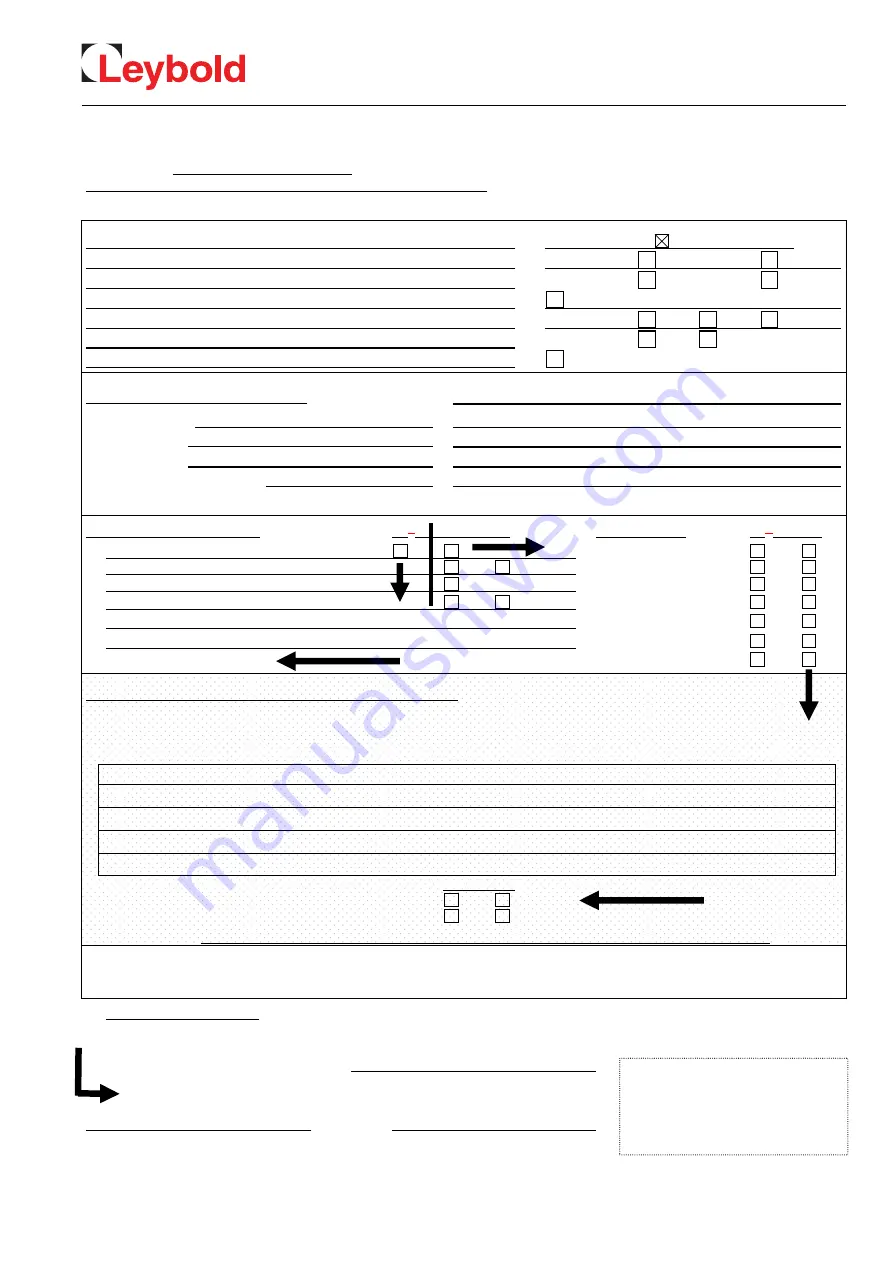
Index
51
GA03108_002_C1 - 04/2018 - © Leybold
Declaration of Contamination
17200001_002_C0
© Leybold
Declaration of Contamination of Compressors, Vacuum Pumps and Components
The repair and / or servicing of compressors, va cuum pumps and components will be carried out only if a correctly completed declaration has
been submitted. Non-completion will result in delay. The manufacturer can refuse to accept any equipment without a declaration.
A separate declaration has to be completed for each single component.
This declaration may be completed and signed only by authorized and qualified staff.
Customer/Dep./Institute
:
Reason for return: applicable please mark
Address :
Repair:
chargeable
warranty
Exchange:
chargeable
warranty
Exchange already arranged / received
Person to contact:
Return only:
rent
loan
for credit
Phone :
Fax:
Calibration:
DKD
Factory-calibr.
End user:
Quality test certificate DIN 55350-18-4.2.1
A. Description of the Leybold product:
Failure description:
Material description :
Catalog number:
Additional parts:
Serial number:
Application-Tool:
Type of oil (ForeVacuum-Pumps) :
Application- Process:
B. Condition of the equipment
No
1)
Yes
No
Contamination :
No
1)
Yes
1
1
.
. Has the equipment been used
toxic
2. Drained (Product/service fluid)
corrosive
3. All openings sealed airtight
flammable
4. Purged
explosive
2)
If yes, which cleaning agent
radioactive
2)
and which method of cleaning
microbiological
2)
1)
If answered with “No”, go to D.
other harmful substances
C. Description of processed substances (Please fill in absolutely)
1. What substances have come into contact with the equipment ?
Trade name and / or chemical term of service fluids and substances processed, properties of the substances
According to safety data sheet (e.g. toxic, inflammable, corrosive, radioactive)
X
Tradename:
Chemical name:
a)
b)
c)
d)
No
Yes
2. Are these substances harmful ?
3. Dangerous decomposition products when heated ?
If yes, which ?
2)
Components contaminated by microbiological, explosive or radioactive products/substances will not be accepted without written
evidence of decontamination.
D. Legally binding declaration
I / we hereby declare that the information supplied on this form is accurate and sufficient to judge any contamination level.
Name of authorized person (block letters) :
Date
signature of authorized person
firm stamp