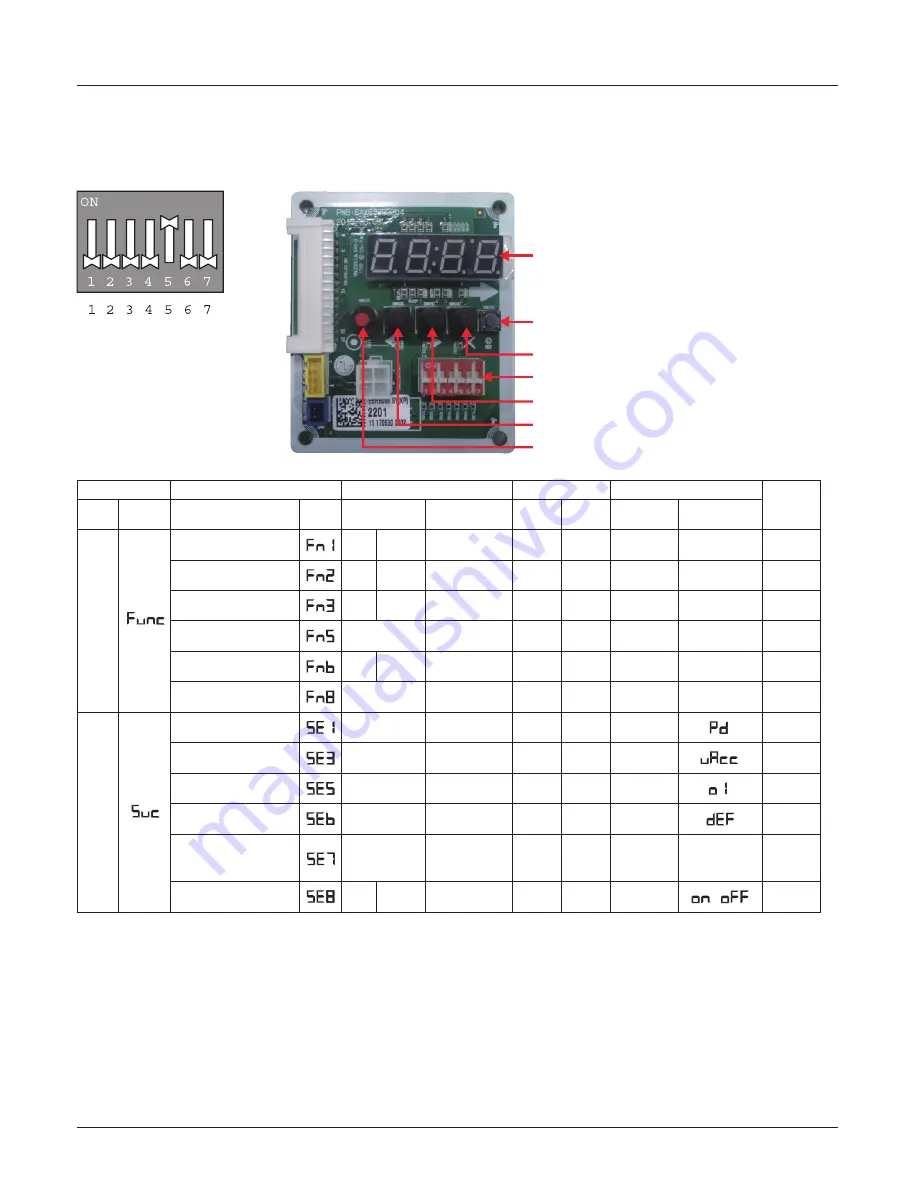
- 25 -
Copyright © 2018 LG Electronics Inc. All rights reserved.
Only training and service purposes.
Function
n
Setting the function
Select the mode/function/option/value using ‘
▶
’, ‘
◀
’ Button and confirm that using the ‘
●
’ button after dip
switch No.5 is turned on.
SW04C (X : cancel)
SW03C (
ȯ
: forward)
DIP-SW01
7 - Segment
SW02C (
ȭ
: backward)
SW01C (
Ɨ
: confirm)
SW01D (reset)
MODE
FUNCTION
OPTION
VALUE
ACTION
Remarks
Content Display1
Content
Display2
Content
Display3
Content Display4 Implement
Display5
Install
ation
Cool & Heat Selector
oFF op1~op2
selected the
option
- -
change the
set value
blank
save in
EEPROM
Static pressure com-
pensation
oFF op1~op3
selected the
option
- -
change the
set value
blank
save in
EEPROM
Night low noise
oFF op1~op15
selected the
option
- -
change the
set value
blank
save in
EEPROM
ODU address
- -
0~254
set the
value
change the
set value
blank
save in
EEPROM
Snow removal & rapid
defrost
oFF op1~op3
selected the
option
- -
change the
set value
blank
save in
EEPROM
Target pressure
adjusting
op1~op6
selected the
option
- -
change the
set value
blank
save in
EEPROM
SVC
Pump Down
- -
-
-
start opera-
tion
-
Vacuum mode
- -
-
-
start opera-
tion
-
Forced oil return
- -
-
-
start opera-
tion
-
Forced defrost
- -
-
-
start opera-
tion
-
Cycle data view
-
-
-
-
Show in
segment
Show the each
numerical value
in process
-
Refrigerant noise
reduction mode
oFF
on
-
-
-
Change the
set value
save in
EEPROM
* Functions save in EEPROM will be kept continuously, though the system power was reset.