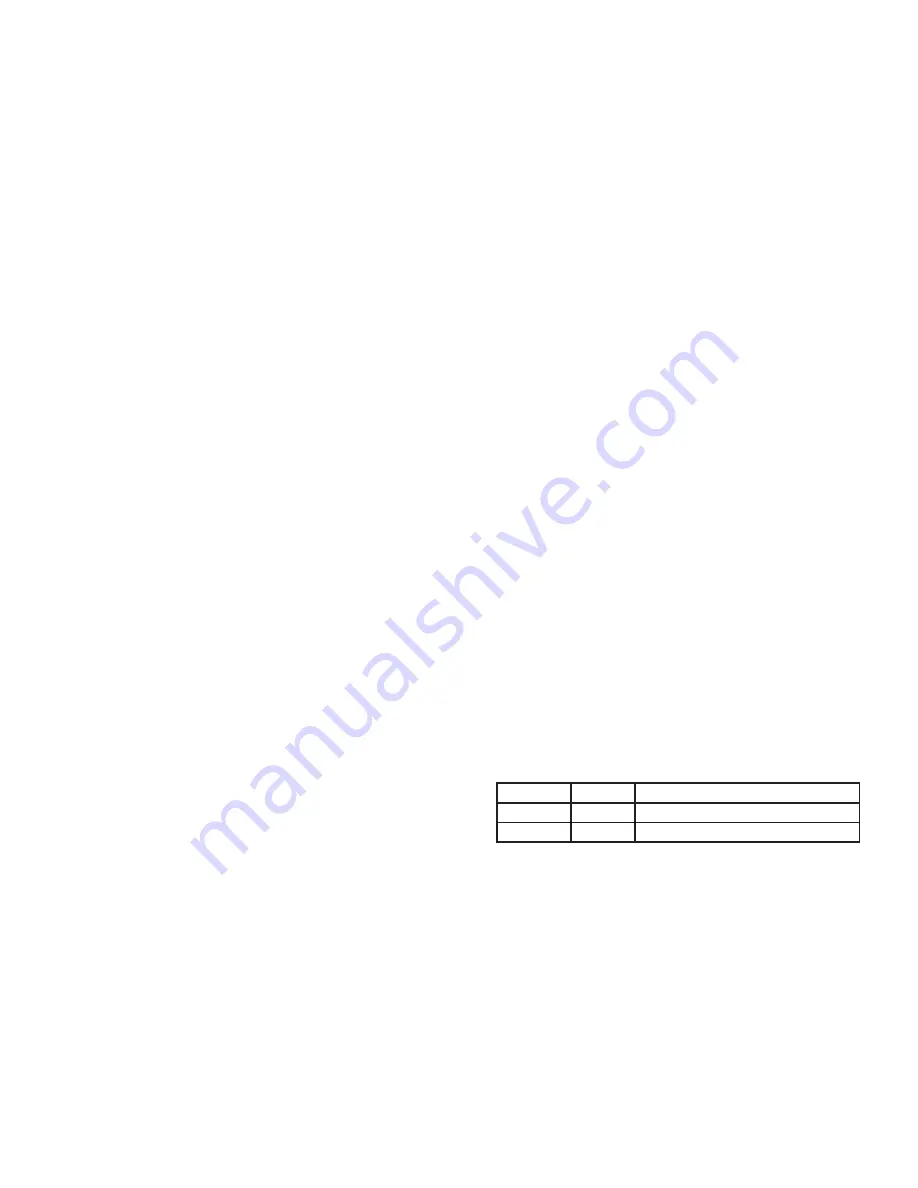
a. Remove the plug from the receptacle prior to touching,
servicing or repairing the pump.
b. To minimize possible fatal electrical shock hazard, use
extreme care when changing fuses. Do not stand in water
while changing fuses or insert your finger into the fuse
socket.
4. Do not operate the pump in a dry basin. This will cause the
pump to become extremely hot, causing burns if touched
and/or damage to the pump.
5. Do not oil the motor. The pump housing is sealed. A high
grade dielectric oil devoid of water has been put into the motor
housing at the factory. Use of other oil could cause serious
electric shock and/or permanent damage to the pump.
6. This pump’s motor housing is filled with a dielectric oil for motor
heat transfer and lifetime lubrication of the bearings. This oil is
non-toxic to aquatic life. However, suffocation can occur if oil is
left on the water surface. If oil escapes the motor housing, it can
be removed from the surface quickly by placing newspapers
on the water surface to soak up the oil.
7. In any installations where property damage and/or personal
injury might result from an inoperative or leaking pump due to
power outages, discharge line blockage, or any other reason, a
backup system(s) and/or alarm should be used.
INSTALLATION
Install the pump in a suitable gas-tight basin that is at least 18” in
diameter and 24” deep.
Pumps features a 1-1/2” female NPT discharge.
Pump can be installed with ABS, PVC, polyethylene or galvanized
steel pipe. Proper adapters are required to connect plastic pipe
to pump.
Place the pump on a hard level surface. Never place pump directly
on clay, earth or gravel surfaces.
Use a check valve in the discharge line to prevent back flow of
liquid into the basin. The check valve should be a free-flow valve
that will easily pass solids.
CAUTION:
For best performance when handling solids, install the
check valve in a horizontal position or at an angle or no more than
45°. Do not install the check valve in a vertical position as solids
may settle in the valve and prevent opening on start-up.
When a check valve is used, drill a relief hole (1/8” or 3/16” diameter)
in the discharge pipe. This hole should be located below the floor
line between the pump discharge and the check valve. Unless such
a relief hole is provided, the pump could air lock and will not pump
water, even though it will run.
OPERATION
TESTING PUMP OPERATION
RFS SERIES SEWAGE EJECTOR PUMPS:
1. These pumps are equipped with a remote float switch.
2. These pumps are installed in a basin with a sealed cover, so
switch operation cannot be observed. The sump cover usually
will have a spare hole that is plugged with a rubber plug. This
plug can be removed and switch operation can be observed.
3. Plug power cord and remote float switch power cord into a
grounded receptacle with voltage consistent with pump voltage
as indicated on pump nameplate.
4. Run water into basin until pump starts.
5. Be sure gate valve in discharge line is open.
6. Allow pump to operate through several on-off cycles.
MANUAL SEWAGE EJECTOR PUMPS:
The power cord for these pumps can be plugged directly into a
properly grounded receptacle with voltage consistent with pump
nameplate for continuous pump operation.
CAUTION:
This type of operation should be used only for emer-
gency use or when a large volume of water is to be pumped. Do
not allow the pump to run dry; this may damage the pump and
void the warranty.
MAINTENANCE
If pump does not operate properly, consult the troubleshooting
chart. If trouble cannot be located with the steps shown, consult
your pump dealer or take pump to a Little Giant authorized
service center.
CAUTION:
When working on pump or switch, always unplug
pump power cord in addition to removing fuse or shutting off circuit
breaker before working on pump.
CLEANING IMPELLER AND VOLUTE
1. Remove screws that hold volute to motor housing.
2. Remove volute and clean impeller and volute passage. Do not
use strong solvents on impeller.
3. Be sure impeller turns freely after cleaning.
4.
CAUTION:
DO NOT REMOVE IMPELLER. REMOVAL OF
IMPELLER REQUIRES SPECIAL TOOLS AND IS TO BE DONE
ONLY BY AN AUTHORIZED SERVICE CENTER.
DO NOT REMOVE MOTOR HOUSING COVER. WARRANTY IS
VOID IF MOTOR HOUSING COVER, IMPELLER OR SEALS HAVE
BEEN REMOVED.
ANY REPAIR ON MOTOR MUST BE DONE BY AN AUTHORIZED
LITTLE GIANT SERVICE CENTER.
WIRING
Check local electrical and building codes before installation. The
installation must be in accordance with their regulations as well as
the most recent National Electrical Code (NEC).
To conform to the National Electrical Code all pumps must be wired
with 14 AWG or larger wire. For runs to 250', 14 AWG wire is suffi-
cient. For longer runs, consult a qualified electrician or the factory.
Pump should be connected or wired to its own circuit with no
other outlets or equipment in the circuit line.Fuses and circuit
breaker should be of ample capacity in the electrical circuit. See
chart below.
H.P.
VOLTAGE FUSE OR CIRCUIT BREAKER AMPS
1/3 or 4/10
115
20
1/3 or 4/10
230
15
REMOTE FLOAT SWITCH LEVEL CONTROL
The RFS series pumps are equipped with a remote float switch
level control. This level control is sealed in a polypropylene float
cylinder. For automatic operation, the pump must be plugged
or wired into a remote float switch. Pump will run continuously if
plugged directly into an electrical outlet.
When the level rises in the basin, the cylinder floats up with the
level. When the cylinder position is at an angle of about 45°, the
switch activates and starts the pump motor.
As the level draws down, the cylinder floats down and when it
is again at an angle of about 45°, the switch deactivates and the
pump motor stops.
NOTE:
BE CERTAIN PUMP IS SECURE IN BASIN AND CYLINDER
FLOATS UNOBSTRUCTED WITHOUT TOUCHING THE BASIN
WALLS OR PLUMBING.
3