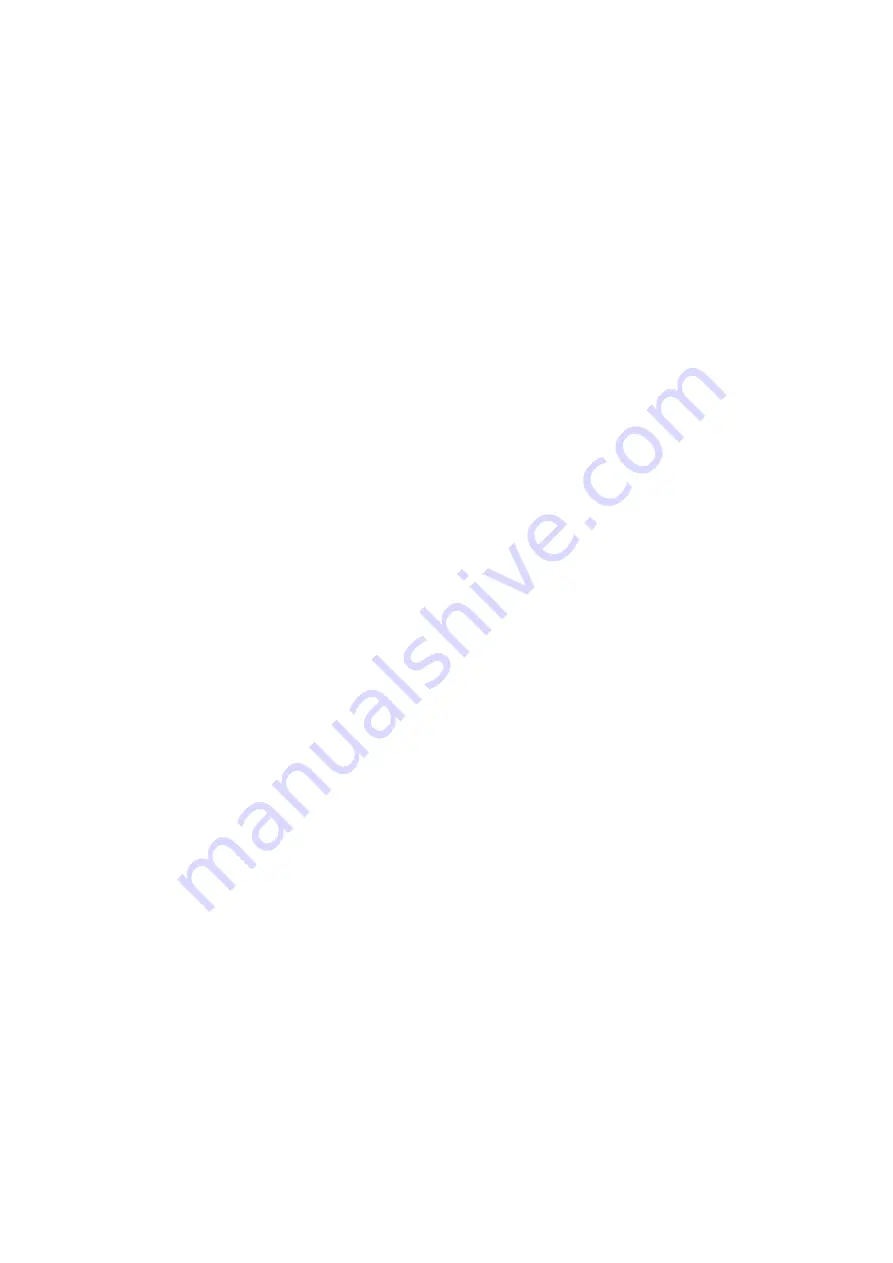
Dear Customer,
May we thank you for having chosen a MHS Group product.
This manual has been prepared to acquaint you with the boiler you have purchased.
Please take time to read it, because the instructions and suggestions on the installation, use and
maintenance of your boiler will enable you to obtain the best results from our high quality product for
a very long time.
CONFORMITY STATEMENT
Regency Premix boilers are manufactured in accordance with the EN656 standard and carry the CE
mark. They comply with the following Directives:
9
90/396
Gas Appliances Directive
9
92/42
Boilers Efficiency Directive
9
73/23
Low Voltage Directive
9
89/893
Electro-Magnetic Compatibility
They comply with Gas Safety Regulations.
Regency Premix boilers are classified as type B23 (the combustion air is coming from the room where
the boiler is installed, there is no draught diverter and the burner fan is placed upstream the
combustion chamber), and are designed for use on gas category I2H (natural gas).
The Manufacturer will not assume any responsibility for the non-observance of any relevant statutory
installation requirements, regulations and codes of practice, or any recommendations and instructions
included in this manual.
INSTALLATION REQUIREMENTS
The equipment must be installed by competent personnel who are suitably qualified in the geld of civil
heating systems.
The boilers need to be connected to:
9
a supply gas system
9
a supply electric system
9
an hydronic heating system
9
a natural draught chimney
The installation of Regency Premix boilers must be in accordance with relevant statutory requirements,
the Gas Safety (Installation and Use) Regulations 1994, Health & Safety at Work Act, Building
Regulations, I.E.E. Regulations, Construction (Design & Management) Regulations 1994, Local
Authority Byelaws, Local Gas Undertaking Regulations, Local & National Water Byelaws, Fire Authority
Regulations and Insurance Company requirements.
The following codes of practice are also applicable:
9
BS6880 Codes of practice for low temperature hot water heating systems of out-put greater than 45
kW. Parts 1,2 & 3 : 1988.
9
CP342 Code of practice for centralised hot water supply, part 2 Buildings other than individual
dwellings.
9
BS6644 1991 specification for gas fired hot water boilers of rated inputs between 60 kW and 2 MW.
9
IGE/UP/2 Gas installation pipework, boosters and compressors on industrial and commercial
premises.
9
CIBSE Guide Reference sections B7, B11 and B13.
9
BS5440 Installation of flues and ventilation for gas appliances of rated input not exceeding 60 kW.
9
British Gas IM/11 Flues for commercial and industrial gas fired boilers and air heaters.
Содержание 001616006
Страница 2: ......
Страница 10: ...1 6 EXPLODED VIEW OF THE BOILER BLOCK AND CASING 1 6 1 BOILERS DRAWING 10 ...