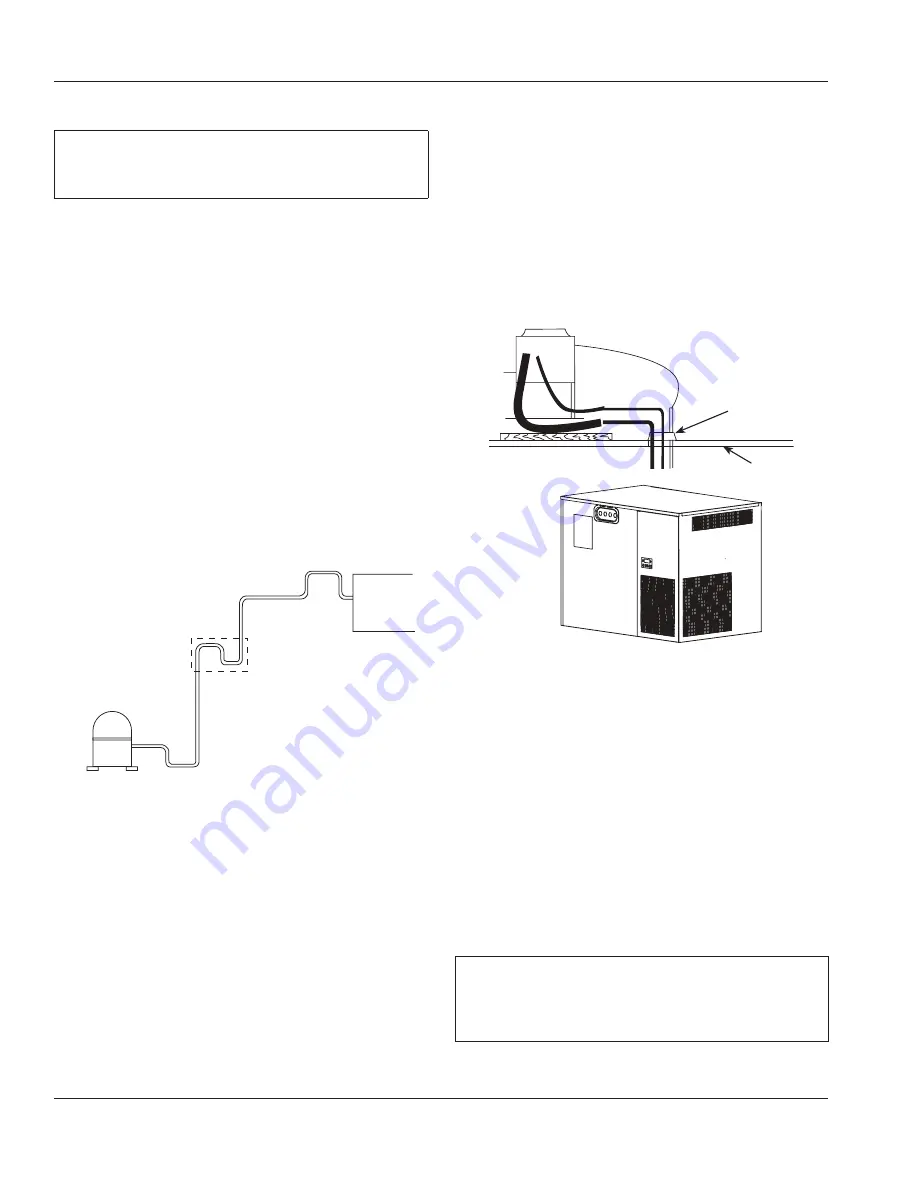
28
Part Number 020002365 08/25/2015
Installation
Section 2
PRE-CHARGED REFRIGERATION LINE REQUIREMENTS
Important
If you have a MAC Multi-Pass condenser, please add
three (3) pounds additional charge.
1. Both the discharge and liquid remote condensing lines
must be kept to a minimum distance for maximum
performance. All Multiplex systems are capacity
rated to 100 ft (30.5 m) tubing distance between
the compressor and condenser. If you have another
brand condenser, please add additional charge for the
condenser (example: up to three (3) pounds for a MAC
condenser).
2. Any vertical rise 25 ft (7.6 m) or greater must have a
manufactured or installed trap (bend), in the discharge
refrigeration line from the compressor to the remote
condenser. A trap is necessary for every additional 25 ft
(7.6 m) vertical rise. When excessive vertical rise exists,
this trap allows oil to reach the condenser and return to
the compressor.
3. The easiest method to create a trap is to bend the
tubing (smoothly, no kinks) into the trap form.
Discharge Line
Condenser Trap
To the
Condenser
Discharge Line Trap Every
25 Vertical ft. (7.6 m)
3" (7.6 cm) x 6" (15.2 cm)
Maximum Trap Area
3 ft (0.9 m) (minimum) of Discharge
Line Trap at the Compressor
Compressor
4. The trap(s) must be of minimum height of 3" (7.6
cm) and a width of 6" (15.2 cm) to minimize oil
accumulation. The traps can also be bent out of the
refrigeration tubing. Carefully bend the tubing down
12" (30.5 cm), and then sweep the tubing back up.
5. It is critical that the Multiplex remote condensing line
size specifications for the specific model be maintained.
The specifications are 1/2" discharge and 3/8" liquid
lines.
Installing the Multiplex Remote Condenser
The Multiplex remote condensing units have a 208-230 Volt,
50/60 HZ, 1 PH fan motor that includes a permanent split
capacitor and internal overload protection. The electrical
wires from the refrigeration unit wire to the condenser.
The electrical installation must be in accordance with local
codes, National Electrical Code and regulations.
1. Determine a position for installation that will allow
access for maintenance and is free from obstruction.
Verify hot air discharge from other condensers does not
interfere with the inlet of this condenser.
2. Install the four legs to the sides of the condenser using
the mounting bolts provided.
3. The General Contractor or Owner must secure two
treated lumber 4" x 4" x 36" (or longer). You may then
mount the remote condenser to the treated lumber.
4. The General Contractor or Owner must install a 3" pitch
pot in the roof. Then seal for weather protection.
Roof
3" Pitch Pot
5. Locate the pre-charged refrigeration lines shipped with
the system. These lines must be a correct length for the
building design. Avoiding any kinks, neatly route these
lines from the remote condenser to the refrigeration
unit. Excess refrigeration tubing must be handled in
one of two ways. When coiling the excess tubing, make
sure the inlet to the coil is at the top of the coil and the
exit is the bottom of the coil. There can be no more
than one turn to the coil. If you have more tubing, you
must cut out the excess before connecting the ends.
When cutting the tubing, you must first evacuate the
refrigerant (line sets have a positive refrigerant holding
charge of two to three ounces). After shortening and
welding the tubing together again, you must evacuate
the tubing to 250 microns. Then recharge the tubing
with 4 ounces of appropriate refrigerant.
,
Caution
Excess refrigeration tubing must be properly cared for
before being connected to either the remote condenser
or the refrigeration unit.
Содержание Multiplex 42 MR04
Страница 8: ...8 Part Number 020002365 08 25 2015 General Information Section 1 THIS PAGE INTENTIONALLY LEFT BLANK ...
Страница 44: ...44 Part Number 020002365 08 25 2015 Maintenance Section 4 THIS PAGE INTENTIONALLY LEFT BLANK ...
Страница 50: ...50 Part Number 020002365 08 25 2015 Troubleshooting Section 5 THIS PAGE INTENTIONALLY LEFT BLANK ...
Страница 51: ...Part Number 020002365 08 25 2015 51 Section 5 Troubleshooting THIS PAGE INTENTIONALLY LEFT BLANK ...