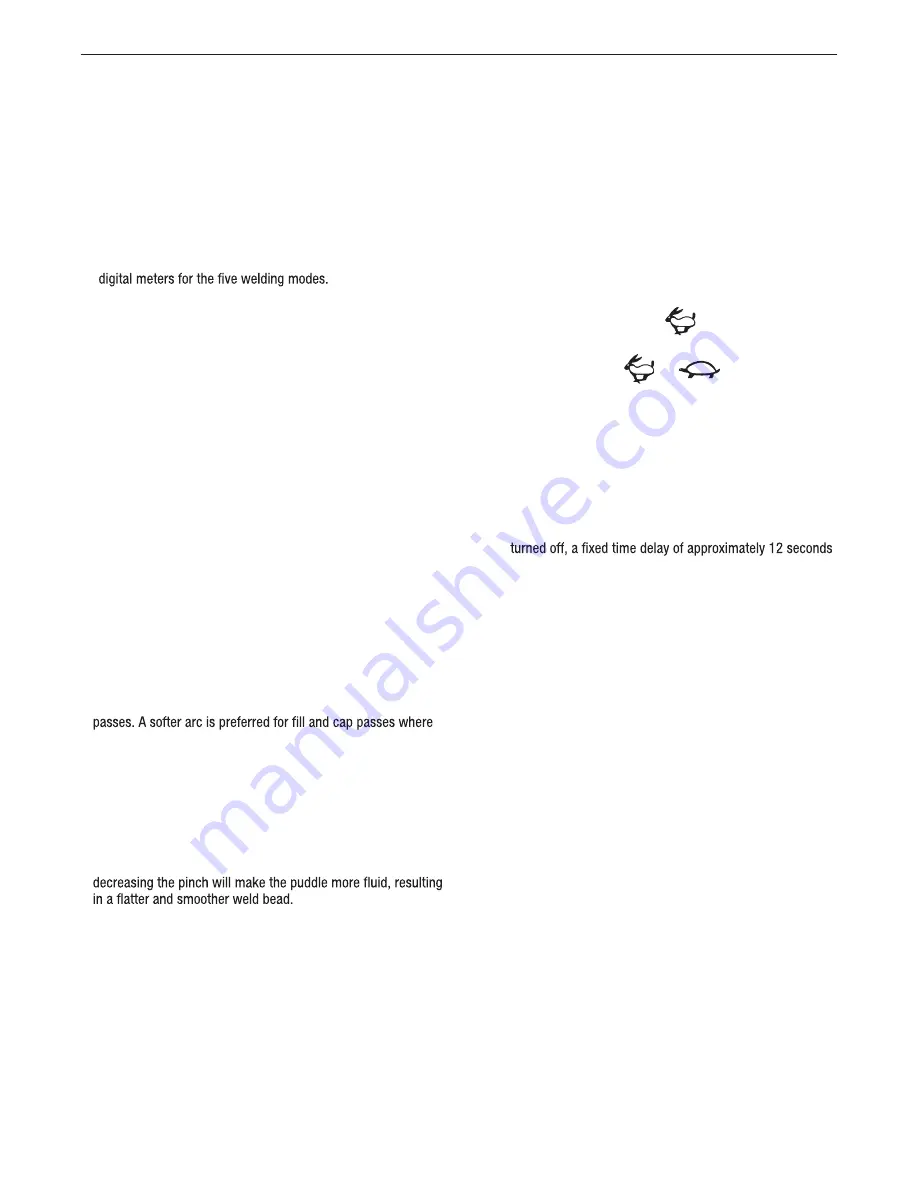
B-4
OPERATION
3. CROSSLINC INDICATOR LIGHT -
When a CrossLinc
enabled device is connected with the machine using the stan-
dard weld power cable and the device's sense lead is attached
to the work piece, the CrossLinc light will automatically illumi-
nate on both the machine and the device. No additional pairing
of the machine to the device is needed. This light indicates the
CrossLinc connection is active and that control of the voltage
and current can be made at the device.
4. OUTPUT CONTROL -
The OUTPUT CONTROL knob is
used to preset the output voltage or current as displayed on the
5. WELD TERMINALS ON SWITCH -
Output is enabled
when in the ON position. Output is remotely controlled when in
the REMOTE position. This control is not active in ArcLink
®
modes.
6. ARC CONTROL -
The ARC CONTROL knob is active in the
CC-STICK, DOWNHILL PIPE, and CV-WIRE modes, and has dif-
ferent functions in these modes. This control is not active in the
TOUCH START TIG, ARC GOUGING, or ArcLink modes.
CC-STICK mode:
In this mode, the ARC CONTROL knob sets the
short circuit current (arc force) during stick welding. Increasing
the number from -10 (Soft) to +10 (Crisp) increases the short
circuit current and prevents sticking of the electrode to the plate
while welding.
This can also increase spatter. It is recommended that the ARC
CONTROL be set to the minimum number without electrode
sticking. Start with a setting at 0.
DOWNHILL PIPE mode:
In this mode, the ARC CONTROL knob
sets the short circuit current (arc force) during stick welding to
adjust for a soft or a more forceful digging arc (Crisp).
Increasing the number from -10 (Soft) to +10 (Crisp) increases
the short circuit current which results in a more forceful digging
arc. Typically a forceful digging arc is preferred for root and hot
weld puddle control and deposition (“stacking” of iron) are key
to fast travel speeds. It is recommended that the ARC CONTROL
be set initially at 0.
CV-WIRE mode:
In this mode, the ARC CONTROL knob changes
the inductance ("pinch") of the current. By adjusting the pinch,
the the rate of current rise will change when the electrode short
circuits to the work.
Increasing the pinch from -10 to +10 may reduce spatter, while
7. WELD MODE SELECTOR SWITCH
Provides six selectable welding modes:
CV-WIRE
DOWNHILL PIPE
CC-STICK
TOUCH START TIG
ARC GOUGING
ARCLINK
8. 42V / 120V WIRE FEEDER VOLTAGE SWITCH
Toggles output of 14-pin connector to voltage requirement of
wire feeder. (Located above 14-pin connector.)
9. 5-PIN CONNECTOR
- For attaching an ArcLink
®
wire
feeder control cable.
10. RUN / STOP / IDLE SWITCH -
Toggling the switch to
the RUN position energizes the fuel solenoid for approximately
30 seconds. The engine must be started within that time or
the fuel solenoid will degenerize, and the switch must be tog-
gled to reset the timer.
Has two positions as follows:
1) In the “HIGH IDLE” position , the engine runs at the
high idle speed controlled by the governor.
2) In the “AUTO IDLE” / position, the idler
operates as follows:
• When switched from “High” to “Auto” or after starting the
engine, the engine will operate at full speed for approxi-
mately 12 seconds and then go to low idle speed.
• When the electrode touches the work or power is drawn
for lights or tools (approximately 100 watts minimum) the
engine accelerates and operates at full speed.
• When welding ceases and the auxiliary power load is
starts.
• If the welding or auxiliary power load is not restarted
before the end of the time delay, the idler reduces the
engine speed to low idle speed.
• The engine will automatically return to high idle speed
when the welding load or auxiliary power load is reap-
plied.
Idler Operational Exceptions -
When the WELDING
TERMINALS switch is in the REMOTELY CONTROLLED position
or the MODE SELECTION switch is in the ArcLink
®
position the
idler will operate as follows:
• When the triggering device (amptrol, arc start switch, etc.)
is pressed, the engine will accelerate and operate at full
speed, provided a welding load is applied within approxi-
mately 12 seconds.
• If the triggering device remains pressed but no welding
load is applied within approximately 12 seconds, the
engine may return to low idle speed.
• If the triggering device is released or welding ceases, the
engine will return to low idle speed after approximately 12
seconds.
AIR VANTAGE
®
600X-I