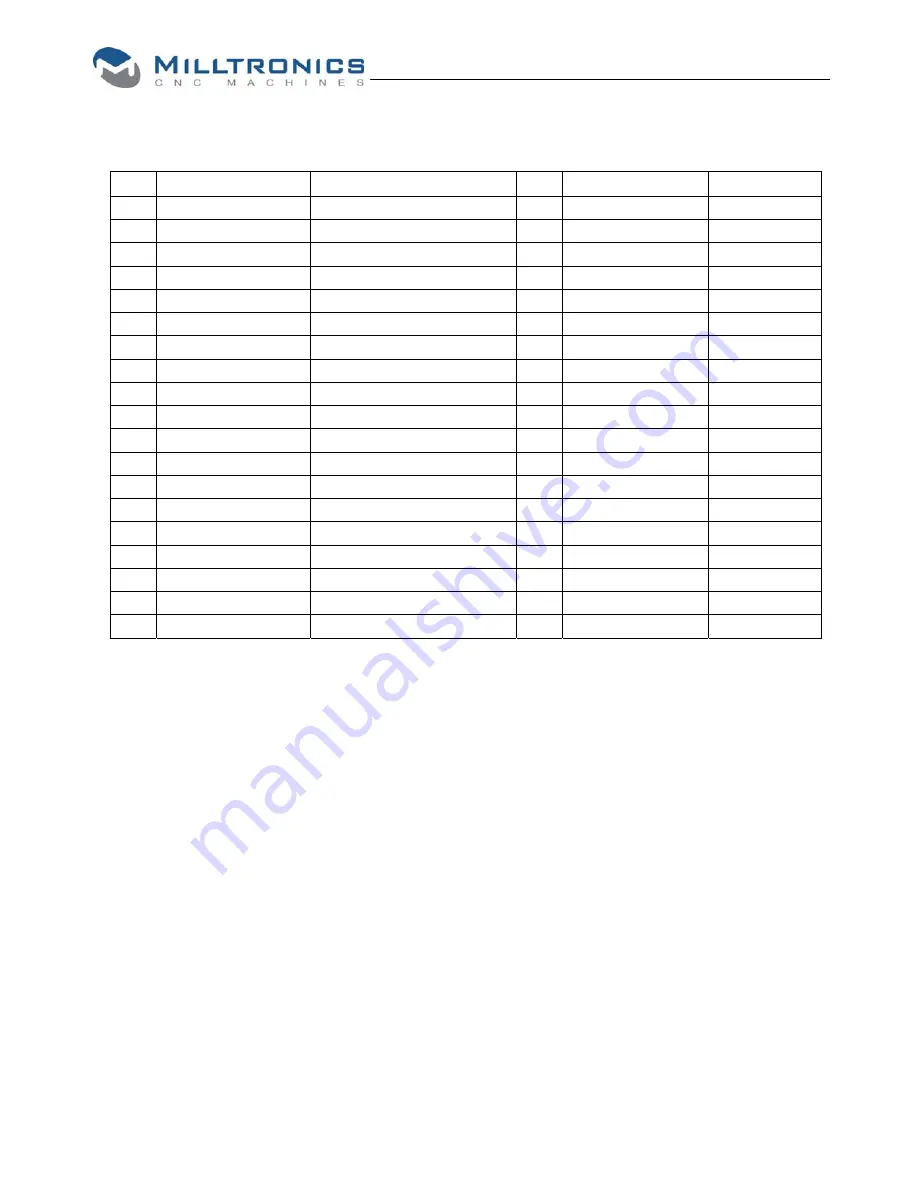
C
HAPTER
8 – P
ARTS
L
ISTS AND
D
RAWINGS
51
Parts List for Hydraulic Chuck
Item Part
no.
Description Q'ty
Remark Milltronics
#
1
3-jaw
chuck
(92HT)
1
NB-212A8
2
E-ARFD-80001-01 Pull tube (92HT)
1
3 E-ARFC-00001-01
Head
stock
(76/92HT)
1
4 E-ARFC-07003-01
Washer
4
M16
5
5001-A16200070
Hex. socket screw
4
M16XP2.0X70L
6 E-ARFC-00002-01
Fixing
block
1
Содержание SL10 Series
Страница 2: ...2 ...
Страница 4: ...iv ...
Страница 6: ......
Страница 19: ...CHAPTER 2 SPECIFICATION 13 SL12 Series Machine Layout 168 4 122 23 74 81 ...
Страница 22: ......
Страница 46: ......
Страница 56: ......
Страница 58: ...Spindle Transmission System 52 ...
Страница 60: ...Spindle Speed Detector 54 ...
Страница 62: ...Headstock C axis option 56 ...
Страница 64: ...Parts Catcher option 58 ...
Страница 66: ...Cut off Detector option 60 ...
Страница 68: ...X Axis 62 ...
Страница 70: ...Z Axis 64 ...
Страница 72: ...Tailstoc 66 k Not shown Tailstock limit switch BNS0003 SW 200 ...
Страница 75: ...CHAPTER 8 PARTS LISTS AND DRAWINGS 69 ntio lly This page inte na unused ...
Страница 76: ...Guarding 70 ...
Страница 78: ...Guarding Door 72 ...
Страница 80: ...Guarding Electrical Box 74 ...
Страница 82: ...76 Solenoid Air FRL and Parts Catcher NU 322 Cap only NU 535 Bowl only NU 477 NU 335 ...
Страница 83: ......
Страница 84: ......
Страница 86: ......
Страница 88: ......
Страница 90: ......
Страница 92: ......