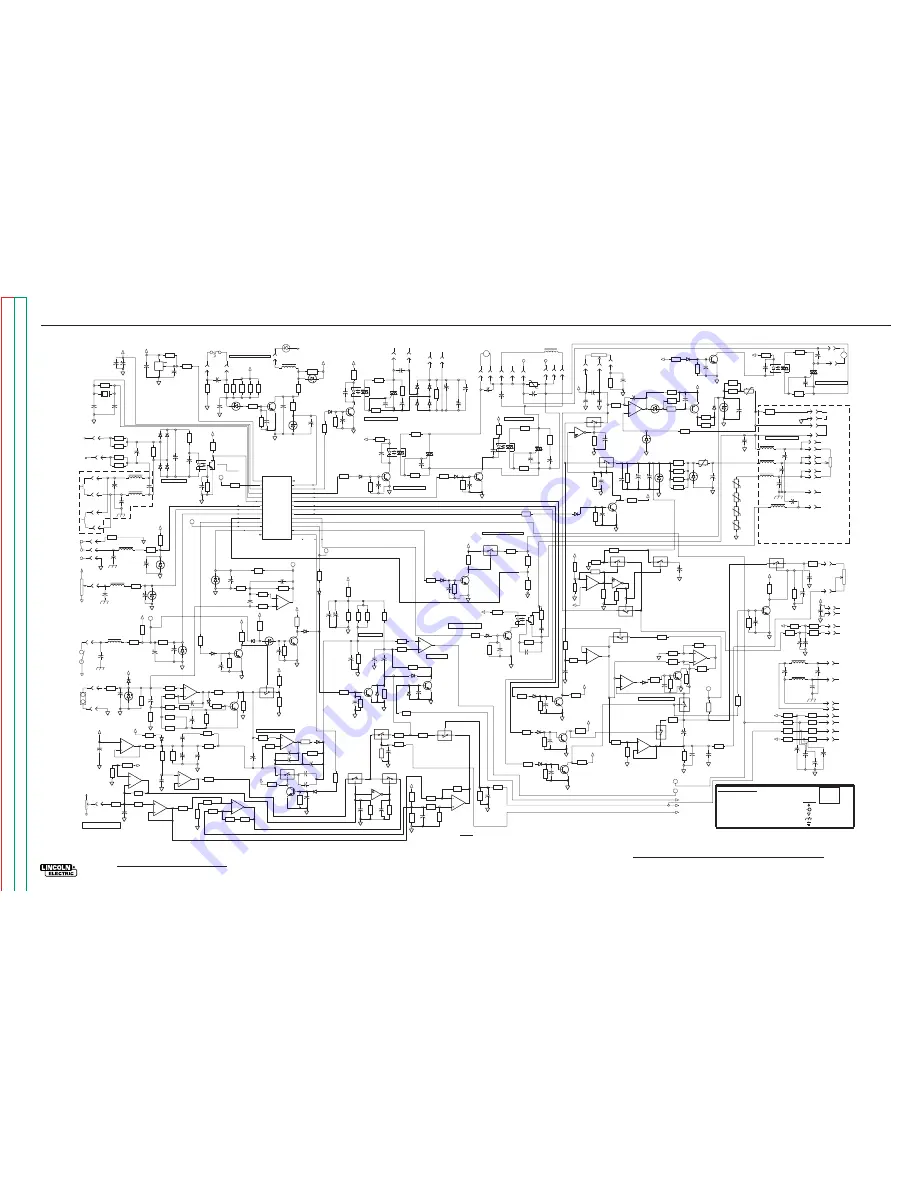
G-5
ELECTRICAL DIAGRAMS
SQUARE WAVE TIG 275
G-5
Retur
n to Section TOC
Retur
n to Section TOC
Retur
n to Section TOC
Retur
n to Section TOC
Retur
n to Master TOC
Retur
n to Master TOC
Retur
n to Master TOC
Retur
n to Master TOC
Control Board Schematic (G3358-2)
J7A
6
.39mH
L6
START
PRESET
LINE_SYNC
OUTPUT_ENABLE
PTC-
TRI-
WORK VOLT.
OCI-
ELECT.VOLT
X-
SEE SHEET 1
DOWN SLOPE POT
METER BOARD INTERFACE
REMOTE PROTECTION
ROBOTIC
J7
1
J7
6
J7A
2
ROBOTIC
3000V
.0047
C95
J7
8
J4
3
D90
5W
15V
DZ36
J7
2
INTERFACE
INTERFACE
AMPTROL
J7A
8
J7
5
J7A
1
J7A
4
J7
4
3000V
.0047
C107
J7A
5
Q27
2N4403
J6
4
J6
3
10.0K
R601
METER BOARD INTERFACE
J4
8
J4
10
J4
7
J4
6
J4
4
50V
0.1
C211
J4
5
C258
AUTO
+5V
47.5K
R561
X10
8
6
9
X10
3
5
4
50V
.68
C227
26.7K
R525
26.7K
R521
100K
R526
100K
R522
50V
0.1
C818
X9
7
6
5
AUTO
10.0K
R560
D84
2.21K
R541
C259
+5V
+15V
10.0K
R481
4.75K
R483
X11
14
13
12
D95
4.75K
R625
33.2K
R616
2_STEP
15.0K
R486
X14
8
6
9
47.5K
R624
X14
1
13
2
47.5K
R20
1.50K
R468
C250
10.0K
R573
C13
1.00K
R12
D98
221K
R21
1.00K
R11
4.7
35V
C14
10.0K
R563
2_STEP
UP/DOWN SLOPE CIRCUIT
MACH_PRESET
15.0K
R482
4.75K
R564
33.2K
R622
Q39
2N4401
X11
8
9
10
10.0K
R627
+15V
+15V
+15V
STICK
50V
.0047
C18
6.81K
R559
10.0
R621
100K
R578
47.5K
R579
4.75K
R576
2.21K
R628
X17
3
5
4
6.81K
R580
10.0
R480
+5V
10.0K
R65
1.00K
R534
1.00K
R536
1.00K
R537
X10
1
13
2
C160
50V
.68
C165
D2
475
R22
47.5K
R567
Q32
2N4401
6.81K
R565
C248
10.0K
R566
Q31
2N4401
22.1K
R33
D85
C247
6.81K
R562
50V
.0047
C37
100V
47p
C15
50V
0.1
C25
X1
8
9
10
START
15.0K
R519
STICK
221K
R56
1.00K
R25
1.00K
R13
50V
0.1
C238
100K
R545
221
R26
47.5K
R570
D86
50V
.68
C24
X10
10
12
11
100K
R415
+5V
UP_SLOPE
CLN
FILTER_CAP
PEN
ERROR AMPLIFIER CIRCUIT
1W
5.1V
DZ22
475
R500
10.0K
R501
.39mH
L11
1.00K
R315
1.00K
R216
.39mH
L1
.39mH
L2
.39mH
L10
1400V
.0047
C65
D12
3000V
.0047
C80
1.00K
R117
1400V
.0047
C106
3000V
.0047
C66
10.0K
R499
1W
5.1V
DZ21
1.00K
R118
AC
GND
+5V
+5V
GND
GND
4.75K
R506
4.7
35V
C213
4.7
35V
C220
3000V
.0047
C244
3000V
.0047
C243
GND
1.00K
R492
1.00K
R493
.39mH
L8
SHEET 2
J5: 14 PIN
J8: 16 PIN
J4: 10 PIN
UP_SLOPE
ELECTRICAL SYMBOLS PER E1537
MFD
1A, 400V
G3358_2BA
RESISTORS = Ohms (
CAPACITORS =
DIODES =
10.0
R611
X14
3
5
4
10.0K
R479
22.1K
R484
47.5K
R603
10.0K
R604
22.1K
R485
X11
7
6
5
C265
3000V
.0047
C196
Q38
2N4401
50V
0.1
C212
1.00K
R635
1.00K
R634
3000V
.0047
C195
1.00K
R636
1.00K
R497
1400V
.0047
C197
.39mH
L7
50V
0.1
C273
50V
0.1
C274
1.00K
R637
50V
0.1
C209
50V
0.1
C208
1.00K
R498
1.00K
R491
1.00K
R496
1.00K
R495
1.00K
R494
PHASE_FIRE
WORK VOLT.
50V
0.1
C210
2.21K
R477
C201
475
R487
C204
ELECT.VOLT
SHUNT_CURRENT
AC
CURRENT CONTROL
LINE_SYNC
PHASE_B
PHASE_A
OUTPUT_ENABLE
STICK
47
35V
C203
BALANCE CONTROL CIRCUIT
NOTES :
FRAME CONNECTION
AUTO
NOT SHOW THE EXACT COMPONENTS OR CIRCUITRY OF CONTROLS HAVING A COMMON CODE
WITHOUT AFFECTING THE INTERCHANGEABILITY OF A COMPLETE BOARD, THIS DIAGRAM MAY
N.A. SINCE COMPONENTS OR CIRCUITRY ON A PRINTED CIRCUIT BOARD MAY CHANGE
NUMBER.
SPARE PARTS AND IC POWER CONNECTION SHOW ON SHEET 1
EARTH GROUND CONNECTION
BALANCE CONTROL
1.2 Vref
J1: 8 PIN
J7A: 8 PIN
UNLESS OTHERWISE SPECIFIED)
(UNLESS OTHERWISE SPECIFIED)
UNLESS OTHERWISE SPECIFIED)
.022/50V
1/4W
(
J3: 4 PIN
J6: 4 PIN
COMMON CONNECTION
LABELS
LAST NO. USED
POWER SUPPLY SOURCE POINT
VOLTAGE NET
Q-
DZ-
J7: 8 PIN
J2: 4 PIN
/AUTO
GENERAL INFORMATION
D-
R-
C-
SUPPLY
1.00K
R535
Q30
2N4401
100K
R532
100K
R419
100K
R528
C163
X9
8
9
10
C228
1.50K
R530
47.5K
R527
47.5K
R531
X5
3
4
C166
100K
R539
4.75K
R529
C159
100K
R411
X9
1
2
3
50V
0.1
C183
10.0K
R464
J5
11
100K
R524
10.0K
R410
100K
R523
1.00M
R520
6.81K
R466
1.2V
100
R508
C191
Q26
2N4401
.39mH
L9
47.5K
R557
C222
4.7
35V
C221
1W
5.1V
DZ23
Q41
2N4401
475K
R469
DC
ROBOTIC ARC_SENSED
ARC_SENSED
MAX FIRE ANGLE
6.81K
R555
10.0K
R623
J5
13
D96
1W
3.3V
DZ39
D97
C271
X1
1
2
3
33.2K
R16
10.0K
R467
D78
33.2K
R28
4.75K
R509
GAS
C79
Q11
2N4401
10.0K
R182
C72
1.50K
R186
HI-FREQ. turning on when noise coupled through
AC line or when switching power switch on
The snubber is needed for TRI1 to prevent
HF
START
2_STEP
and off.
BACKGROUND CURRENT
1.00K
R205
D77
+15V
50V
0.1
C207
6.81K
R474
G
MT2
MT1
TRI2
6.81K
R178
+15V
+15V
MACH
+15V
10.0K
R596
47.5K
R574
D72
2.21K
R600
C266
Q34
2N4401
D88
X17
1
13
2
ARC_SENSED
REM_SENSE
CTRL POT AUTO CONNECTION
/SENSE_ENABLE
LOC_REM
6.81K
R572
UP_SLOPE
REM_SENSE
C75
G
MT2
MT1
TRI1
3043
OCI2
2
6
1
4
X11
1
2
3
150
R618
50V
0.1
C270
68.1K
R23
3043
OCI3
2
6
1
4
1.00K
R211
C100
CNY17-3
OCI5
4
2
1
6
5
X17
8
6
9
4.75K
R585
400V
.1
C84
C74
10.0K
R179
D76
6.81K
R542
C91
Q18
2N4401
GAS DRIVING CIRCUIT
PULSER_PRESET
10.0K
R584
3000V
.0047
C88
4.7
35V
C272
+
t
.24
PTC2
Set control pot at max.
+
t
.24
PTC5
50V
0.1
C152
+
t
.24
PTC6
+
t
.24
PTC4
.39mH
1A
L3
5W
10V
DZ38
3.32K
R472
.39mH
L4
+15V
3000V
.0047
C190
221
R319
221
R317
600V
.05
C63
2.21K
R476
GND
B
(-)
ARC_SENSED
PULSER
REMOTE AMPTROL
A
(+)
ARC_SENSED
CONTROL
ROBOTIC
GND
4.2V @ 70mA
4.8V @ 50mA
PULSER SUPPLY:
600V
.05
C62
.39mH
L5
221
R318
20.0
R587
100K
R549
221
R316
C264
C200
10.0K
R612
J4
1
J4
2
J4
9
100K
R602
J5
4
J5
14
+
t
56
PTC3
X14
10
12
11
C
F
CHASSIS CONNECTION
+15V
20.0
R588
GND
10.0K
R556
X16
3
5
4
3.01K
R548
400A/200mV
100V
47p
C5
AC
221K
R3
50V
820p
C4
D1
1.00K
R5
68.1K
R543
1W
15V
DZ2
3000V
.0047
C242
X1
7
6
5
D79
J2
1
J2
2
Q28
2N4401
150
R7
221K
R558
D83
50V
.0047
C234
10.0K
R546
1.00K
R4
1.50K
R547
C6
10.0K
R6
15.0K
R552
+15V
+15V
-
AC/DC
MICRO-
SWITCH
SHUNT CURRENT AMPLIFIER
15.0K
R553
1.00K
R1
+15V
C246
61.9K
R544
D99
50V
.0047
C21
100K
R538
1.0
35V
C28
1.00M
R31
X13
14
13
12
68.1K
R626
8.25K
R24
C29
100
R27
301
R518
REMOTE PROTECTION
TRIGGER
ROBOT
100V
22p
C214
100V
22p
C215
CURRENT CONTROL
+5V
L_GND
C1
Q24
2N4401
4.75K
R473
THERMAL LED
1.00K
R438
4.75K
R507
Q29
2N4401
2.67K
R326
J8
4
D70
X16
10
12
11
Q1
2N4401
10.0K
R436
C169
10.0K
R18
C19
1W
5.1V
DZ20
1W
15V
DZ1
1.00K
R215
J5
12
J5
7
J5
6
J5
8
J7A
7
J7A
3
J7
7
J7
3
J8
6
C36
AMPTROL
TRIGGER
STICK
POSTFLOW
+5V
2_STEP
4_STEP
18VAC
X9
14
13
12
X13
1
2
3
C22
D9
4.75K
R505
50V
150p
C54
475K
R125
CNY17-3
OCI1
4
2
1
6
5
D13
3.32K
R144
C39
20
50V
C38
681
R114
1.00K
R516
10.0K
R513
Vss
28
Vdd
14
PD5
AN3/PC3
/IRQ
/RESET
TCMP
VRH/PC7
OSC1
OSC2
PC0
AN2/PC4
AN0/PC6
PD7
PA7
PC2
PC1
AN1/PC5
PA3
PB5/SD0
PA4
PA2
PB6/SDI
PA6
PA1
PA0
PB7/SCK
PA5
MC68HC705
X12
3
16
25
17
12
10
11
8
23
27
4
18
13
19
21
20
1
24
15
26
22
2
7
5
6
9
1.00K
R515
1.00K
R517
100V
47p
C225
D17
MACH
+15V
FAN
SHUNT_CURRENT
+15V
+15V
/TRIGGER
TRIGGER CIRCUIT
CURRENT_FB
SOFT_START
REM_SENSE
AC
POSTFLOW
MODE
FAN
Trigger open
close
OUTPUT_ENABLE
FILTER_CAP
ARC_SENSED
START
LOC_REM
UP_SLOPE
STICK
/SENSE_ENABLE
BG_CURRENT
2_STEP
GAS
HF
/SHUTDOWN
50V
0.1
C224
47.5K
R514
50V
820p
C223
X1
14
13
12
1W
5.1V
DZ24
HV XFMR
23 VAC
LOCAL CONTROL POT
FAN
FAN DRIVING CIRCUIT
SOLENOID
115VAC
SUPPLY
(-)
(+)
BACKGROUND
100K
R503
1.00K
R504
1.0
35V
C217
S-8054HN
Vdd
Vss
RES
X15
50V
0.1
C218
C216
50V
0.1
C219
1400V
.0047
C2
J3
2
1W
3.3V
DZ4
J5
5
10.0K
R613
47.5
R9
+5V
L_GND
L_GND
L_5V
L_5V
PT_Vsp
TSTAT
THERMAL SHUTDOWN CIRCUIT
N_5V
J3
1
2.21K
R323
47.5
R10
2.21K
R324
2.21K
R8
.39mH
L12
2.21K
R325
150
R63
1.00M
R502
130
4.0MHz
Y1
3043
OCI4
2
6
1
4
1.00K
R594
J8
8
+t
56
PTC1
C170
47.5
R321
10.0K
R595
+5V
26.7
R439
1400V
.0047
C104
267
R196
D59
1N5402
1400V
.0047
C180
1400V
.0047
C108
3300
50V
C174
10.0K
R440
1400V
.0047
C103
150
R490
1W
15V
DZ35
X16
1
13
2
X5
5
6
C257
1400V
.0047
C158
10.0K
R597
1W
5.1V
DZ29
X13
7
6
5
50V
0.1
C193
+15V
D57
1N5402
3300
50V
C173
C171
D58
1N5402
400V
.1
C172
G
MT2
MT1
TRI3
HF DRIVING CIRCUIT
MACH_PRESET
267
R197
26.7
R195
D56
1N5402
1.50K
R181
C40
C261
J8
13
J5
10
J5
9
120J
175V
TP5
J8
10
J8
7
J8
12
J8
15
J8
2
J8
5
G
MT2
MT1
TRI4
C262
J8
16
1400V
.0047
C263
3043
OCI6
2
6
1
4
C260
D91
10.0K
R591
6.81K
R590
J8
11
J5
1
J5
2
J5
3
50V
0.1
C198
Q37
2N4401
267
R593
1.50K
R592
J8
3
267
R437
1400V
.0047
C181
1.50K
R435
J8
14
+15V
+15V
FAN
+15V
47.5
R322
100K
R583
X5
9
8
X16
8
6
9
C254
C255
332K
R633
1.0
35V
C239
Q40
2N4401
50V
0.1
C153
4.75K
R614
1W
5.1V
DZ37
6.81K
R632
MACH
OUTPUT_ENABLE
100K
R630
100K
R631
C268
10.0K
R615
10.0K
R620
X17
10
12
11
47.5K
R629
X13
8
9
10
+15V
PULSER
PULSER_PRESET
1.0
35V
C154
6.81K
R568
1N4936
D4
50V
.0047
C27
1N4936
D64
START
2_STEP
PHASE FIRE
UP_SLOPE
221
R32
7.68K
R17
50V
0.1
C269
50V
0.1
C30
10.0K
R617
50V
150p
C194
D87
C249
Q33
2N4401
10.0K
R569
22.1K
R66
50V
.0047
C31
1.00K
R64
Q5
2N4401
Q2
2N4401
D7
NOTE: Lincoln Electric assumes no responsibility for liablilities resulting from board level troubleshooting. PC Board repairs will invalidate your factory warranty. Individual Printed Circuit Board Components are not
available from Lincoln Electric. This information is provided for reference only. Lincoln Electric discourages board level troubleshooting and repair since it may compromise the quality of the design and may result
in danger to the Machine Operator or Technician. Improper PC board repairs could result in damage to the machine.
G3358-2
7-24-98