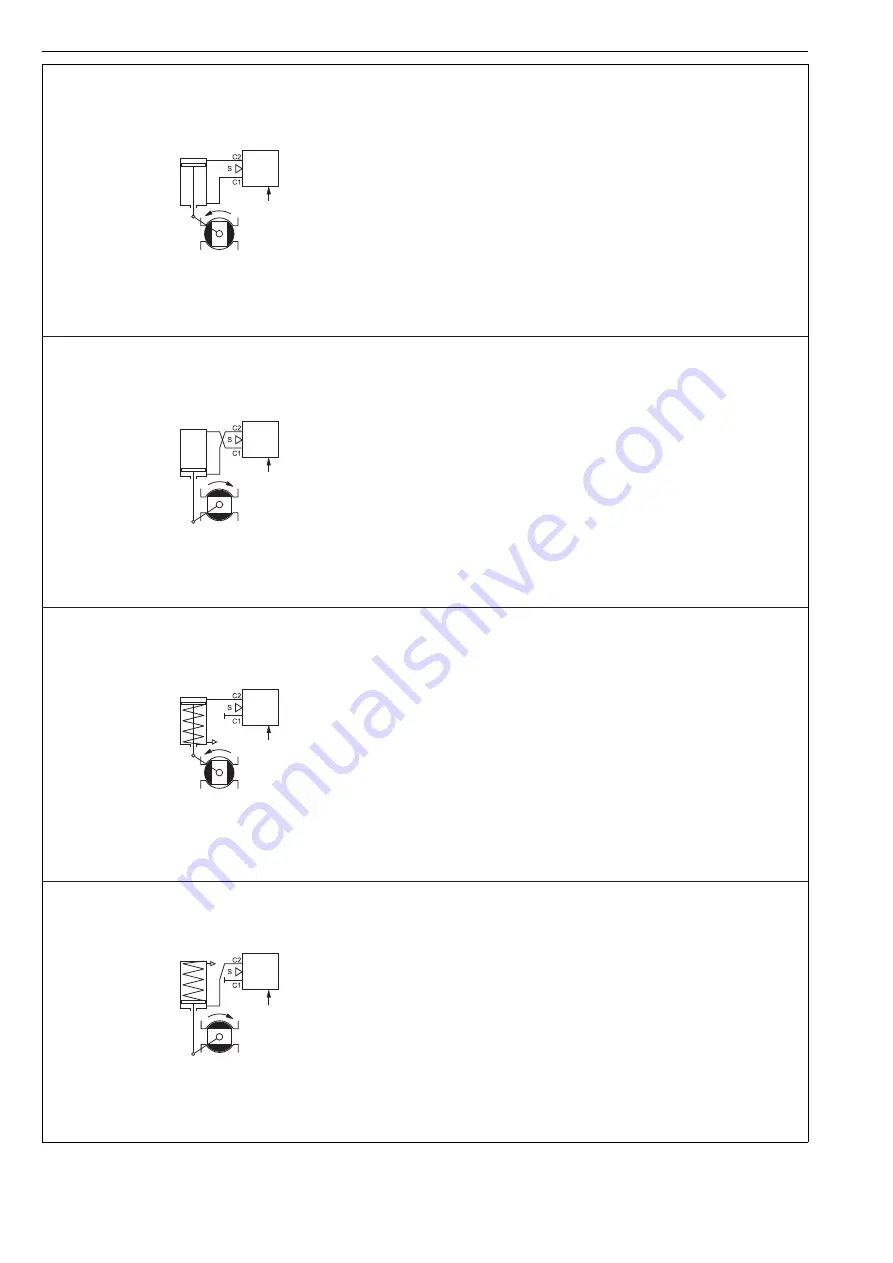
14
7 ND90 71 en
SINGLE-ACTING ACTUATOR, SPRING TO OPEN
SINGLE-ACTING ACTUATOR, SPRING TO CLOSE
DOUBLE-ACTING ACTUATOR, REVERSED PIPING
Increasing input signal to open valve
(not recommended)
Default setting:
DIR = OPE
ROT = cC (close valve to clockwise)
ATYP = 2-A
PFA = OPE
A0, CUTL and VTYP according to valve type
5. Increasing input signal to open valve (shown)
Default setting:
DIR = OPE
ROT = cC (close valve to clockwise)
ATYP = 1-A
PFA = CLO (must be in the spring direction)
A0, CUTL and VTYP according to valve type
7. Increasing input signal to close valve (shown)
Default setting:
DIR = CLO
ROT = cC (close valve to clockwise)
ATYP = 1-A
PFA = OPE (must be in the spring direction)
A0, CUTL and VTYP according to valve type
6. Increasing input signal to close valve
(not recommended)
Default setting:
DIR = CLO
ROT = cC (close valve to clockwise)
ATYP = 1-A
PFA = CLO (must be in the spring direction)
A0, CUTL and VTYP according to valve type
4. Increasing input signal to close valve (shown)
Default setting:
DIR = CLO
ROT = cC (close valve to clockwise)
ATYP = 2-A
PFA = OPE
A0, CUTL and VTYP according to valve type
.
3.
8. Increasing input signal to open valve
(not recommended)
Default setting:
DIR = OPE
ROT = cC (close valve to clockwise)
ATYP = 1-A
PFA = OPE (must be in the spring direction)
A0, CUTL and VTYP according to valve type
DOUBLE-ACTING ACTUATOR
Increasing input signal to open valve (shown)
Default setting:
DIR = OPE
ROT = cC (close valve to clockwise)
ATYP = 2-A
PFA = CLO
A0, CUTL and VTYP according to valve type
2. Increasing input signal to close valve
(not recommended)
Default setting:
DIR = CLO
ROT = cC (close valve to clockwise)
ATYP = 2-A
PFA = CLO
A0, CUTL and VTYP according to valve type
.
1.