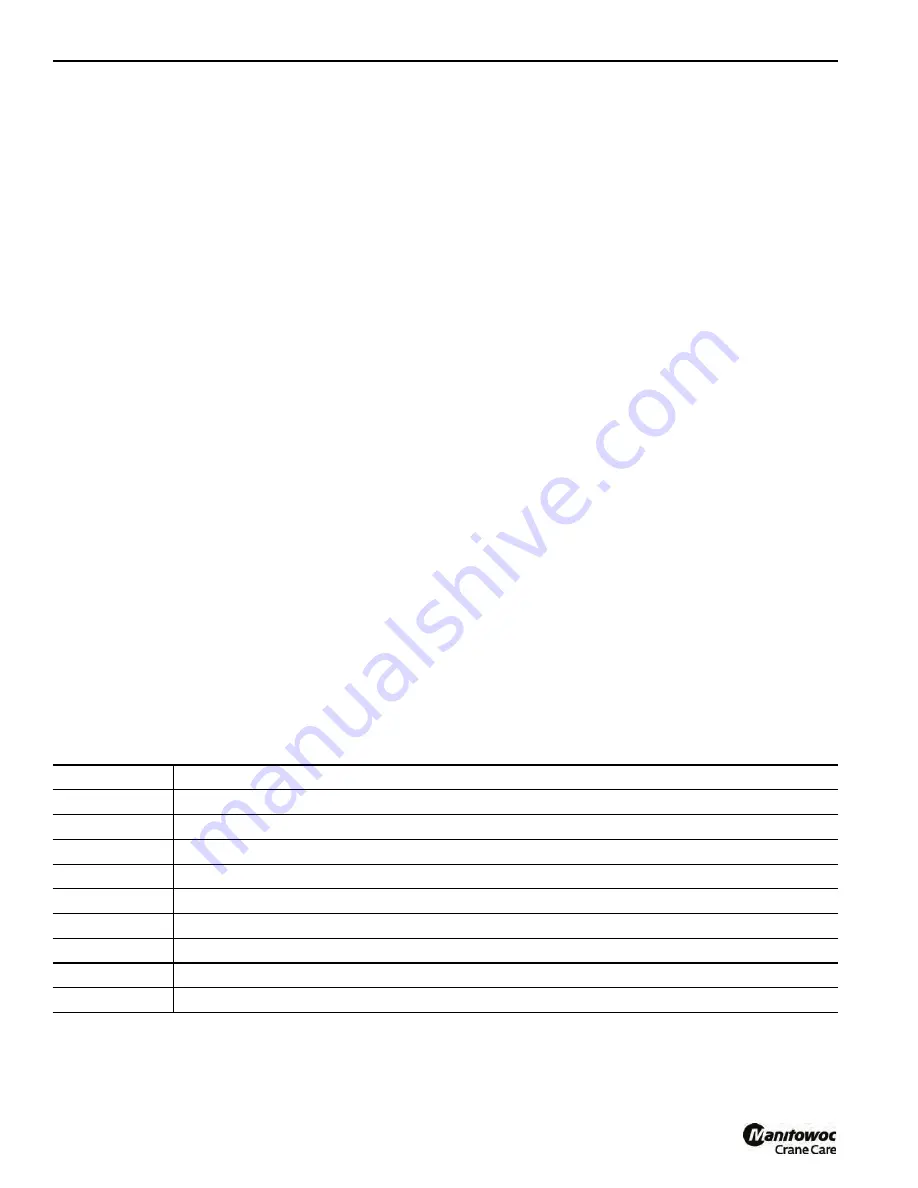
LUBRICATION
TMS800E13 OPERATOR MANUAL
4
Published 02-06-2014, Control # 495-00
LUBRICATION POINTS
A regular frequency of lubrication must be established for all
lubrication points. Normally, this is based on component
operating time. The most efficient method of keeping track of
lube requirements is to maintain a job log indicating crane
usage. The log must use the engine hourmeter to ensure
coverage of lube points that will receive attention based on
their readings. Other lubrication requirements must be made
on a time basis, that is, weekly, monthly, etc.
All oil levels are to be checked with the crane parked on a
level surface in transport position, and while the oil is cold,
unless otherwise specified.
On plug type check points, the oil levels are to be at the
bottom edge of the check port.
On all hoists with a check plug in the drum, the check/fill plug
shall be at the 3 o’clock position with the oil level at the
bottom edge of the check port.
All grease fittings are SAE STANDARD unless otherwise
indicated. Grease non-sealed fittings until grease is seen
extruding from the fitting. 0.28 kg (1 oz) of EP-MPG equals
one pump on a standard 0.45 kg (1 lb) grease gun.
Over lubrication on non-sealed fittings will not harm the
fittings or components, but under lubrication will definitely
lead to a shorter lifetime.
On sealed U-joints, care must be exercised to prevent
rupturing seals. Fill only until expansion of the seals first
becomes visible.
Unless otherwise indicated, items not equipped with grease
fittings, such as linkages, pins, levers, etc., should be
lubricated with oil once a week. Motor oil, applied sparingly,
will provide the necessary lubrication and help prevent the
formation of rust. An anti-seize compound may be used if
rust has not formed, otherwise the component must be
cleaned first.
Grease fittings that are worn and will not hold the grease
gun, or those that have a stuck check ball, must be replaced.
Where wear pads are used, cycle the components and
relubricate to ensure complete lubrication of the entire wear
area.
Surface Protection for Cylinder Rods
Steel cylinder rods include a thin layer of chrome plating on
their surfaces to protect them from corroding. However,
chrome plating inherently has cracks in its structure which
can allow moisture to corrode the underlying steel. At typical
ambient temperatures, hydraulic oil is too thick to penetrate
these cracks. Normal machine operating temperatures will
allow hydraulic oil to warm sufficiently to penetrate these
cracks and if machines are operated daily, protect the rods.
Machines that are stored, transported, or used in a corrosive
environment (high moisture, rain, snow, or coastline
conditions) need to have the exposed rods protected more
frequently by applying a protectant. Unless the machine is
operated daily, exposed rod surfaces will corrode. Some
cylinders will have rods exposed even when completely
retracted. Assume all cylinders have exposed rods, as
corrosion on the end of the rod can ruin the cylinder.
It is recommended that all exposed cylinder rods be
protected using Boeshield® T-9 Premium Metal Protectant.
Manitowoc Crane Care has Boeshield® T-9 Premium Metal
Protectant available in 12 oz. cans that can be ordered
through the Parts Department.
NOTE:
Cylinder operation and inclement weather will
remove the Boeshield® protectant; therefore,
inspect machines once a week and reapply
Boeshield® to unprotected rods.
Table 5-1
Lube Symbol Chart
Symbol
Description
AFC
Antifreeze/Coolant - 50/50 Blended, Fully Formulated - SAE Grade J1941
EO
Engine Oil - SAE 15W-40, API Service Classification CJ-4.
EP-MPG
Extreme Pressure Multipurpose Grease - Lithium Soap Base, NLGI Grade 2.
SGL-5
Synthetic Gear Lubricant - SAE Grade 50, API Gravity 23.
HYDO
Hydraulic Oil - Must meet John Deere Standard JDM-J20C, Allison C4, and ISO 4406 level.
SSGL-5
Semi-Synthetic Gear Lubricant - SAE Grade 80W-90, API Service Designation GL-5.
ASC
Anti-Seize Compound - Military Specifications MIL-A-907E.
EP-OGL
Open Gear Lubricant - Fuchs Ceplattyn 300 Spray, NLGI Class 1-2
AGMA No. 4 EP
Extreme Pressure Gear Lube
Reference Only
Содержание Grove TMS800E13
Страница 5: ...Operator Manual Grove TMS800E13 R e f e r e n c e O n l y ...
Страница 6: ...R e f e r e n c e O n l y ...
Страница 148: ...SET UP AND INSTALLATION TMS800E13 OPERATOR MANUAL 38 Published 02 06 2014 Control 495 00 R e f e r e n c e O n l y ...
Страница 162: ...LUBRICATION TMS800E13 OPERATOR MANUAL 14 Published 02 06 2014 Control 495 00 THIS PAGE BLANK R e f e r e n c e O n l y ...
Страница 166: ...OPERATOR MANUAL TMS800E13 APL 2 R e f e r e n c e O n l y ...
Страница 167: ...R e f e r e n c e O n l y ...
Страница 168: ...R e f e r e n c e O n l y ...