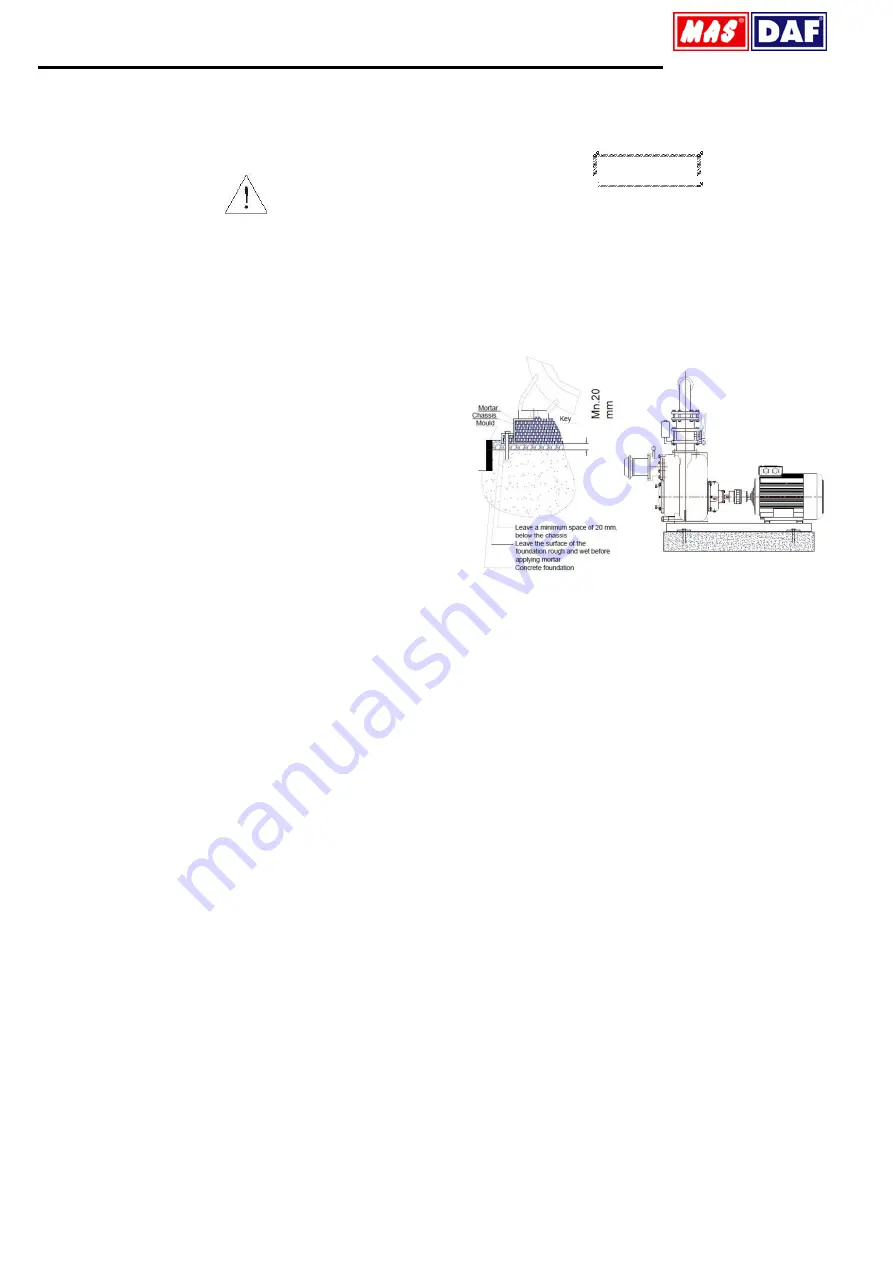
Mas Grup
4
Damages caused in transport
Check the pump when it is delivered to you. Please let us know of there is
any damage.
5.2. Storage
Please keep the unit clean and dry area during storage.
If the pump is out of use for a long time, please consider the instructions
below.
1. If there is water inside the pump, drain it.
2. Clean the pump casing and impeller by jetting clean water for a short
time.
3. Empty water inside the pump casing, suction line and discharge line.
4. Add small amount of antifreeze inside the pump casing if it is not
possible to empty it completely. Rotate the pump shaft by hand to mix
the antifreeze.
5. Add liquid lubricator into the bearing and seal gap up
until the level
indicator.
6. Close the suction and discharge exits with gasket.
7. Spray an anti-corrosive into the pump casing.
8. Rotate the pump shaft by hand once in every month, in order to protect
it from freezing and to lubricate the bearings.
6. ASSEMBLY / INSTALLATION
6.1. Installation
In our standard production, the pump and the motor have been installed
in a common base plate.
6.1.1. Location of Installation
Pump will be installed in a location where the control and the
maintenance of the pump are easily made. The pump room should be
suitable for operation of lifting systems such as freight elevator, forklift,
etc.
6.1.2. Location of Installation- Local Ambient Temperature
When the local ambient room temperature exceeds +40
o
C in a pumping
system, suitable ventilation should be provided in order to remove the
heat dissipated to the environment and supply fresh air.
6.2. Type of Connection
Type of connection depends on the design type and the size of the pump
and the motor, as well as the local installation conditions. Foot-mounted
horizontal pump-motor units have been installed in a common base plate.
6.3. Foundation
6.3.1. General
In applications where a trailor is not used, the pump must be properly
fixed to solidified concrete base plate with studs.
Base plate of the pump must be grouted. The foundation shall be of
concrete or steel framework.
Note:
The foundation shall distribute the weight of the pumping group
evenly.
6.3.2. Main Properties of the Steel Framework Bases
Foundations with steel framework shall be designed in such a way that
the base plate is bolted or welded contacting to all area.
CAUTION
If base plate is supported from only four points, pump group will
stay in the middle, causing misalignment of the coupling and
increasing the noise level.
6.3.3. Foundation Properties
The foundation shall be horizontal, flat and clean and shall support all the
weight.
Note:
Reinforced concrete bases are constructed from standard concrete
with at least B 25 resistance class.
Figure 3:
Typical Concrete Foundations
6.4. Coupling Alignment
6.4.1. General
For a proper operation of a pump group, a good alignment of the coupling
is necessary. Vibration, noise, overheating of the bearings, overcharge
problems can be attributed to the misalignment of coupling or using an
improper coupling.
Flexible coupling does not correct the axial misalignments between
the pump and the motor axes. However, it allows pinpointing the
misalignments.
In order to avoid overheating, vibration, noise and wearing of the
rolling bearings, alignment of the coupling has to be made properly
and checked often.
Do not use a different coupling other than the original type installed
on pumping group.
6.4.2. Method of Coupling Alignment
When the motor moves towards the pump, a gap must be maintained in
order that the two faces of the coupling do not touch each other. The
recommended distance is 3 mm. To check the coupling alignment, a
conical measurement device and a gauge stick are needed.
1. Angular Misalignment (Figure 4)
In order to control the angular misalignment, the distance between the
two halves of the coupling is measured in both horizontal and vertical
planes. Measurements taken at four points shall be in agreement for the
alignment.
2. Parallel Axis Misalignment (Figure 4)
In order to control parallel axis misalignment, a smooth edged
gauge stick is pressed axially over the upper half of the coupling. Then,
the gauge stick is checked for the other half of the coupling. For
alignment, the gauge stick shall be in contact with both of the halves at
the same time. This procedure shall be repeated for four sides of the
coupling. (i.e. top, bottom, left and right sides of the coupling). When all
four sides give reasonably accepted results, alignment of the coupling
has been ensured.