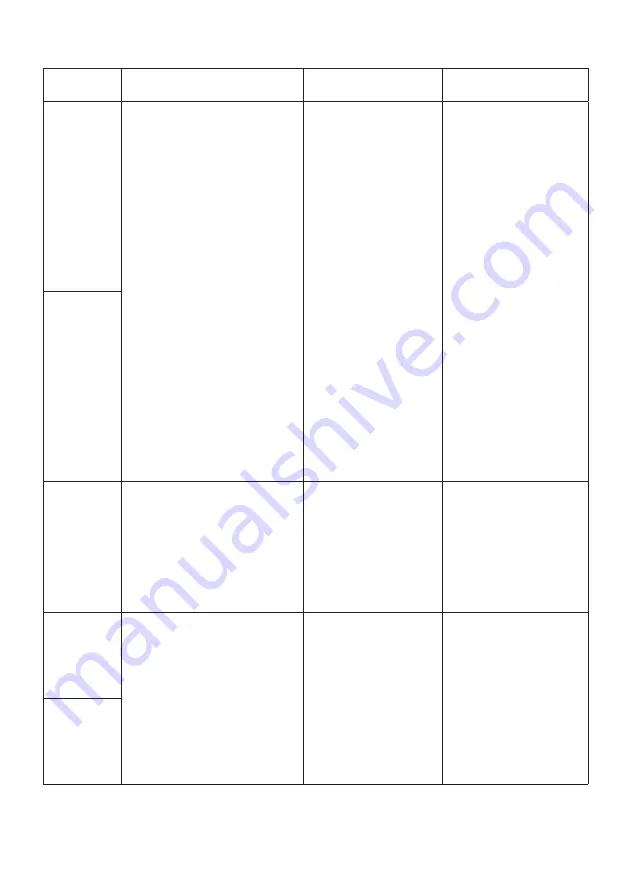
Page 39 of 76
Actuator configurations available for IC Advanced
,
Proportional and Parallel
Pre-configured
Customised range
Description
Current limit
inwards *
10A for both current limit
directions. (When the current
outputs are at zero, it means that
they are at maximum value 10A).
Be aware:
When the actuator comes with
current cut-off limits that are
factory pre-configured for certain
values, the pre-configured values
will be the new maximum level of
current cut-off.
This means that if the current
cut-off limits are pre-configured
to 7A, it will not be possible to
change the current limits through
BusLink to go higher than 7A.
If the temperature drops
below 0°C, all current limits
will automatically increase
to 15A for 24V, and 20A for
12V, independent of the pre-
configured value.
Recommended range:
3A to 10A
If the temperature drops
below 0°C, all current
limits will automatically
increase to 15A for
24V, and 20A for 12V,
independent of the pre-
configured value
.
The actuator’s unloaded
current consumption is
very close to 4A, and
if the current cut-off is
customised below 4A
there is a risk that the
actuator will not start.
The inwards and outwards
current limits can be
configured separately and
do not have to have the
same value.
Current limit
outwards *
Max. speed
inwards/
outwards
100% equal to full performance
Please note: for parallel actuators
the full performance equals 80%
of the max. speed.
Lowest recommended
speed at full load: 60%
It is possible to reduce
the speed below 60%,
but this is dependable
on load, power supply
and the environment.
The speed is based on a
PWM principle, meaning
that 100% equals the
voltage output of the
power supply in use, and
not the actual speed.
Virtual
endstop
inwards
0mm for both virtual enstop
directions.
(When the virtual endstops are at
zero, it means that they are not
in use).
It is only possible to run
the actuator with one
virtual endstop, either
inwards or outwards.
The virtual endstop
positions are based on
hall sensor technology.
The positioning needs to
be initialised from time
to time by reaching one
of the physical endstops
of the actuator, which
must be available for
initialisation.
Virtual
endstop
outwards
Содержание TECHLINE LA33
Страница 1: ...Page 1 of 76 LINAK COM TECHLINE Actuator LA33 User manual...
Страница 74: ...Page 74 of 76...
Страница 75: ...Page 75 of 76...