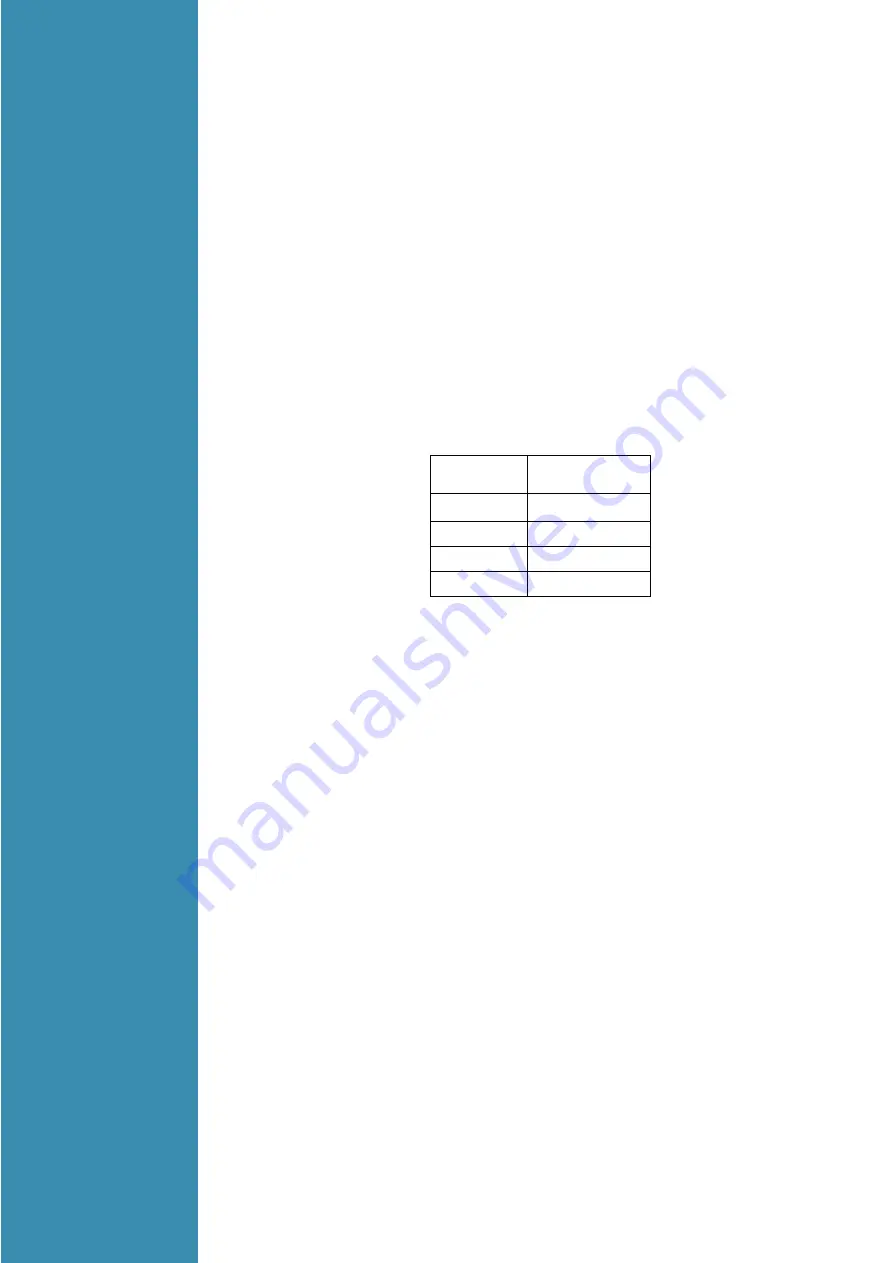
3.2.4
MMA
Welding
Fundamentals
-
Electrode Selection
As a general rule, the selection of an electrode is straight forward,in that it is only a matter of selecting
an electrode of similar composition to the parent metal. However, for some metals there is a choice of
several electrodes, each of which has particular properties to suit specific classes of work. It is
recommend to consult your welding supplier for the correct selection of electrode.
-
Welding Current (Amperage)
Correct current selection for a particular job is an important factor in arc welding. With the current set
too low, difficulty is experienced in striking and maintaining a stable arc. The electrode tends to stick to
the workpiece, penetration is poor and beads with a distinct rounded profile will be deposited. Too
high current is accompanied by overheating of the electrode resulting undercut and burning through
of the base metal and producing excessive spatter. Normal current for a particular job may be
considered as the maximum, which can be used without burning through the work, over-heating the
electrode or producing a rough spattered surface. The table shows current ranges generally
recommended for a general purpose type 6013 electrode.
-
Arc Length
To strike the arc, the electrode should be gently scraped on the work until the arc is established. There
is a simple rule for the proper arc length; it should be the shortest arc that gives a good surface to the
weld. An arc too long reduces penetration, produces spatter and gives a rough surface finish to the
weld. An excessively short arc will cause sticking of the electrode and result in poor quality welds.
General rule of thumb for down hand welding is to have an arc length no greater than the diameter of
the core wire.
-
Electrode Angle
The angle that the electrode makes with the work is important to ensure a smooth, even transfer of
metal. When welding in down hand, fillet, horizontal or overhead the angle of the electrode is generally
between 5and 15 degrees towards the direction of travel. When vertical up welding the angle of the
electrode should be between 80 and 90 degrees to the work piece.
-
Travel Speed
The electrode should be moved along in the direction of the joint being welded at a speed that will
give the size of run required. At the same time, the electrode is fed downwards to keep the correct arc
length at all times. Excessive travel speeds lead to poor fusion, lack of penetration etc, while too slow
a rate of travel will frequently lead to arc instability, slag inclusions and poor mechanical properties.
-
Material and Joint Preparation
The material to be welded should be clean and free of any moisture, paint, oil, grease, mill scale, rust
or any other material that will hinder the arc and contaminate the weld material. Joint preparation will
depend on the method used include sawing, punching, shearing, machining, flame cutting and others.
In all cases edges should be clean and free of any contaminates. The type of joint will be determined
by the chosen application.
Electrode Size
ø mm
Current Range
(Amps)
2.5 mm
60-95
3.2 mm
100-130
4.0 mm
130-165
5.0 mm
165-260
Содержание GRAND ARC 320 CEL PFC MV
Страница 19: ...4 4 Electrical schematic drawing...