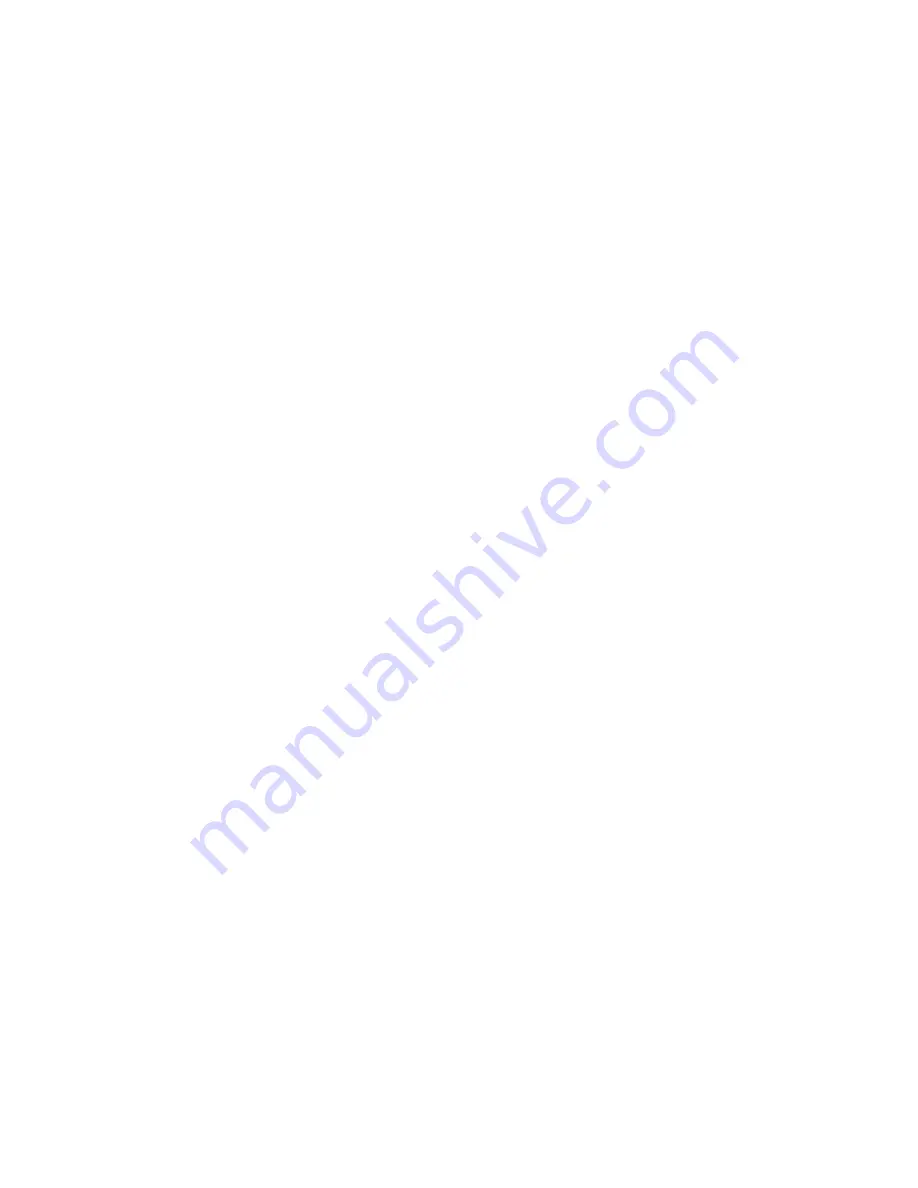
3-2. Focus Servo
The aim of Focus Servo is to maintain the distance between object lens of P/U and disc surface, so that
the detected RF signals (A, B, C, D) can be maximized.
Focus Servo is based on focus error (FE) signal which is generated from focus error detection block in
CXA2551R (IC401) using Astigmatism Method. Focus gain and path can be changed at the CXA2551R
according to the disc, and the resulting output (FE) is input to Servo IC (IC201, OTI-9790).
FE signal after first amplification in OTI-9790 is A/D converted and input to Digital Equalizer Block, most
important part at the Focus Servo. At the Digital Equalizer, adjustments for Focus Bias and Loop Gain are
performed.
After D/A converted, Focus servo signal is output through FAO port (OTI-9790, Pin 207) and drive Focus
Actuator through the Focus Drive IC (IC501, BA5983FM).
3-3. Tracking Servo
The aim of Tracking Servo is to make laser beam trace the data track on disc. Tracking Error (TE) signal
is generated from tracking error detection block in CXA2551R (IC401) using DPP (Differential Push-Pull)
Method. DPP method uses not only main beam (A, B, C, D) but side beams (E,F and G, H) for correcting
DC offset generated in Push-Pull method.
The remaining procedures of TE signal processing in OTI-9790 is similar to Focus Servo.
After D/A converted, Tracking servo signal is output through TAO port (OTI-9790, Pin 208) and drive
Tracking Actuator through the Tracking Drive IC (IC501, BA5983FM).
3-4. Sled Servo
The working distance of tracking actuator is too short to cover whole disc radius. Sled Servo make PU
move by little and little so that the laser beam keep tracing the data track on disc continuously when
tracking actuator reaches the working limit.
Another function of Sled Servo is to seek a target point on disc, following user commands.
Sled error signal is generated with accumulated tracking error signal (that is DC value of TE), which is
input to Servo IC (OTI-9790, Pin 198).
After compensation in OTI-9790, Sled servo signal is output through SLO (OTI-9790, Pin 3) and drive Sled
Motor via IC501.
Another sled control signal, SLEDMOVE from U-COM (IC301), is used in the seek mode for data access.
SLEDMOVE signal is compared with feedback speed signal via Hall sensor and speed detection
IC502(BA5925FV) so that the sled movement speed can be controlled accurately, and it is possible to
seek data access point very fast.
29