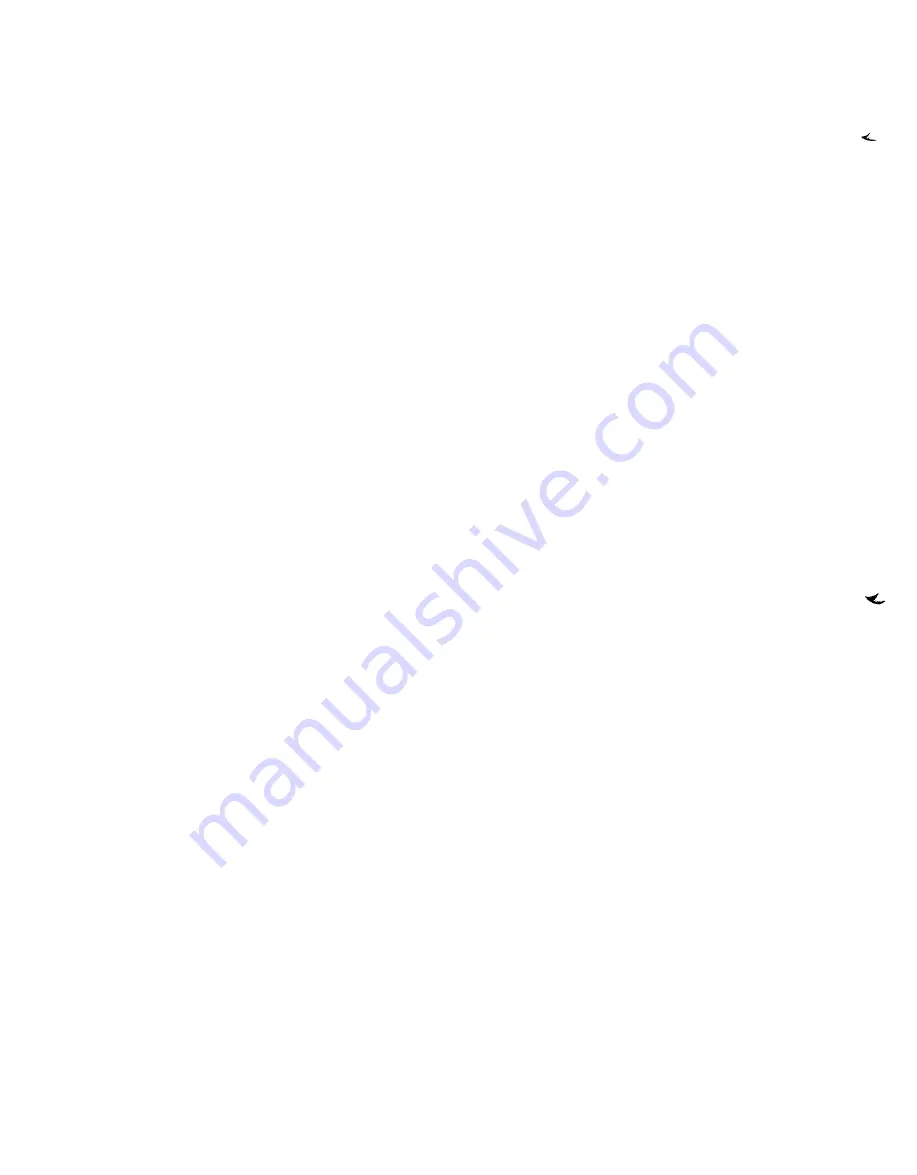
2.
3.
4.
5.
6.
7.
FORCED CIRCULATION OF ANTIFREEZE THROUGH
THE WATER CIRCUITS IS THE ONLY SURE METHOD
OF AVOIDING TROUBLE.
Take measures to prevent the shutoff valve in the water
supply line from being accidentally turned on.
If a cooling tower is used and if the water pump will be
exposed to freezing temperatures, be sure to remove the
pump drain plug and leave it out so that any water which
may accumulate will drain away.
Open compressor disconnect switch, and remove
Fusetrons. If transformer is used for control voltage, the
disconnect must remain on to provide power to oil heater.
Set compressor switch to OFF position. To insure against
the possibility of an accidental start, remove relay R7 in
each control panel.
Check for corrosion and clean and paint rusted surfaces.
Clean and flush water tower for all units operating on a
water tower. Make sure tower “blowdown” or bleedoff is
operating. Set up and use a good maintenance program
to prevent “liming up” of both tower and condenser. It
should be recognized that atmospheric air contains many
contaminants which increase the need for proper water
treatment. The use of untreated water may result in cor-
rosion, erosion, sliming, scaling or algae formation. It is
recommended the service of a reliable water treatment is
required-McQuay assumes no responsibility for the
results of untreated or improperly treated water.
Remove condenser heads at least once a year and clean
condenser tubes.
ANNUALSTARTUP
A dangerous condition can exist if power is applied to a faul-
ty compressor motor starter which has been burned out. This
condition can exist without the knowledge of the person start-
ing the equipment.
This is a good time to check all the motor winding
resistance to ground. Annual checking and recording of this
resistance will provide a record of any deterioration of the
winding insulation. All new units have well over 100 megohms
resistance between any motor terminal and ground.
Whenever great discrepancies in readings occur or uniform
readings of less than 5 megohms are obtained, the motor
cover should be removed for inspection of the winding prior
to starting the unit. Uniform readings of less than 5 megohms
indicate motor failure is imminent and motor should be re-
placed or repaired. Repair before failure occurs can save a
great deal of time and labor expended in the cleanup of a
system after motor burnout.
1.
2.
3.
4.
5.
6.
The control circuit should be energized at all times. If the
control circuit has been off and oil is cool, energize oil
heaters and allow 24 hours for heater to remove refrigerant
from the oil before starting.
Check and tighten all electrical connections.
Replace the drain plug in cooling tower pump if it was
removed at shutdown time the previous season.
Install Fusetrons in main disconnect switch (if removed).
Reconnect water lines and turn on supply water. Flush out
condenser and check for leaks.
Refer to the procedures of “Preliminary Checks Before
Starting” before energizing the compressor circuit.
REPAIR OF SYSTEM
PUMPING DOWN
If it becomes necessary to pump the system down, extreme
care should be used to avoid damage to the water chiller due
to freezing. Always make sure that full water flow is main-
tained through the chiller while pumping down. To pump
system down, close all liquid line valves. With all liquid line
valves closed and water flowing through chiller, start the com-
pressor. In order to pump system down as far as possible,
it will be necessary to bypass the low pressure override switch
and jumper the low pressure cutout. Set temperature module
to manual load position. Vanes must be open while pump-
ing down to avoid a surge or other damaging condition.
Operate machine until the suction pressure stabilizes at
approximately 20 to 25 psig.
Stop the machine. Allow pressure to buildup. Repeat this
procedure 3 times.
After the system has been pumped down, the gas pressure
remaining will have to be purged before the machine can be
serviced.
PRESSURE TESTING
No pressure testing is necessary unless some damage was
incurred. After repairs are made, pressure test the system
at a pressure that does not exceed the standby pressure in
the condenser. (A test pressure higher than condenser
pressure would open the discharge check valve and allow
flow of test pressure into condenser). In cases where the en-
tire refrigerant charge is lost, refer to the following para-
graphs. The evacuation procedure can be followed in both
cases.
Page 16 I IM 307
LEAK TESTING
In case of the loss of the entire refrigerant charge, the unit
should be checked for leaks prior to charging the complete
system. This can be done by charging only enough refrigerant
into the system to build the pressure up to approximately 10
psig and adding sufficient dry nitrogen to bring the pressure
up to a maximum of 125 psig and then leak test with Halide
or electronic leak detector. CAUTION: DO NOT USE OXY-
GEN TO BUILD UP PRESSURE AS A SERIOUS EXPLO-
SION CAN RESULT. A pressure regulating valve should
always be used on the drum being used to build the system
pressure. Also, do not exceed the test pressure given above.
When the test pressure is reached disconnect the gas
cylinder.
If any leaks are found in welded or silver soldered joints
or if it is necessary to replace a gasket, relieve the test
pressure in the system before proceeding. For copper joints,
silver solder is recommended.
After making any necessary repair, the system should be
evacuated as described below.
EVACUATION
After it has been determined that there are no refrigerant
leaks, the system should be evacuated using a vacuum pump
with a capacity of approximately 3 cu. ft/min. and that will
reduce the vacuum to at least 1 millimeter (1000 microns).
A mercury manometer, electronic or other type of micron
gauge should be connected at the farthest point from the
vacuum pump. For readings below 1 millimeter, the electronic
or other micron gauge should be used.