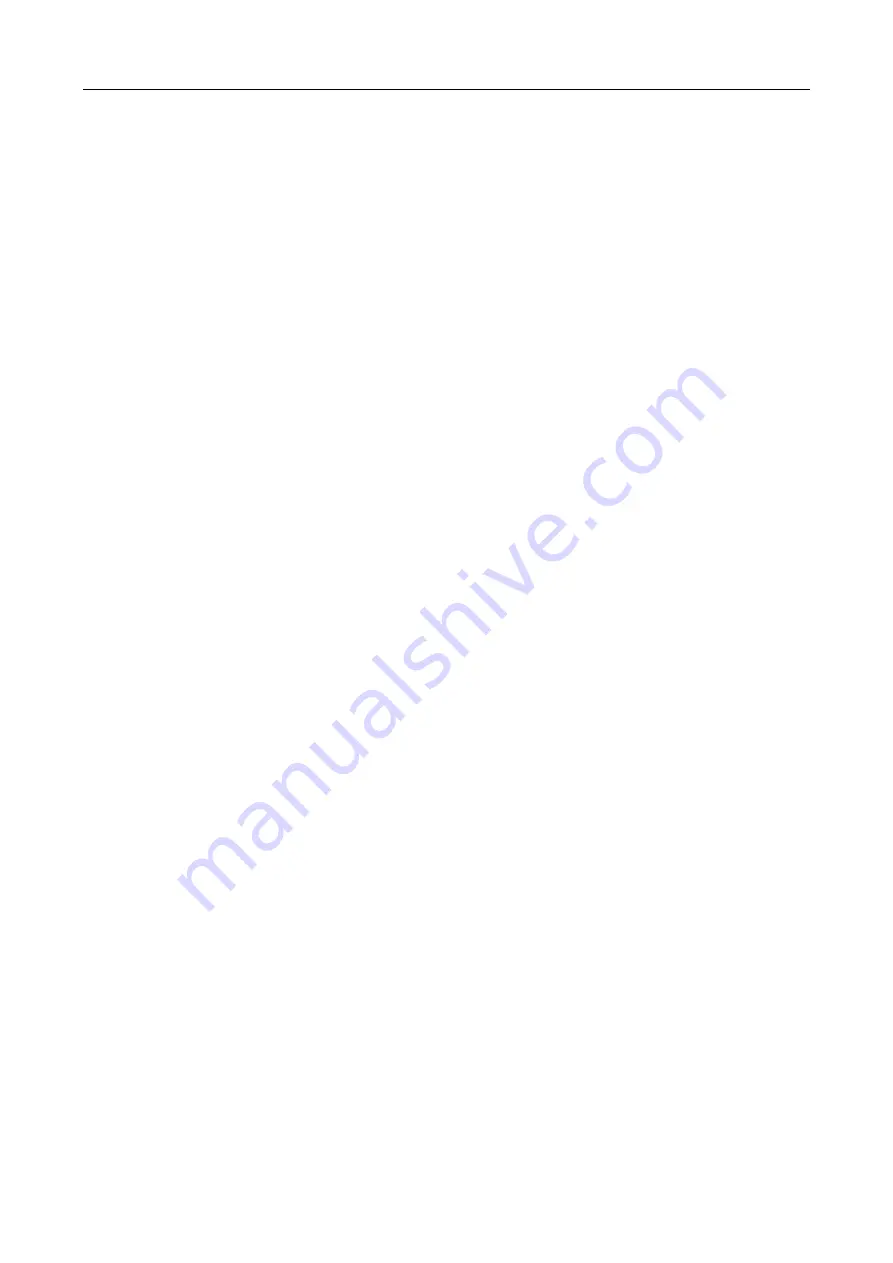
54
GENERAL SERVICING
Servicing Rotor and Rotor Bearings (Econ Flail head only)
To dismantle a rotor, rotor bearing and motor assembly, first remove the motor guard and
disconnect the hose connections to the motor. It is important either to plug the hoses, or
connect them together using an adaptor - if left open on the ground they will siphon empty
the hydraulic tank.
Keep hoses and connections clean at all times.
For easy access now turn the cutting head so that the end opposite the motor stands on
the ground, the rotor shaft now being in the vertical position - the end plate should be
rested on blocks to give a ground clearance of 4" (100mm) - this allows space for the
bearing bolts to be removed.
Remove the bolts holding the motor and bearing to the end plate - withdraw the motor
vertically from the rotor shaft, being careful not to loose the 6 drive rollers which may be
sticking to the motor drive adaptor. Turn the rotor shaft until it is possible to unfasten the
grub screws in the bearing collar. (Note: these circular flanges are only fitted on certain
machines). In 1973 new bearings with additional covers were fitted, there are two holes in
the circular flanges at the end of the rotor shaft which allow access for the allen key.
Remove bolts from the other bearing through the hole where the motor has been removed,
tap the bearing down onto the shaft and withdraw the rotor shaft complete with its bearings
from the mainframe.
Remove the circlip, from the drive end. The bearing can now carefully be knocked off the
rotor shaft using a wood or leather mallet. Check the bearings for excessive wear on the
ball race seat, on the spherical ball seat and also check if the seals are intact.
When assembling the rotor, reverse the previous operations to the point of refitting the
motor. At this stage the bottom (nearest ground) bearing bolts should be in place but not
tightened and the top bearing in line with the holes in the end plate. Locate the six drive
rollers in the motor drive adaptor holding then in place with either thick grease or a rubber
band. Line the six rollers up with the mating holes in the end of the rotor shaft and fit
carefully together, allowing the motor spigot to locate through the hole in the end plate and
into the mating recess in the bearing housing.
Now fit the bolts and ‘feel’ the motor shaft and bearing into a free concentric position
before tightening the bolts by moving the rotor end bearing on its loose bolts. The rotor
shaft should rotate freely without tight spots after these bolts are tightly secured. Fasten
the bottom bearing bolts, grub screws in the bearings, hoses and motor guard. In fitting the
bearings remember to position the grease nipple in an accessible position for lubricating it.
The rotor, whilst dismantled, should be checked for straightness - maximum bow at centre
is 1/16th of an inch (0.58mm) - flail lugs checked for weld fatigue, loss of balance weights
from end 10" diameter plates. If there is any undue vibration when the rotor is running,
then this is almost certainty caused by unbalance. If you have any doubt, return the rotor
(minus flails) for factory re-balance. Always check that a complete set of flails is fitted,
replace broken ones and also ensure that they are free to swing in their attachment.
Содержание ECON HEDGEMASTER Mk3
Страница 3: ......
Страница 9: ......
Страница 15: ......
Страница 17: ......
Страница 39: ...22 ARM OPERATION SWITCHBOX CONTROL ...
Страница 43: ...26 ARM OPERATION MONOLEVER CONTROL ...
Страница 53: ...36 ARMHEAD OPERATION JOYSTICK CONTROLS ...
Страница 54: ...37 ARMHEAD OPERATION JOYSTICK CONTROLS ...