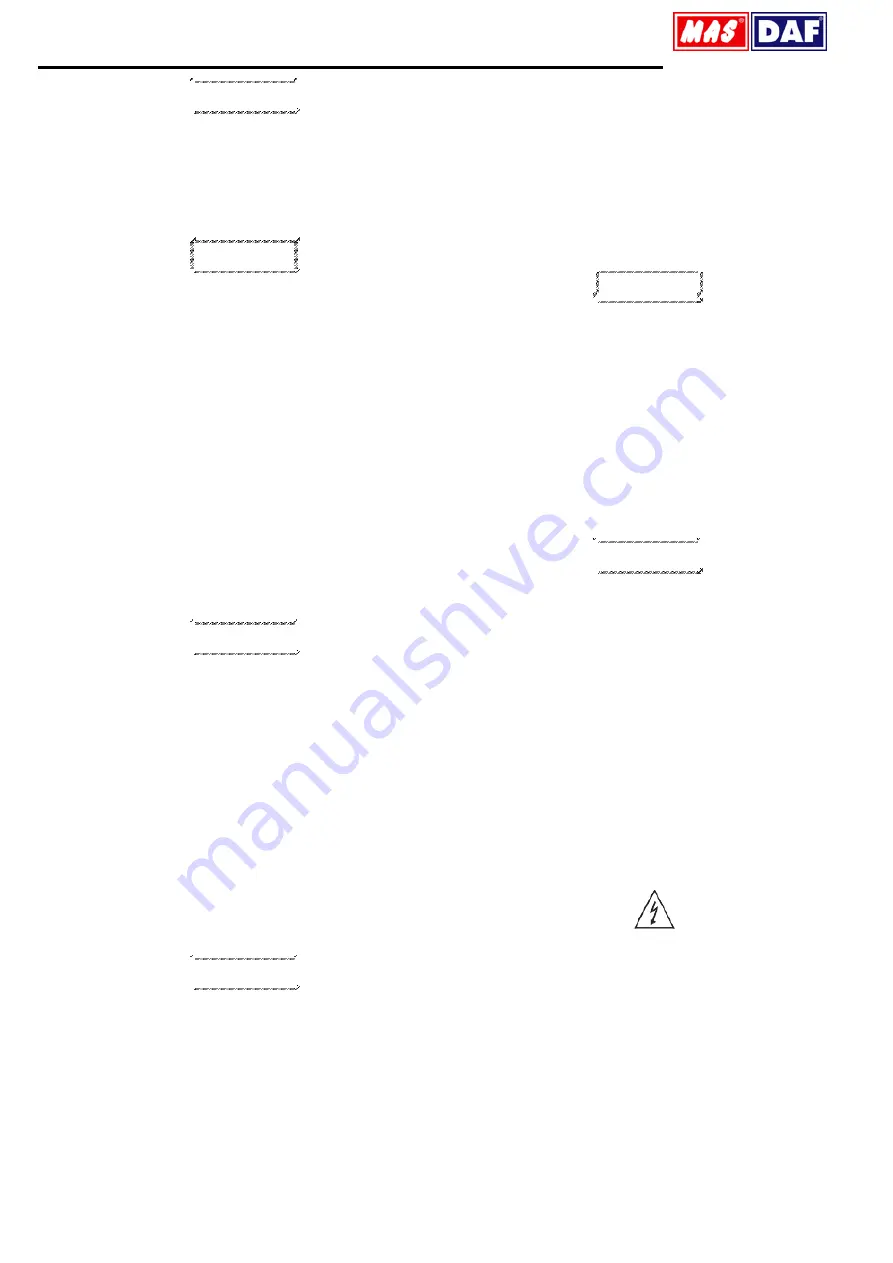
Mas Grup
7
CAUTION
Some leakage from 3.8 to 19 l/min will occur when the valve is fully
closed. Be sure the bypass line is directed back to the wet well or tank to
prevent hazardous spills.
When the pump shuts down, the spring returns the diaphragm to its
original position. Any solids that may have accumulated in the diaphragm
chamber settle to the bottom and are flushed out during the next priming
cycle.
CAUTION
The valve will remain open if the pump does not reach its designed
capacity or head. Valve closing pressure is dependent upon the
discharge head of the pump at full capacity. The range of the valve
closing pressure is established by the tension rate of the spring.
Valve closing pressure can be further adjusted to the exact system
requirements by moving the spring retaining pin up or down the
plunger rod to increase or decrease tension on the spring.
6.5.3.1. Automatic Air Release Valve Installation
The automatic air release valve must be independently mounted in a
horizontal position and connected to the discharge line of the self-priming
centrifugal pump.
The valve inlet must be installed between the pump discharge port and
the non-pressurized side of the discharge check valve. The valve inlet is
at the large end of the valve body and it is provided with standard 1-inch
pipe thread.
The valve outlet is located at the opposite end of the valve and is also
equipped with standard 1-inch pipe threads. The outlet should be
connected to a bleed line which slopes back to the wet well or sump. The
bleed line must be the same size as the inlet piping or larger. If piping is
used for bleed line, avoid o use of elbows whenever possible.
CAUTION
It is recommended that each air release valve should be fitted with
an independent bleeder line directed back to the wet well. However,
if multiple air release valves are installed in a system, the bleeder
lines may be directed to a common manifold pipe.
6.5.4. Discharge Lines
6.5.4.1. Siphoning
Do not terminate the discharge line at a level lower than of the liquid
being pumped unless a siphon breaker is used in the line. Otherwise, a
siphoning suction causing damage to the pump could result.
6.5.4.2. Valves
If a throttling is desired in the discharge line, use a valve as large as the
largest pipe to minimize friction losses. Never
install a throttling valve and
system check valve be installed in the discharge line to protect the pump
from excessive shock pressure and reverse rotation when it is stopped.
CAUTION
If the application involves a high discharge head, gradually close the
discharge throttling valve before stopping the pump.
6.5.4.3. By-pass Lines
Self-priming pumps are not air compressors. During the priming cycle, air
from the suction line must be vented to atmosphere on the discharge
side. If the discharge line is open, this air check valve has been installed
in the discharge line; the discharge side of the pump must be open to the
atmospheric pressure through a by-pass line installed between the pump
discharge and the check valve. A self-priming centrifugal pump will not
prime if there is sufficient static liquid head to hold the discharge check
valve closed.
Note: The by-pass line should be sized so that it does not affect pump
discharge capacity; however the by-pass line
should be at least 1” in
diameter to minimize the chance of plugging.
Inflow discharge applications (less than 30 feet or 9 meters), it is
recommended that the by-pass line be run back to the wet well and locate
6” below the water level or cut-off point of the level pump. In some
installation, this by-pass line may be terminated with 180-240 cm in length
1 1/2" hoses. Smoothbore hose, air and liquid vented during the priming
process will then agitate the hose and break up any solids, grease, or
other substances likely to cause clogging.
CAUTION
A by-pass line that is returned to a wet well must be secured against
being drawn into the pump suction inlet.
It is also recommended that pipe unions be installed at each
90˚ elbow in
a by-pass line to ease disassembly and maintenance.
In high discharge head applications (more than 30 feet or 9 m), an
excessive amount of liquid may be by-passed and forced back to the wet
well under the full working pressure of the pump.
If the installation involves a flooded suction such as below - ground lift
station. A pipe union and manual shut
– off valve may be installed in the
bleed line to allow service of the valve is installed anywhere in the air
release piping, it must be a full
– opening ball type valve to prevent
plugging by solids.
CAUTION
If a manual shut-off valve is installed in a by-pass line, it must not be
left closed during operation. A closed manual shut-off valve may
cause a pump which has lost prime to continue to operate without
reaching prime, causing dangerous overheating and possible
explosive rupture of the pump casing. Personnel could be severely
injured. Allow an over-heated pump to cool before servicing. Do not
remove plates, covers, gauges, or fittings from an overheated pump.
Liquid within the pump can reach boiling temperatures, and vapor
pressure within the pump can cause parts being disengaged to be
ejected with great force. After the pump cools, drain the liquid from
the pump by removing the casing drain plug. Use caution when
removing the casing drain plug. Use caution when removing the
plug to prevent injury to personnel from hot liquid.
6.6. Motor Connection for Applications with Electric Motor
In electric motor coupled UKM-S type pumps, motor must be connected
by an electrical technician according to the connection (switch) diagram.
Local electricity policies have to be applied.
•
Electrical connections have to be made by authorized electricians.
•
In dismantling the pump, make sure the electricity is cut off before
taking the motor cover out.
•
Use the appropriate electrical connection to the motor.
In environments where there is a risk of explosion, prescribed
protective law and regulations shall be applied by competent
authorities.