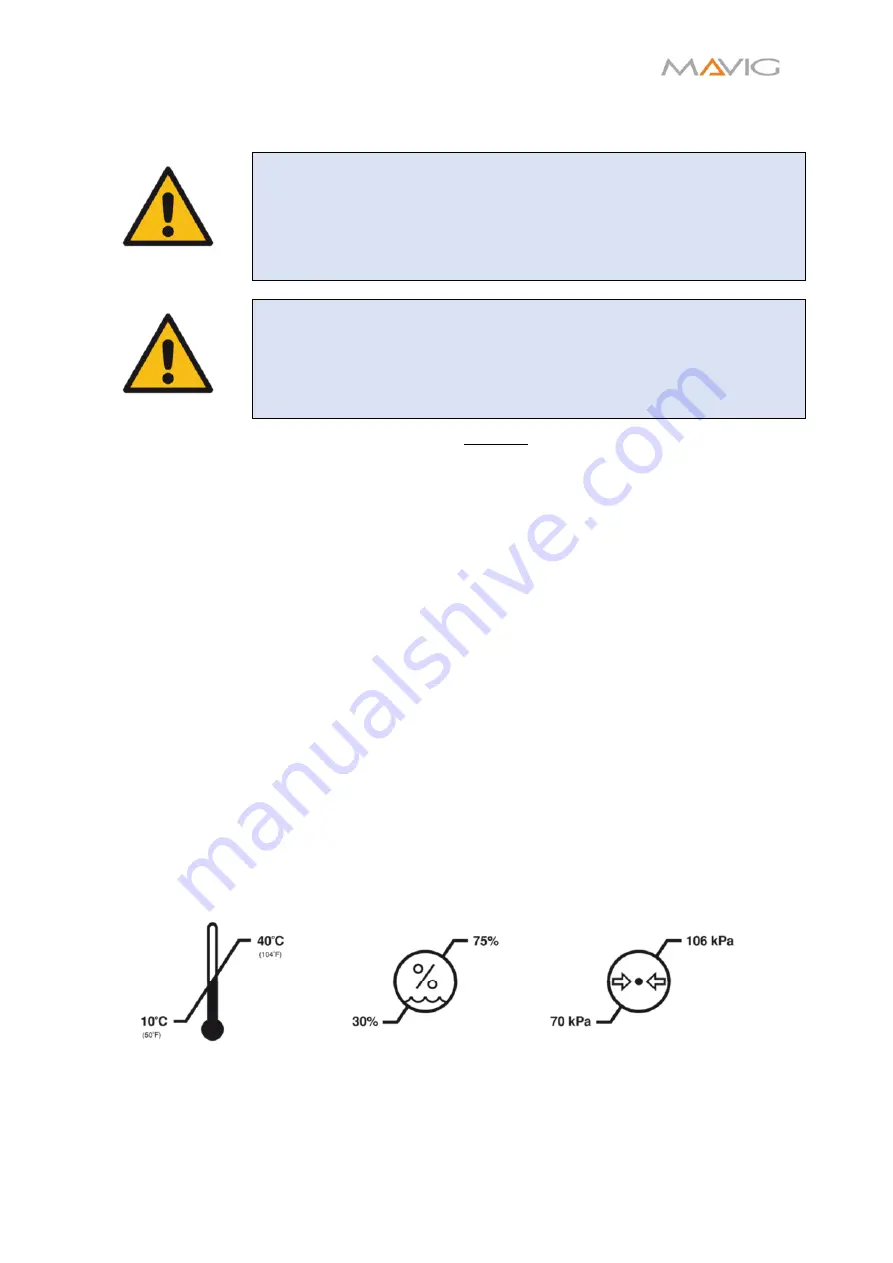
Page 9 of 54
5100054
BND01O03.docx
Avoid collisions between the system and other devices, walls, ceilings, etc. as these may
cause serious damage to the system.
WARNING – Risk of injury!
The manufacturer must be immediately informed of any damage to the
system. Stop all use of the device until the damage is rectified:
Disconnect the system from the mains. Do not stand or work beneath
the system.
WARNING – Risk of injury!
Do not remove any covers, or open any cable ducts, etc.!
Failure to comply in full with these instructions exempts the manufacturer from all liability
and/or warranty obligations.
Additional installation considerations according IEC 60601-1:2005+AMD1:2012:
When installed in an end-product, consideration must be given to the following:
•
Humidity preconditioning treatment shall be considered during end-product
evaluation (clause 5.7)
•
The power input measurements must be conducted during the end-product
evaluation with all loads supplied and operated in the least favorable condition.
•
Applicable leakage current tests shall be conducted during the end-product
evaluation.
•
In the end-product installation, the equipment must have means to isolate its
circuits electrically from the supply mains on all poles simultaneously.
•
In the end-product installation, the equipment shall be fused acc. to clause 8.11.5
•
The end-product installation has to be conform to the EMV specifications acc. to
clause 17.
5.
Transport, Storage and Operational Conditions
5.1.
When in Operation
•
Temperature:
10 °C to 40 °C
•
Relative humidity:
30% to 75%
•
Air pressure:
70 kPa to 106 kPa