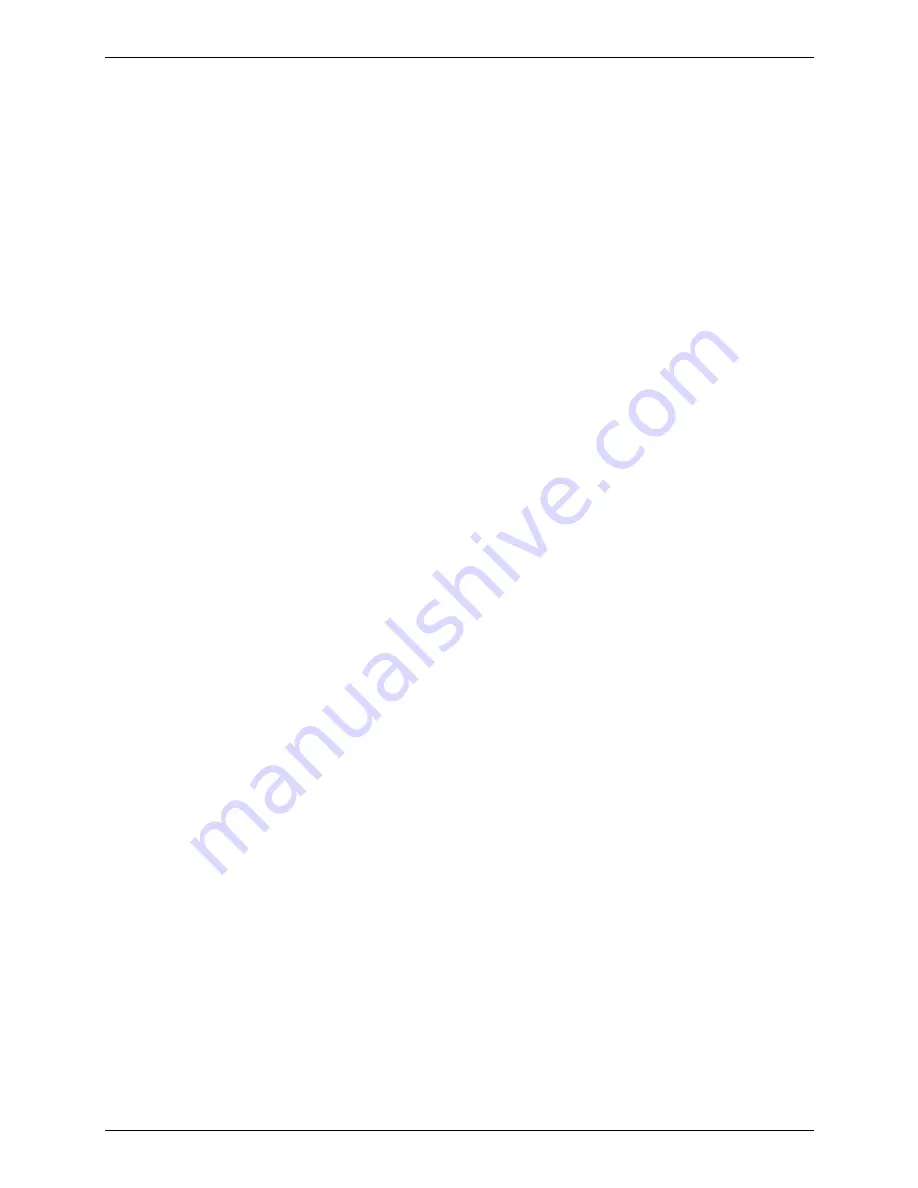
Vacuum Drying and Leakage Checking
Installation
103
7. Vacuum Drying and Leakage Checking
7.1 Purpose of vacuum drying
Eliminating moisture in system to prevent the phenomena of ice-blockage and copper oxidation.
Ice-blockage shall cause abnormal operation of system, while copper oxide shall damage compressor.
Eliminating the non-condensable gas (air) in system to prevent the components oxidizing, pressure
fluctuation and bad heat exchange during the operation of system.
7.2 Selection of vacuum pump
The ultimate vacuum degree of vacuum pump shall be -756mmHg or above.
Precision of vacuum pump shall reach 0.02mmHg or above.
7.3 Operation procedure for vacuum drying
Due to different construction environment, two kinds of vacuum drying ways could be chosen, namely
ordinary vacuum drying and special vacuum drying.
7.3.1 Ordinary vacuum drying
1. When conduct first vacuum drying, connect pressure gauge to the infusing mouth of gas pipe and liquid
pipe, and keep vacuum pump running for 1hour (vacuum degree of vacuum pump shall be reached
-755mmHg).
2 If the vacuum degree of vacuum pump could not reach -755mmHg after 1 hour of drying, it indicates
that there is moisture or leakage in pipeline system and need to go on with drying for half an hour.
3 If the vacuum degree of vacuum pump still could not reach -755mmHg after 1.5 hours of drying, check
whether there is leakage source.
4 Leakage test: After the vacuum degree reaches -755mmHg, stop vacuum drying and keep the pressure
for 1 hour. If the indicator of vacuum gauge does not go up, it is qualified. If going up, it indicates that
there is moisture or leak source.
7.3.2 Special vacuum drying
The special vacuum drying method shall be adopted when:
1. Finding moisture during flushing refrigerant pipe.
2. Conducting construction on rainy day, because rain water might penetrated into pipeline.
3. Construction period is long, and rain water might penetrated into pipeline.
4. Rain water might penetrate into pipeline during construction.
Procedures of special vacuum drying are as follows:
1. Vacuum drying for 1 hour.
2. Vacuum damage, filling nitrogen to reach 0.5Kgf/cm2 .
Because nitrogen is dry gas, vacuum damage could achieve the effect of vacuum drying, but this
method could not achieve drying thoroughly when there is too much moisture. Therefore, special
attention shall be drawn to prevent the entering of water and the formation of condensate water.
3. Vacuum drying again for half an hour.
If the pressure reached -755mmHg, start to pressure leakage test. If it can not reached the value,
repeat vacuum damage and vacuum drying again for 1 hour.
4 Leakage test: After the vacuum degree reaches -755mmHg, stop vacuum drying and keep the pressure
for 1 hour. If the indicator of vacuum gauge does not go up, it is qualified. If going up, it indicates that
there is moisture or leak source.
Содержание U2MRS-12
Страница 6: ...Dimensions 12 Indoor Units 2 Dimensions Model A H 18 K 205 235 24 K 30 K 245 275 36 K 245 275 205 235...
Страница 7: ...Service Space Indoor Units 13 3 Service Space 1000mm 1000mm 1000mm 1000m m...
Страница 13: ...Field Wiring Indoor Units 19 9 Field Wiring...
Страница 20: ...Wiring Diagrams 26 Indoor Units 4 Wiring Diagrams 12K 12K 24K 30K 36K...
Страница 21: ...Wiring Diagrams Indoor Units 27 MTB 24HWDN1 QRC4...
Страница 28: ...Field Wiring 34 Indoor Units 10 Field Wiring 12K 18K 24K 30K 36K...
Страница 32: ...Service Space 38 Indoor Units 3 Service Space...
Страница 34: ...Wiring Diagrams 40 Indoor Units 36K...
Страница 37: ...Indoor Units 43 9 Field Wiring...
Страница 40: ...Dimensions 46 Indoor Units 2 Dimensions...
Страница 41: ...Service Space Indoor Units 47 3 Service Space...
Страница 42: ...Wiring Diagrams 48 Indoor Units 4 Wiring Diagrams 12K 18K...
Страница 46: ...52 Indoor Units 10 Field Wiring 12K 18K...
Страница 48: ......
Страница 51: ...Dimensions Console Type 57 2 Dimensions MFAU 12HRFN1 QRC8 MFA 16HRFN1 QRC8...
Страница 52: ...Service Space 58 Console Type 3 Service Space...
Страница 53: ...Wiring Diagrams Console Type 59 4 Wiring Diagrams MFAU 12HRFN1 QRC8 MFA 16HRFN1 QRC8...
Страница 58: ...Field Wiring 64 Console Type 10 Field Wiring MFAU 12HRFN1 QRC8 MFA 16HRFN1 QRC8...
Страница 64: ...Wiring Diagrams 70 Outdoor Units 4 Wiring Diagrams U2MRS 12...
Страница 65: ...Wiring Diagrams Outdoor Units 71 18K 24K 30K 36K...
Страница 66: ...Wiring Diagrams 72 Outdoor Units...
Страница 67: ...Wiring Diagrams Outdoor Units 73...
Страница 92: ...Refrigerant pipe installation 98 Installation...
Страница 123: ...Troubleshooting Electrical Control System 129 2 4 1 2 Outdoor unit malfunction...
Страница 130: ...Troubleshooting 136 Electrical Control System 2 4 2 3 Up down panel is not closed...
Страница 132: ...Troubleshooting 138 Electrical Control System 2 4 4 For the outdoor unit 2 4 4 1 E0 malfunction...
Страница 134: ...Troubleshooting 140 Electrical Control System 2 4 4 3 E3 malfunction...
Страница 135: ...Troubleshooting Electrical Control System 141 2 4 4 4 E4 malfunction...
Страница 138: ...Troubleshooting 144 Electrical Control System 2 4 4 7 E6 malfunction Only for MOU 36HFN1 QRC4 MOU 36HFN1 QRC8...
Страница 141: ...Troubleshooting Electrical Control System 147 2 4 4 9 P1 malfunction For 36k models...
Страница 142: ...Troubleshooting 148 Electrical Control System 2 4 4 10 P2 malfunction For 36k models...
Страница 143: ...Troubleshooting Electrical Control System 149 2 4 4 11 P3 malfunction...