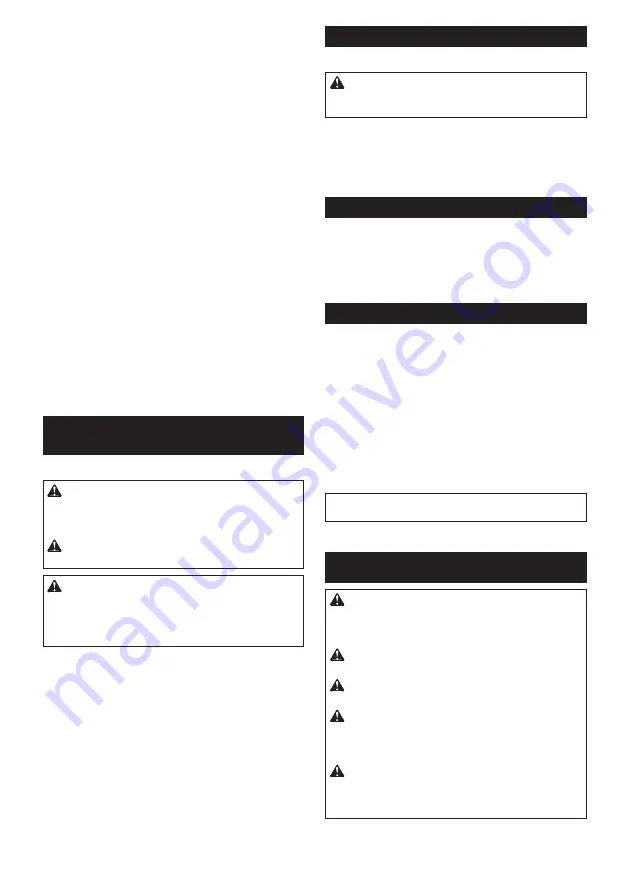
10 ENGLISH
For tool with locking screw type
wheel guard
Mount the wheel guard with the protrusions on the
wheel guard band aligned with the notches on the bear
-
ing box. Then rotate the wheel guard to such an angle
that it can protect the operator according to work. Be
sure to tighten the screw securely.
To remove wheel guard, follow the installation proce
-
dure in reverse.
►
Fig.5:
1.
Wheel guard
2.
Bearing box
3.
Screw
For tool with clamp lever type wheel
guard
Loosen the screw, and then pull the lever in the direc
-
tion of the arrow. Mount the wheel guard with the protru
-
sions on the wheel guard band aligned with the notches
on the bearing box. Then rotate the wheel guard to such
an angle that it can protect the operator according to
work.
►
Fig.6:
1.
Wheel guard
2.
Bearing box
3.
Screw
4.
Lever
Pull the lever in direction of the arrow. Then tighten the
wheel guard with fastening the screw. Be sure to tighten
the screw securely. The setting angle of the wheel
guard can be adjusted with the lever.
►
Fig.7:
1.
Screw
2.
Lever
To remove wheel guard, follow the installation proce
-
dure in reverse.
Installing or removing depressed
center wheel or flap disc
Optional accessory
WARNING:
When using a depressed center
wheel or flap disc, the wheel guard must be fitted
on the tool so that the closed side of the guard
always points toward the operator.
WARNING:
Never use a grinding wheel which
is more than 6.5 mm thick.
CAUTION:
Make sure that the mounting part
of the inner flange fits into the inner diameter of
the depressed center wheel / flap disc perfectly.
Mounting the inner flange on the wrong side may
result in the dangerous vibration.
Mount the inner flange onto the spindle.
Make sure to fit the dented part of the inner flange onto
the straight part at the bottom of the spindle.
Fit the wheel/ disc on the inner flange and screw the
lock nut with its protrusion facing downward (facing
towards the wheel).
►
Fig.8:
1.
Lock nut
2.
Depressed center wheel
3.
Inner flange
4.
Mounting part
To tighten the lock nut, press the shaft lock firmly so
that the spindle cannot revolve, then use the lock nut
wrench and securely tighten clockwise.
►
Fig.9:
1.
Lock nut wrench
2.
Shaft lock
To remove the wheel, follow the installation procedure
in reverse.
Installing or removing flex wheel
Optional accessory
WARNING:
Always use supplied guard when
flex wheel is on tool.
Wheel can shatter during use
and guard helps to reduce chances of personal injury.
►
Fig.10:
1.
Lock nut
2.
Flex wheel
3.
Back up pad
4.
Inner flange
Follow instructions for depressed center wheel but also
use back up pad over wheel. See order of assembly on
accessories page in this manual.
Super flange
Optional accessory
Only for tools with M14 spindle thread.
Models with the letter F are standard-equipped with
Super flange. Only 1/3 of efforts needed to undo lock
nut, compared with conventional type.
Installing or removing abrasive disc
Optional accessory
►
Fig.11:
1.
Sanding lock nut
2.
Abrasive disc
3.
Rubber pad
1.
Mount the rubber pad onto the spindle.
2.
Fit the disc on the rubber pad and screw the sand
-
ing lock nut onto the spindle.
3.
Hold the spindle with the shaft lock, and securely
tighten the sanding lock nut clockwise with the lock nut
wrench.
To remove the disc, follow the installation procedure in
reverse.
NOTE:
Use sander accessories specified in this man
-
ual. These must be purchased separately.
OPERATION
WARNING:
It should never be necessary to
force the tool.
The weight of the tool applies ade
-
quate pressure. Forcing and excessive pressure
could cause dangerous wheel breakage.
WARNING:
ALWAYS replace wheel if tool is
dropped while grinding.
WARNING:
NEVER bang or hit grinding disc
or wheel onto work.
WARNING:
Avoid bouncing and snagging
the wheel, especially when working corners,
sharp edges etc.
This can cause loss of control and
kickback.
WARNING:
NEVER use tool with wood cutting
blades and other saw blades.
Such blades when
used on a grinder frequently kick and cause loss of
control leading to personal injury.