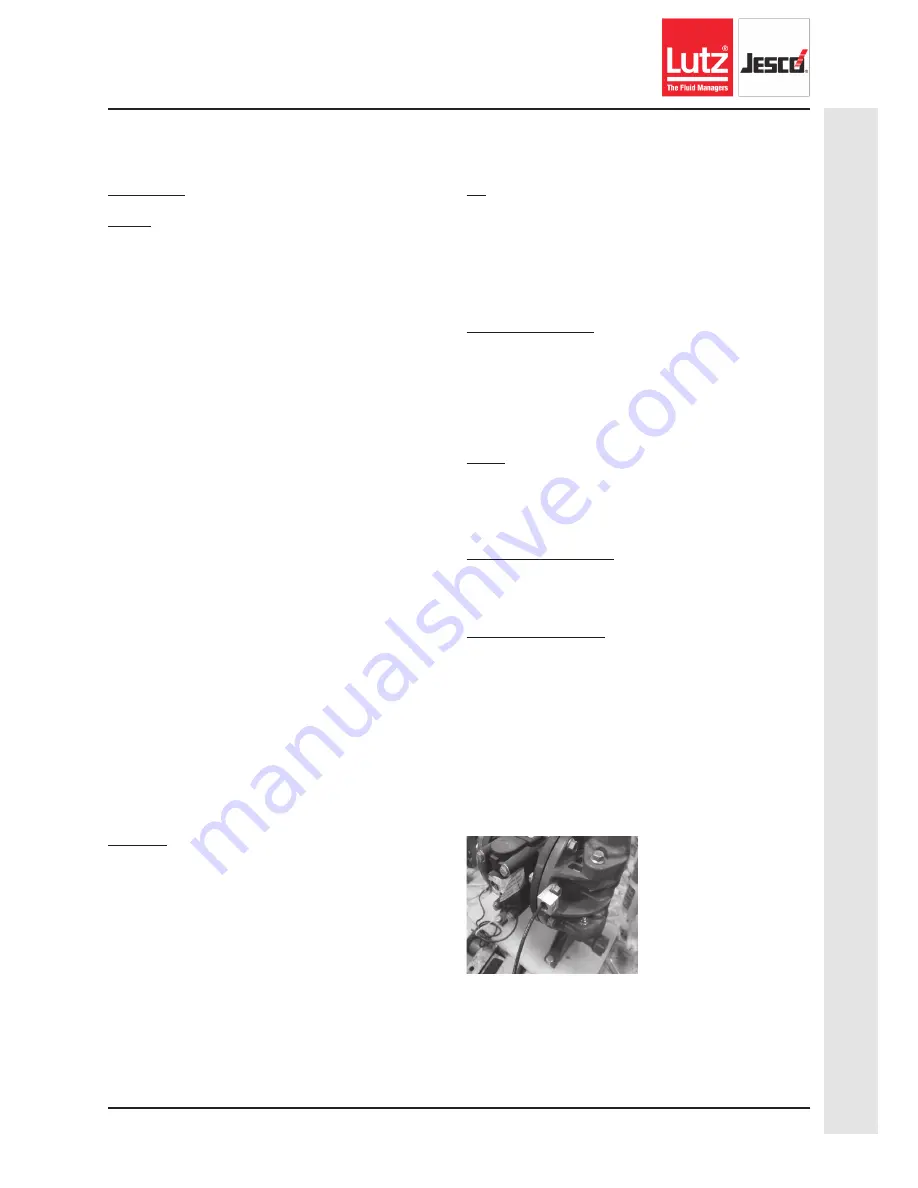
Installation, Troubleshooting and Maintenance
Installation
Piping
Whenever possible ensure the pump is installed using the
shortest possible pipe lengths with the minimum amount of
pipe fittings. Ensure all piping is supported independent of
the pump.
Suction and discharge piping should not be smaller than the
connection size of the pump. When pumping liquids of high
viscosity, larger piping may be used, in order to reduce fric-
tional pipe loss.
Employ flexible hoses in order to eliminate the vibration
caused by the pump. Mounting feet can also be used to re-
duce vibration effects.
All hoses should be reinforced, non-collapsible and be capa-
ble of high vacuum service. Ensure that all piping and hoses
are chemically compatible with the process and cleaning
fluid.
For processes where pulsation effects should be
reduced, employ a pulsation dampener on the discharge side
of the pump.
For self-priming applications, ensure all connections are air-
tight and the application is within the pumps dry-lift capabil-
ity. Refer to product specifications for further details.
For flooded suction applications, install a gate valve on the
suction piping in order to facilitate service.
For unattended flooded suction operation, it is recommended
to pipe the exhaust air above the liquid source. In the event
of a diaphragm failure this will reduce or eliminate the pos-
sibility of liquid discharging through the exhaust onto the
ground.
Location
Ensure that the pump is installed in an accessible location, in
order to facilitate future service and maintenance.
Air
Ensure that the air supply is sufficient for the
volume of air required by the pump. Refer to product specifi
-
cations for further details. For reliable operation, install a 5
micron air filter, air-valve and pressure regulator. Do not ex
-
ceed the pumps maximum operating pressure of 120 psig.
Remote Operation
Utilize a three way solenoid valve for remote operation. This
ensures that air between the solenoid and the pump is al-
lowed to “bleed off,” ensuring reliable operation. Liquid
transfer volume is estimated by multiplying displacement per
stroke times the number of strokes per minute.
Noise
Correct installation of the muffler reduces sound
levels. Refer to product specifications for
further details.
Submerged Operation
For submersible operation, pipe the air exhaust to atmo-
sphere
Grounding the Pump
Loosen grounding screw and install a grounding wire. Tighten
grounding screw. Wire size should be a 12 gauge wire or larg-
er. Connect the other end of the wire to a true earth ground.
Equipment must be grounded to achieve ATEX rating and it
is recommended to configure the pump with a grounding lug
option.
P h o n e : ( 5 8 5 ) 4 2 6 - 0 9 9 0
www.lutzjescoamerica.com
Fax: (585) 426-4025
9
Operation & Maint
enance Ins
tructions
AODD: 2” Air Operat
ed Double Diaphragm Pum
p