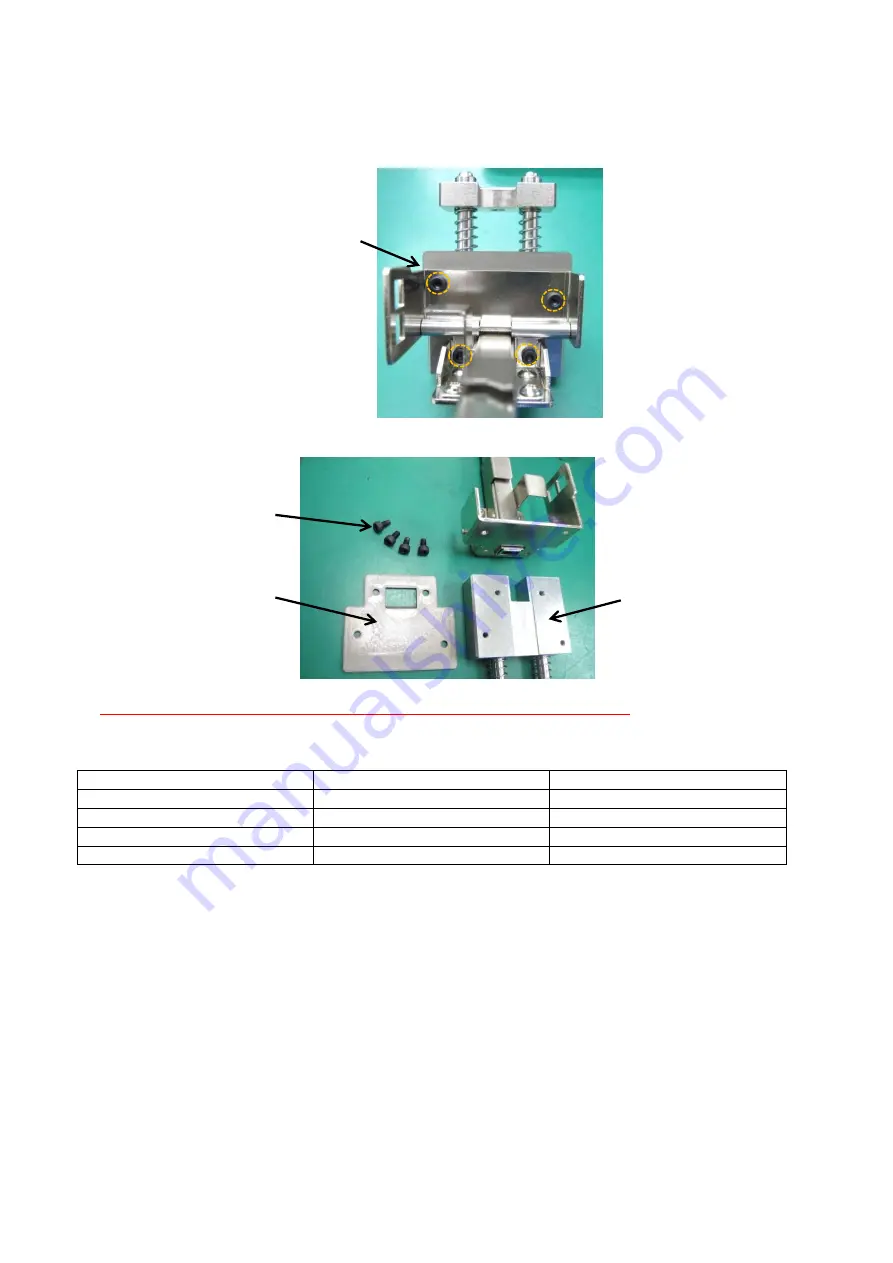
11
3-5 Dissembling and Reassembling a Stapler Unit
(Removing the staples that are stuck)
1. Following the steps in
3-4 Replacing the Staple Level Sensor
, remove the sensor.
2. Remove the four hexagonal hole screws.
3. After disassembly, remove all the staples.
4. After the removal, take the reverse steps to reassemble the product.
When inserting the connector into the sensor, be careful not to bend the pin.
Refer to
3.6 Adjusting the Stapler Unit Head
.
List of Components
No.
Name
Qty.
01-001
Stapler Unit
1
221
Base Block
1
226
Plate
1
HS3x6
Inner Hexagonal Hole Screw
4
4-HS3x6
226
[Plate]
4-HS3x6
221 [Base Block]