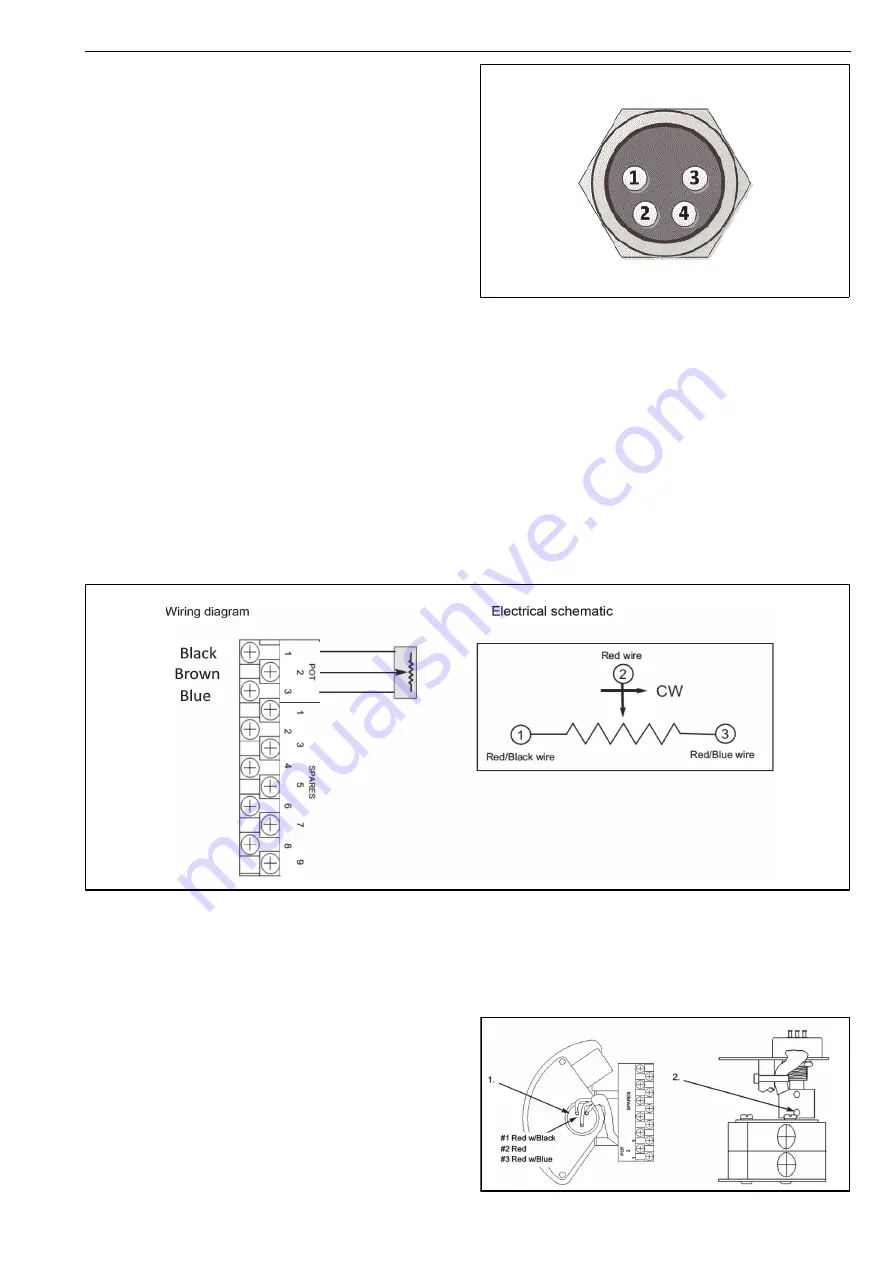
7 ND90 71 en
21
4.5.1 Remote mounting
ND9100H,ND9100F, ND9100P, ND7100H
For applications if there is e.g. heavy vibrations, environ-
ment temperature is very high or access is difficult, there is
available remote position measurement option. In this kind
of applications position sensor is attached to actuator and
ND9000 can be installed further away. Pneumatic piping
between ND9000 and actuator is done as explained in
chapter 4.6 and wiring between position sensor and
ND9000 according to Fig. 13.
There are three different cable lengths available between
ND9000 and remote position sensor: 1.2m, 3m and 30m.
If position sensor is remote mounted to linear actuator,
there are some parameters which have to be defined as fol-
lowing:
valve acting type (VTYP) have to be defined as rotary
valve rotation direction (ROT) have to be defined as
Clockwise to Close (CC)
Remote position sensor for rotary actuators is available also
with limit switch.
Fig. 14
Pin assignment in female connector view (connec-
tor in device)
Pin assignement
Pin# Function
1
Cable Shield Ground (Ground)
2
Potentiometer Plus (Blue)
3
Potentiometer Center (Brown)
4 Potentiometer
Minus
(Black)
4.5.2 Quartz position sensor connections and calibration
Potentiometer Calibration
1.
Operate the actuator to the desired “zero” position.
Connect an ohm meter across the terminals POT 1 &
POT 2 to measure the potentiometer output.
2.
Loosen the bottom set screw and rotate the coupling
until the ohm meter reads approximately 5k Ohms
(assuming a 10K Ohm potentiometer). Retighten the
set screw and verify the ohm meter still reads
approximately 5k Ohms.
3.
Operate the actuator to the desired “100 %” position
(assuming 90 degree rotation) and verify the ohm
meter reads (2.7K Ohms or 7.7K Ohms +/- 10 %,
depending on rotation direction).
4.
Remove all test equipment.
5.
Connect the position sensor cable to the terminal
strip as shown in the above wiring diagram.
6.
Connect the connector end of the position sensor
cable to the ND9000 female connector shown in
Fig. 13.