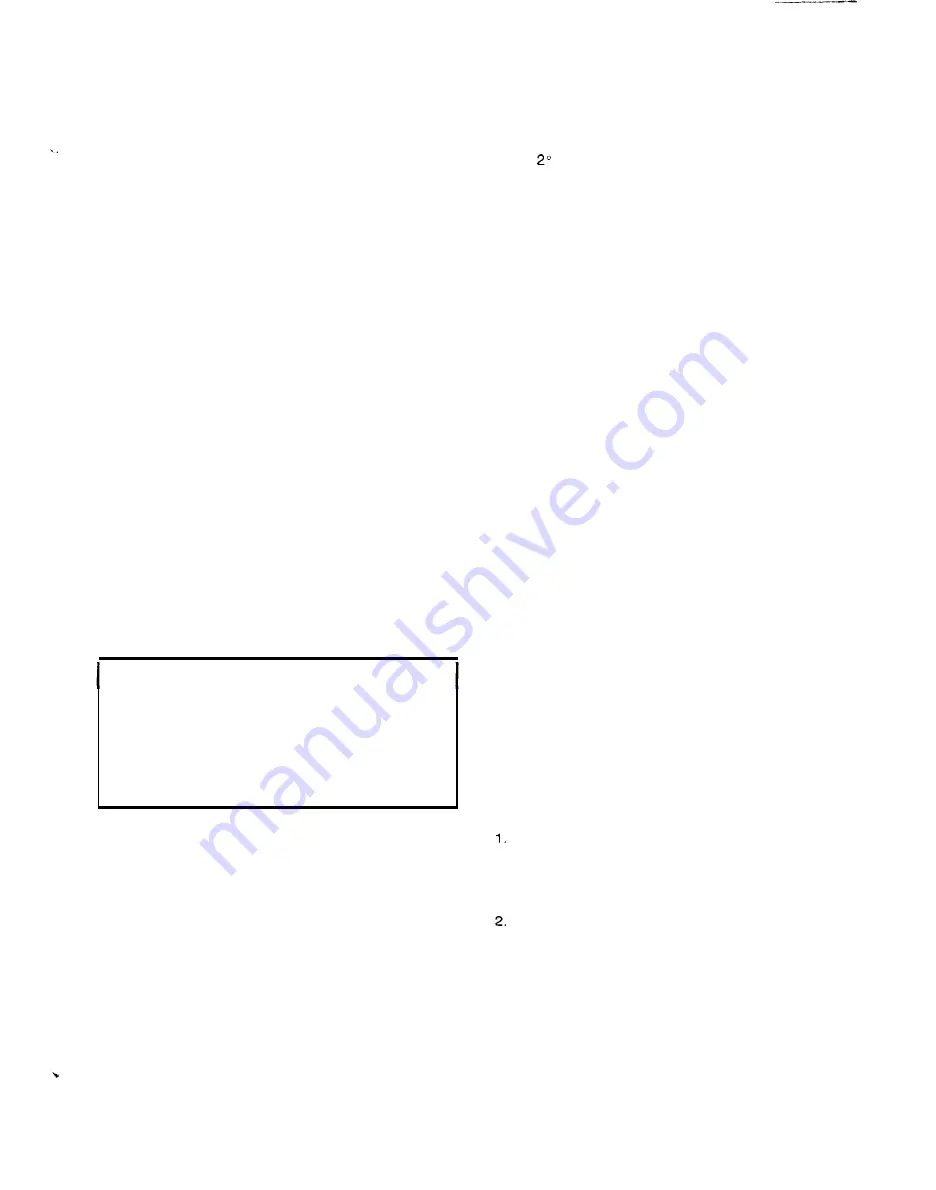
MAINTENANCE
ROUTINE MAINTENANCE
LUBRICATION (See CAUTION)
After the system is once placed into operation, no other ad-
ditional oil is required except in the event that repair work
becomes necessary to the oil pump or unless a large amount
of oil is lost from the system due to a leak.
If oil must be added with the system under pressure, use
a hand pump with its discharge line connected to the ser-
vice valve at the bottom of the oil pump. (The CEO50 com-
pressor with its internal oil pump is equipped with an oil ser-
vice valve on the compressor).
CHANGING OIL FILTERS (See CAUTION)
CEO50 Compressors-If the unit is equipped with a suction
line service valve, close this valve and close the valve on the
motor cooling liquid line to isolate the compressor. Vent the
refrigerant pressure from the compressor. Remove the filter
cover and the old filter and install the new filter, open end
first. Replace the cover using a new gasket. Reopen the suc-
tion and liquid line valves.
If the unit is not equipped with a suction line service valve,
the unit will have to be pumped down in order to remove the
pressure in the compressor before removing the cover and
changing the filter. Refer to later section for pumpdown
procedure.’
CEO63 and Larger Compressors-The oil filter in each of
these machines can be changed by simply isolating the filter
cavities. Close the oil discharge line service valve at the oil
pump (at the filter on CE126). Remove the filter cover; some
foaming may occur but the check valve should limit leakage
from other compressor cavaties. Remove the filter, replace
with new element and replace filter cover using new gasket.
Reopen valve in pump discharge line.
When the machine is operated again, the oil level should
be checked to determine if oil needs to be added to main-
tain proper operating level.
CAUTION
Improper servicing of the lubrication system, including
the addition of excessive or incorrect oil, substitute
quality oil filter, or mishandling of the equipment under
pressure is hazardous. Only authorized and trained ser-
vice personnel should attempt this service. For qualified
assistance, contact your local McQuay Service
technician.
REFRIGERANT CYCLE
Maintenance of the refrigerant cycle consists of maintaining
a log of the operating conditions, and assuring the unit has
the proper oil and refrigerant charge.
At every inspection, the oil, suction and discharge
pressures should be noted and recorded, as well as con-
denser and chiller water temperatures.
The suction line temperature at the compressor should be
taken at least once a month. Subtracting from this, the
saturated temperature equivalent of the suction pressure will
give the superheat. Extreme changes in superheat over a
period of time will indicate losses of refrigerant or possible
deterioration of the expansion valves. Proper superheat set-
ting is
to 6°F at full load.
ELECTRICAL SYSTEM
Maintenance of the electrical system involves the general re-
quirement of keeping contacts clean and connections tight
and checking on specific items as follows:
1.
2.
3.
4.
5.
6.
The compressor current draw should be checked and com-
pared to nameplate RLA value. Normally the actual cur-
rent will be lower since the nameplate rating represents
full load operation. Also check all pump and fan motor
amperages and compare with nameplate ratings.
Inspection should verify that the oil heaters are operative.
The heaters are insert cartridge type and can be
checked by ammeter reading. They should be energized
whenever power is available to the control circuit
(whenever compressor is inoperative). When the com-
pressor starts the heaters are de-energized.
At least once a year, all safety controls except compressor
overloads should be made to operate and their operating
points checked. Any control may shift its operating point
as it ages, and this must be detected so the controls can
be readjusted or replaced. Pump interlocks and flow swit-
ches should be checked to assure they interrupt the con-
trol circuit when tripped.
Contactor in the motor starter should be inspected and
cleaned annually. Tighten all terminal connections.
The compressor motor resistance to ground should be
checked and logged annually. This log will track insula-
tion deterioration. A reading of 5 megohms or less in-
dicates possible insulation failure and should be further
checked.
The centrifugal compressor must rotate in the direction
indicated by the arrow on the casting near the rotation
sightglass. If the operator has any reason to suspect that
the power system connections may have been altered, the
compressor should be jogged to check rotation. For
assistance, call McQuay Service.
CLEANING AND PRESERVING
A common cause of service calls and equipment malfunc-
tion is dirt. This can be prevented with normal maintenance.
The system components most subject to dirt are:
Permanent or cleanable filters in the air handling equip-
ment must be washed in accordance with the manufac-
turer’s instructions; throwaway filters should be replaced.
The frequency of this service will vary with each
installation.
Remove and clean strainers in chilled water system, oil
cooler line and condenser water system at every
inspection.
SEASONAL SERVICING
Prior to shutdown periods and before starting again, the
following service procedures should be completed.
ANNUAL SHUTDOWN
1. Where freezing temperatures may be encountered, the
condenser and chiller water piping should be disconnected
from the supply and drained of all water. Dry air blown
through the condenser will aid in forcing all water out.
Removal of condenser heads is also recommended. The
condenser and evaporator are not self-draining. Water per-
mitted to remain in the piping and vessels will rupture
these parts if subjected to freezing temperature.
IM 307
/
Page 15