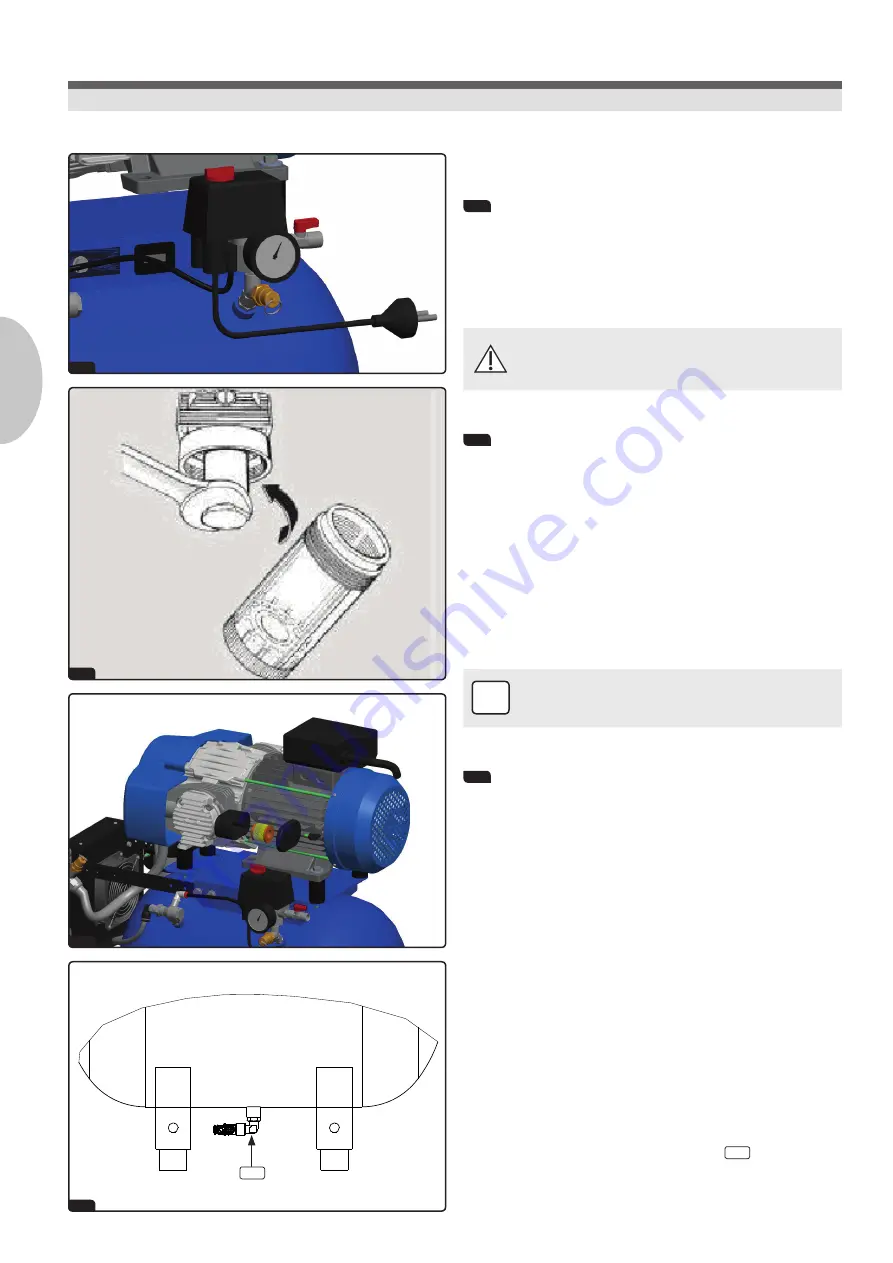
4
3
2
1
4.1
EN
18
17. Service and maintenance
1
Safety valve check
Check if the safety valve functions properly during first use of the
compressor.
Pull the ring at the top of the safety valve to check if air is vented
properly.
Safety valve must not be used to relieve air from the air
receiver! Always protect eyes from compressed air using
safety glasses!
2
Air line filter and dryer prefilter cartridge replacement
Prefilter and dryer prefilter cartridges (0,5 µm and 0,01 µm) must be re
-
placed every year.
Disconnect the compressor from the main supply
Open the air drain cock or the condensate relief from the air receiver
and relief residual pressure contained in the air receiver
Manually unscrew the filter receiver
Unscrew the cartridge as shown in the picture above and replace it with
the new cartridge
Fix again the filter receiver
i
Carefully place the o-ring on the lip of the filter receiver.
Replace the o-ring as necessary.
3
Replacement and cleaning of the air intake filter
Clean the air intake filters every year with compressed air or water, or re
-
place if necessary.
18. Decommissioning and disposal
Decommissioning
If the compressor is not to be used for a longer period of time, it is re-
commended to drain the condensate from the pressure tank. Then the
compressor must be operated for approx. 10 minutes with the condensate
drainage tap open. Afterwards, switch off the compressor at the pressure
switch, close the condensate drainage tap and remove the mains plug.
Disposal
After disconnecting the appliance from the mains electricity supply by
removing the mains plug, the air pressure in the pressure tank must be
released by opening the condensate drainage tap
4.1
.
When disposing of the compressor, all necessary safety precautions must
be taken in order to avoid harm to persons or objects.
Service and maintenance
Decommissioning and disposal
Practice personnel, technicians