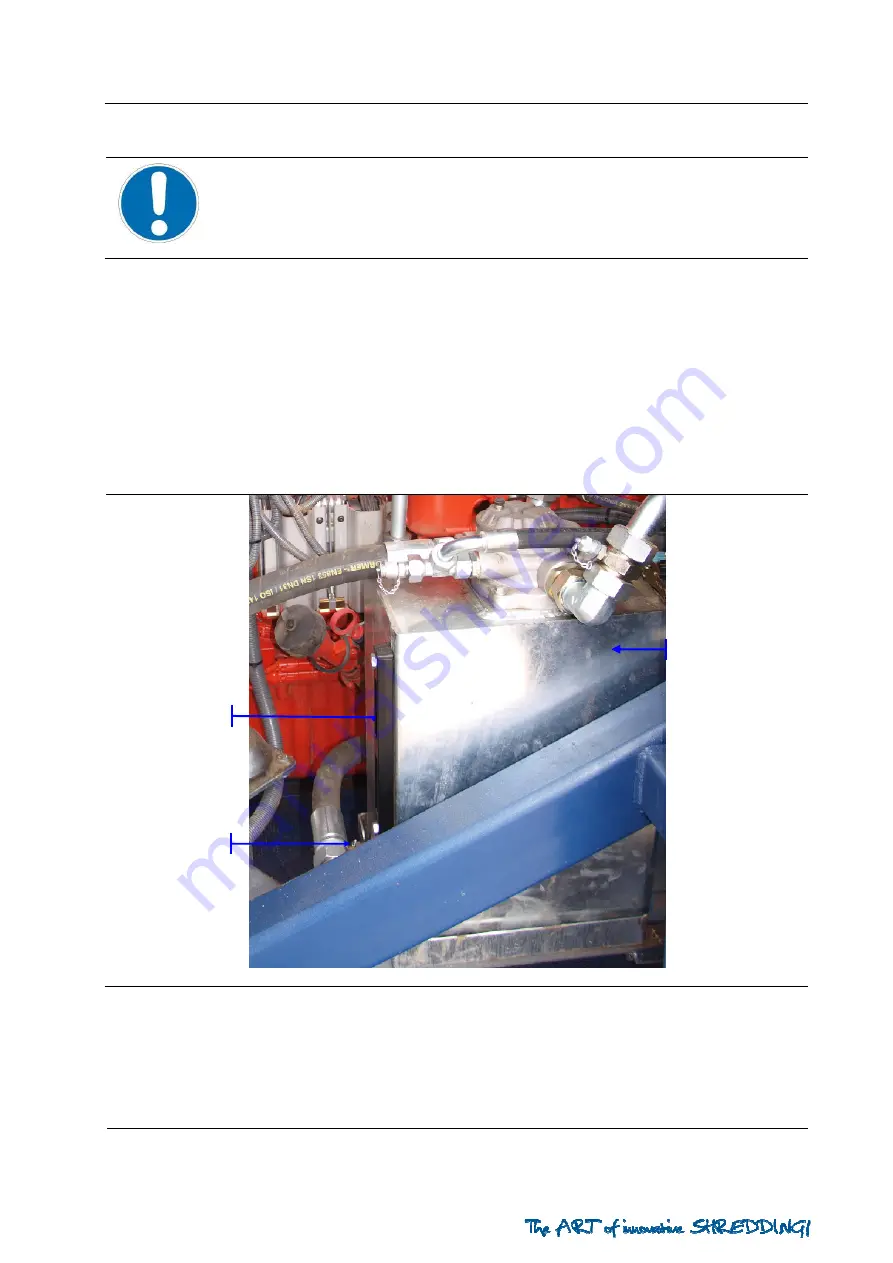
URRACO 75 D
S
ERVICE GUIDELINES
Managing director
LINDNER
Mobile Shredder GmbH
Industriestrasse 1A
D-99820 Hörselberg / Eisenach
Service hotline:
+49 (0) 36920 - 7269 - 600
Manuel Lindner
Gerhard Buhl
Walter Geiger
Page - 20 - of - 38 -
1.7.-8
Checking the Hydraulic Oil Level / Changing the Hydraulic Oil
Maximum oil filling is only permissible with retracted hydraulic cylinders.
Checking the oil level
If the oil drops below the minimum level, the <Hydraulic oil level> indicator light lights up on
the control panel. In this case, the machine switches off immediately.
The hydraulic oil level must be checked daily via the sight glass; the oil should be
approximately in the upper third of the sight glass. Ensure that the shedder is standing
horizontally.
Oil drain plug
Sight glass
Hydraulic oil tank