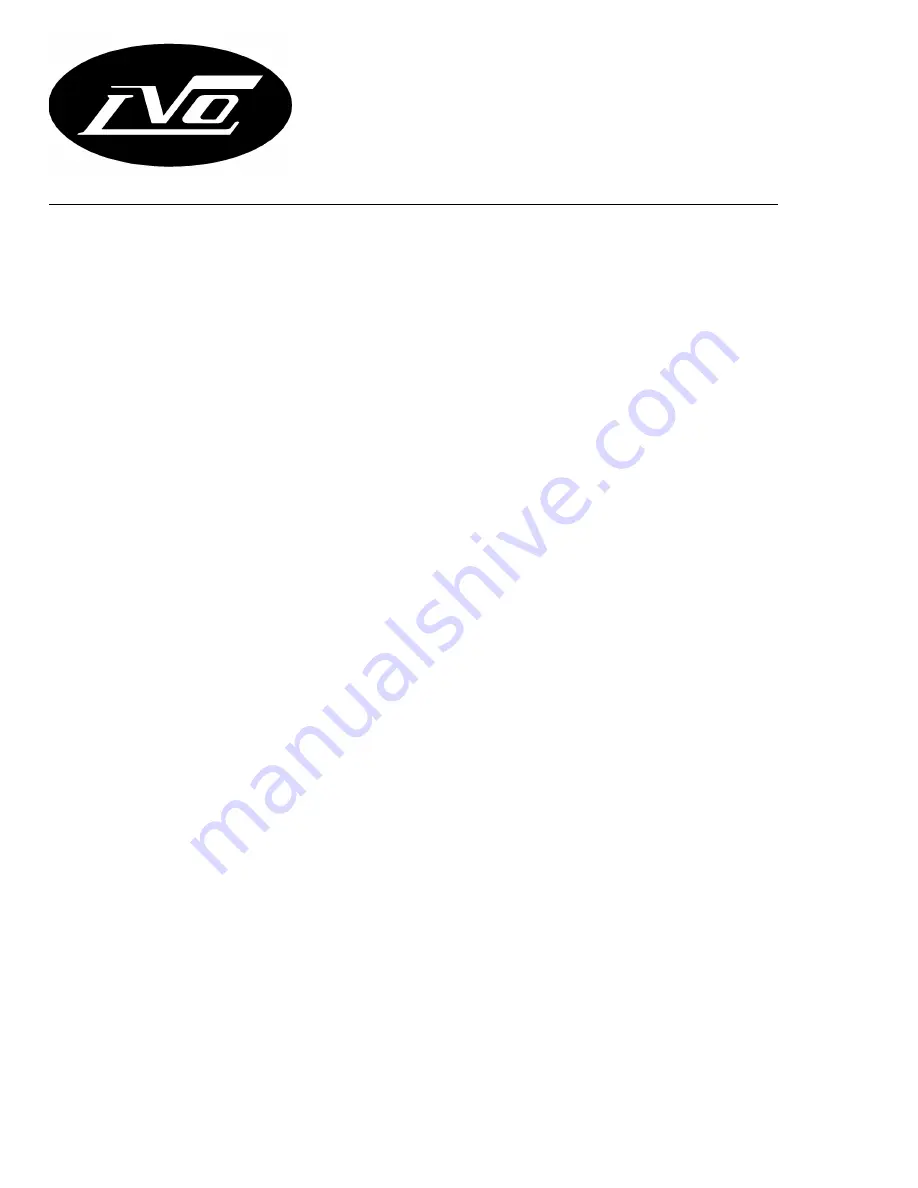
LVO Manufacturing Inc.
LVO Manufacturing Inc.
LVO Manufacturing Inc.
LVO Manufacturing Inc.
808 N. 2
nd
Avenue E., P.O. Box 188
Rock Rapids, IA 51246
www.lvomfg.com
(712) 472-3734
1-800-346-5749 Fax (712) 472-2203
__________________________________________________________________________________________________________________________________________________________________
8
There are many methods for setting the machine in the pit. Often the machine is slid into the
pit from the front. Hydraulic jacks, pry bars and pallet jacks or a forklift are usually necessary
to accomplish the task. Keep in mind that the heaviest part of the machine is the backside
where the pumps are located.
Once the machine is in the pit, the front floor grate should be set in place. The machine
should then be moved ahead to eliminate any gaps between the machine and the floor grate
yet leaving enough a space that the floor grate can be removed for periodic hosing down of
the pit floor.
Step 4 DRAIN:
Provisions for the drain should be made next. The rack washer has a copper drain
located as shown on pages 24 - 26 of this manual (see page 3 for drain size). The drain
should be plumbed according to local code. Local ordinance may require a grease trap, vent,
and/or a floor sink. If required these should be installed before the machine is installed. It is
strongly recommended that unions be used to allow the machine to be easily moved. Failure
to do so may void the warranty.
Models that set in a pit do not require a drain connection because the wash tank drains
directly into the pit.
Step 5 WATER SUPPLY HOOK-UP:
The factory recommends 140° F (120° F minimum) hot
water at the machine (see page 3 for water line size). This may require a dedicated water
heater for the rack washer. If hard water is present the manufacturer recommends installing a
water softener or calcium filter. Hard water deposits will shorten the life of many of the
components on the rack washer, resulting in higher maintenance costs. Please note that a
union is installed at the point of hook-up (see pages 24 - 26). This will allow the machine to
be moved for service and cleaning. The customer must furnish a shut-off valve on the supply
side of the union. This shut-off should be easily accessible to the operator of the machine.
Step 6 STEAM VENT:
The machine is equipped with a collar for 8" duct work as shown on pages
24 - 26. This duct should be directly vented to the outside of the building. DO NOT vent
into a wall, attic, or any other concealed space of the building and avoid horizontal runs of
duct.
The factory recommends 8" plastic pipe or stainless steel duct for the vent. If stainless steel is
used the duct work should be installed with reverse joints so that the condensate inside the
vent can drain back into the machine without leaking. All seams should also be sealed with
silicon.
Generally the machine is ordered with a 700 cfm, 1/2 Hp squirrel cage fan. The 700 cfm fan
and adapter (provided) should be mounted and siliconed directly to a flange on the top of the
machine before the duct work is installed. The ductwork attaches directly to the exhaust of the
fan. Wire is provided to wire the fan directly into the control panel. A dedicated breaker and