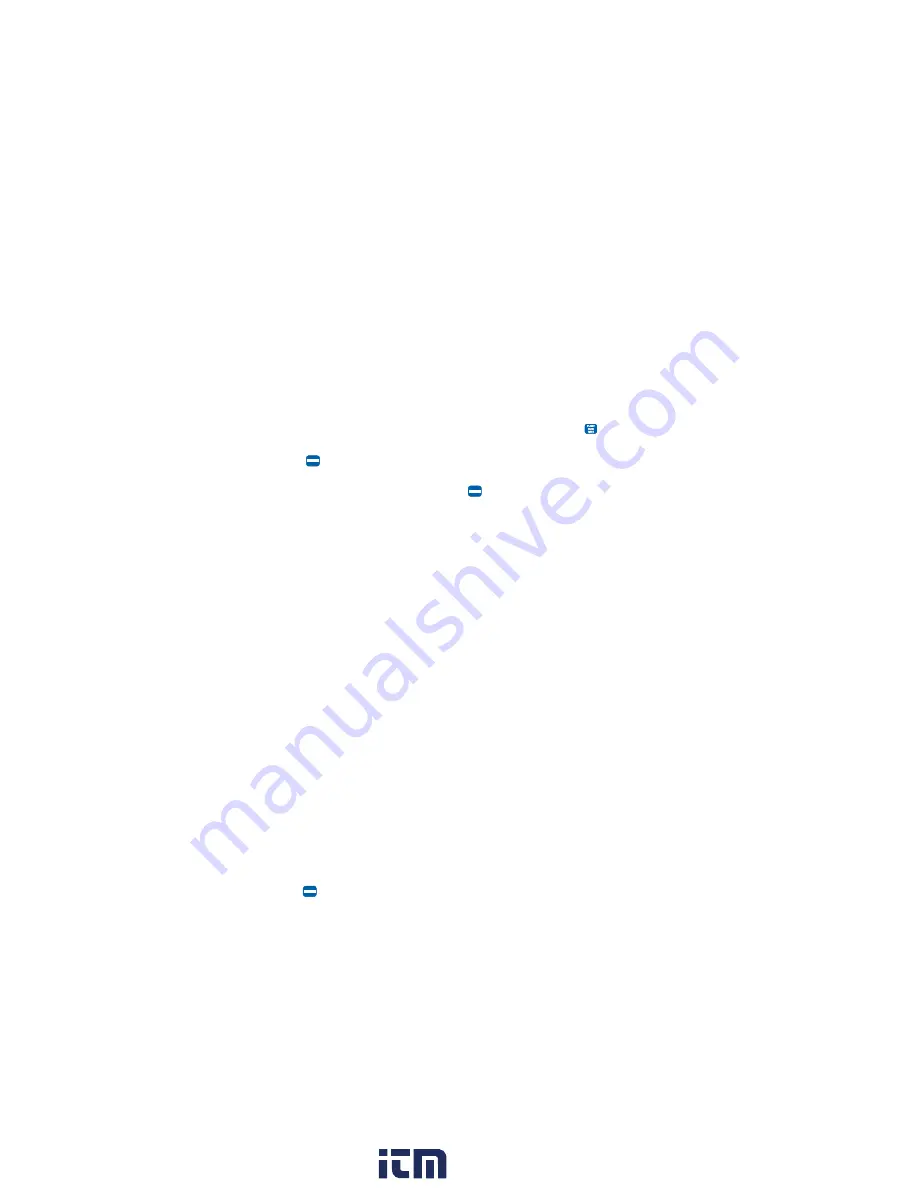
8
In the Secure menu the value of
PSF
is programmed
for the action of the MPC based on the condition of a
seal failure. If set to ˝
AUt0
˝ when pump moisture sensor
indicates that there is a seal failure condition then
the corresponding pump seal failure lamp is lit on the
controller. The pump will remain in service with only the
lamp indication of failure. The lamp will be turned off
automatically when the seal failure condition has ceased.
If
PSF
is set to ˝
rES
˝ when pump moisture sensor
indicates that there is a seal failure condition then
the corresponding pump seal failure lamp is lit on the
controller. If the MPC is only being used with one pump
or being used with two pumps with the lead/lag function
turned off then no action is taken by the MPC with the
operation of the pumps. The failure indication lamp will
be manually reset as described in the next paragraph. If
the MPC is being used with two pumps with the lead/lag
function turned on then the failed pump will automatically
become the lag pump, the remaining pump will become
the lead pump, and the alternation will be discontinued.
The lamp indication and pump alternation can be
manually reset as described in the next paragraph.
Once the pump has been repaired the seal failure
action can be reset with the values of
P1SF
and
P2SF
in
the Secondary menu. The item
P1SF
or
P2SF
will display
FA1L
if the corresponding pump has met the condition of
a seal failure. Press the
ENTER key to reset. If the
pump moisture sensor is still in the fail condition then the
control will not reset. If the moisture sensor is no longer
in the fail condition then the display will revert to ˝----˝.
OVER TEMPERATURE OPERATION
Most pumps have an installed normally closed
thermostat for over temperature protection of the pump.
The thermostat has a preset value from the pump
manufacturer at which point the pump needs to be shut
down. The Mercoid
®
MPC detects when the thermostat
signal changes to open and shuts down the pump.
In the Secure menu the value of
P0t
is programmed for
the action of the MPC based on the condition of the
over temperature. When the pump temperature sensor
indicates that there is an over temperature condition the
pump will be held out of service and the corresponding
pump over temperature lamp is lit on the controller. If
using the MPC with two pumps with the lead/lag function
turned on then the failed pump will automatically be
taken out of service, the remaining pump will become
the lead pump, and the alternation will be discontinued.
When controlling two pumps with the lead/lag function off
the failed pump will automatically be taken out of service
and the remaining pump will be controlled by the
SP1H
and
SP1L
set points.
If
P0t
is set to ˝
AUt0
˝ then the pump will be automatically
placed back into service and the lamp turned off when
the over temperature condition has ceased. If set to
˝
rES
˝ then the pump will remain out of service and the
lamp lit until the corresponding manual reset
P10t
or
P20t
is reset in the Secondary menu (described in the
next paragraph). The pump cannot be brought back into
service until the over temperature condition has ceased.
Once the pump has cooled down the MPC Pump
Controller can be reset with the values of
P10t
and
P20t
in the Secondary menu. The item
P10t
or
P20t
will
display
FA1L
if the pump has met the condition of over
temperature. Press the
ENTER key to reset. If the
pump temperature sensor is still in the fail condition then
the control will not reset. If the temperature input is no
longer in the fail condition then the display will revert to
˝----˝.
ANALOG RETRANSMISSION OPERATION
The analog retransmission allows the Process Variable
to be sent as an analog signal to an external device.
The signal may be either 2-10 VDC (option RV) or 4-20
mADC (standard). The output may be changed in the
field from one to the other by the toggle switch located on
the top printed circuit board, factory standard is mADC.
Wire the output as shown on page 1.
To set up the analog retransmission, first determine the
scale range that the analog signal will represent. The
maximum scale is 9999 counts. In the Secure menu
set
P0L
for the scale value that will be represented by
the low end of the analog signal (2 V or 4 mA). Set
P0H
for the scale value that will be represented by the high
end of the analog signal (10 V or 20 mA). Operation
is automatic. There are no further programming steps
required. The values of
P0L
and
P0H
must be within the
programmed scale range. The scale range is set by the
SCAL
and
SCAH
in the Secure menu.
PUMP RUN TIME OPERATION
The pump run time is indicated in hours of operation
since the last time that the run time meter was reset
for a specific pump. The Pump Run Time key on the
front of the unit will display run time for both pumps when
depressed. Run time for pump 1 is in the top display and
pump 2 is in the lower display. To reset the pump run
time go to the menu items
P1rn
and
P2rn
in the Secondary
Menu. When in the corresponding menu item hold the
ENTER button for approximately two seconds. The
display will blank out for about 1 second and the run time
will display 0. These menu items can be locked out by
the
PrSt
menu item in the Secure Menu.
OPTION 232, 485 SERIAL COMMUNICATION
OPERATION
The serial communications options allow the control to
be written to and read from a remote computer or other
similar digital device. Communication is allowed either
through a RS-485 (Option 485) port, or a RS-232 (Option
232) port.
Wire the communication lines as shown on page 5.
Wiring for the RS-485 is run from control to control in
a daisy chain fashion with a termination resistor (120
Ω) across the transmit and receive terminals of the last
control in the chain. Set the RS-485 DIP switch for half
or full duplex as appropriate for your application. The DIP
switch is located on the communications board plugged
into the center of the bottom board of the control.
Select the control address and communication baud
rate with the Addr and bAUd menu items in the Secure
Menu. THE BAUD RATE AND ADDRESS MENU ITEMS
WILL TAKE EFFECT ON THE NEXT POWER UP OF
THE CONTROL. BE SURE TO POWER CYCLE THE
CONTROL BEFORE USING THE NEW BAUD RATE
AND ADDRESS.
In operation, you have the option of preventing a write
command from the host computer. To prevent the host
from writing to the control change the L0rE menu item in
the Secondary Menu to L0C. To allow the host to write
commands to the control set L0rE to rE. (The host does
have the ability to change the L0rE state, but it is not
automatic.)
If your system depends on constant reading or writing
to and from the host, you may wish to set the No Activity
Timer (
nAt
) to monitor the addressing of the control.
When the
L0rE
is set to
rE
and the
nAt
is set to any value
other than
0FF
, the control will expect to be addressed
on a regular basis. If the control is not addressed in the
time set by the value of
nAt
, then the control will display
the error message
CHEC
LorE
. To clear the message set
L0rE
to
L0C
.
www.
.com
1.800.561.8187