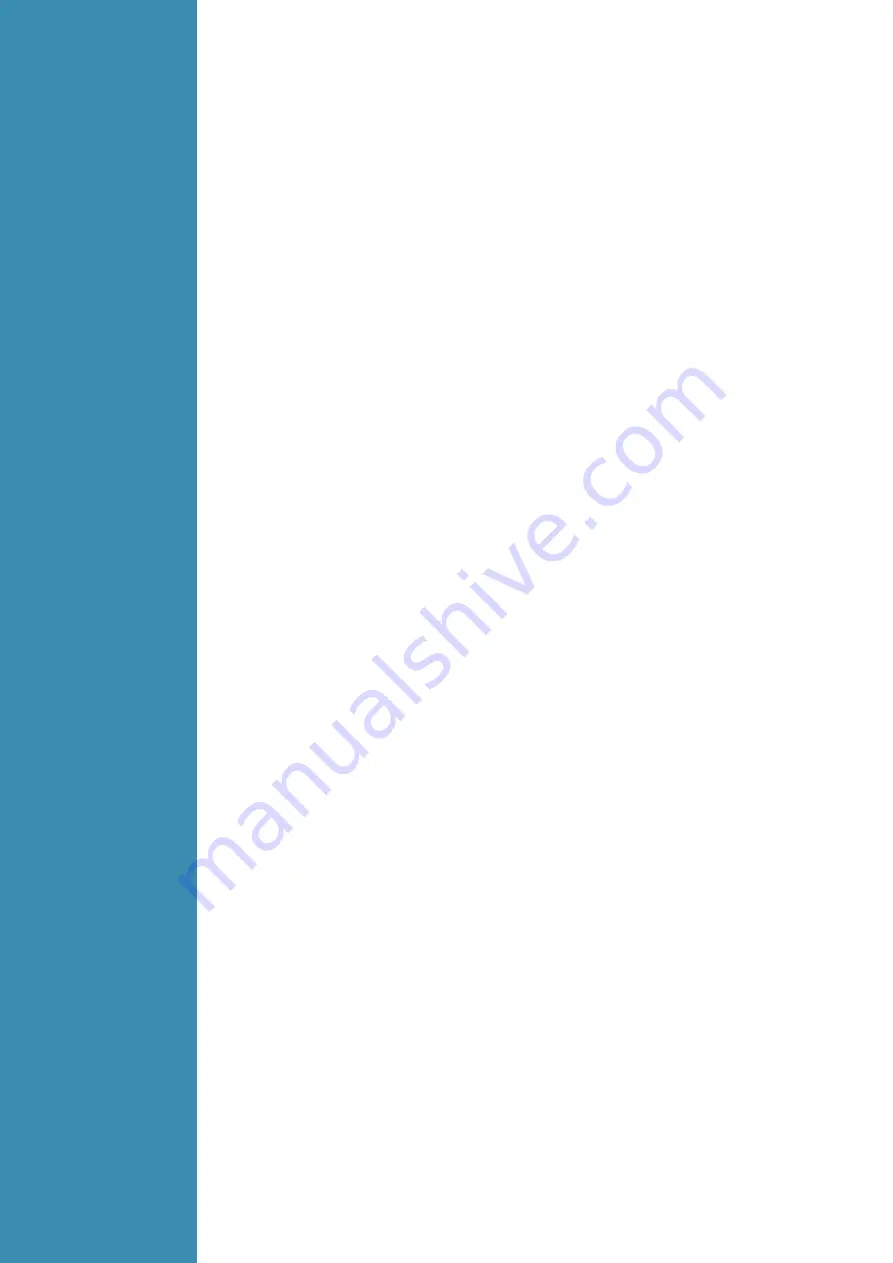
Multifunction Smart Control Knob (3)
Press knob to navigate through the control panel parameters not controlled by specific selector
buttons. Parameter/setting selected will be indicated by the LED on the control panel and the value
shown on the display (8). Adjust the parameter by turning the knob.
Digital multifunction display (8)
Before welding this displays the setting selected or being adjusted using the control knob (3).
During welding it displays welding current. The parameter setting displayed is indicated by
The LEDs on the control panel.
Alarm Indicator (9)
Lights when over voltage, over current, input phase loss or electrical overheating (due to exceeding
duty cycle) is detected and protection is activated. When protection is activated, welding output will
be disabled until the safety system senses the overload has reduced sufficiently and indicator lamp
goes out. May also trigger if machine experiences an internal power circuit failure.
Hot start (14)
Hot start provides extra power when the weld starts to counteract the high resistance of the electrode
and workpiece as the arc is started.
Arc Force (16)
An MMA welding power source is designed to produce constant output current (CC). This means with
different types of electrode and arc length; the welding voltage varies to keep the current constant.
This can cause instability in some welding conditions as MMA welding electrodes will have a minimum
voltage they can operate with and still have a stable arc.
Arc Force control boosts the welding power if its senses the welding voltage is getting too low. The
higher the arc force adjustment, the higher the minimum voltage that the power source will allow. This
effect will also cause the welding current to increase. 0 is Arc Force off, 10 is maximum Arc Force. This is
practically useful for electrode types that have a higher operating voltage requirement or joint types
that require a short arc length such as out of position welds.
VRD Function
VRD stands for Voltage Reduction Device.
This is a safety system that reduces the output voltage from the welding terminals in MMA mode while
the welding output is not in use, to reduce the risk of electric shock from the live output voltage.
The disadvantage of this system is that it makes the striking of the arc more difficult, especially on
restarts and with some types of electrode such as low hydro-gen electrodes.
Lift TIG Mode
Lift TIG is an arc ignition system for basic TIG welding that removes the need to‘scratch’ start or strike
the tungsten on the work piece to start the arc, which can have a negative effect on the weld quality
due to tungsten contamination. Lift arc starting works by gently touching the tungsten on the work
piece and then lifting it off. The control circuit will sense when the tungsten is removed from the work
piece and send a pulse of electricity through the torch that will cause the TIG arc to initiate.
Connection of Output Cables Two sockets are available on this welding machine. For MMA welding
the electrode holder is shown be connected to the positive socket, while the earth lead (work piece)
is connected to the negative socket, this is known as DCEP. However various electrodes require a
different polarity for optimum results and careful attention should be paid to the polarity, refer to the
electrode manufacturers information for the correct polarity.
DCEP: Electrode connected to “+” output socket.
DCEN: Electrode connected to “-” output socket.
3.2
Installation
&
Operation
for MMA
Welding
3.2.1
Set up
installation
for MMA
Welding
Содержание GRAND ARC 320 CEL PFC MV
Страница 19: ...4 4 Electrical schematic drawing...