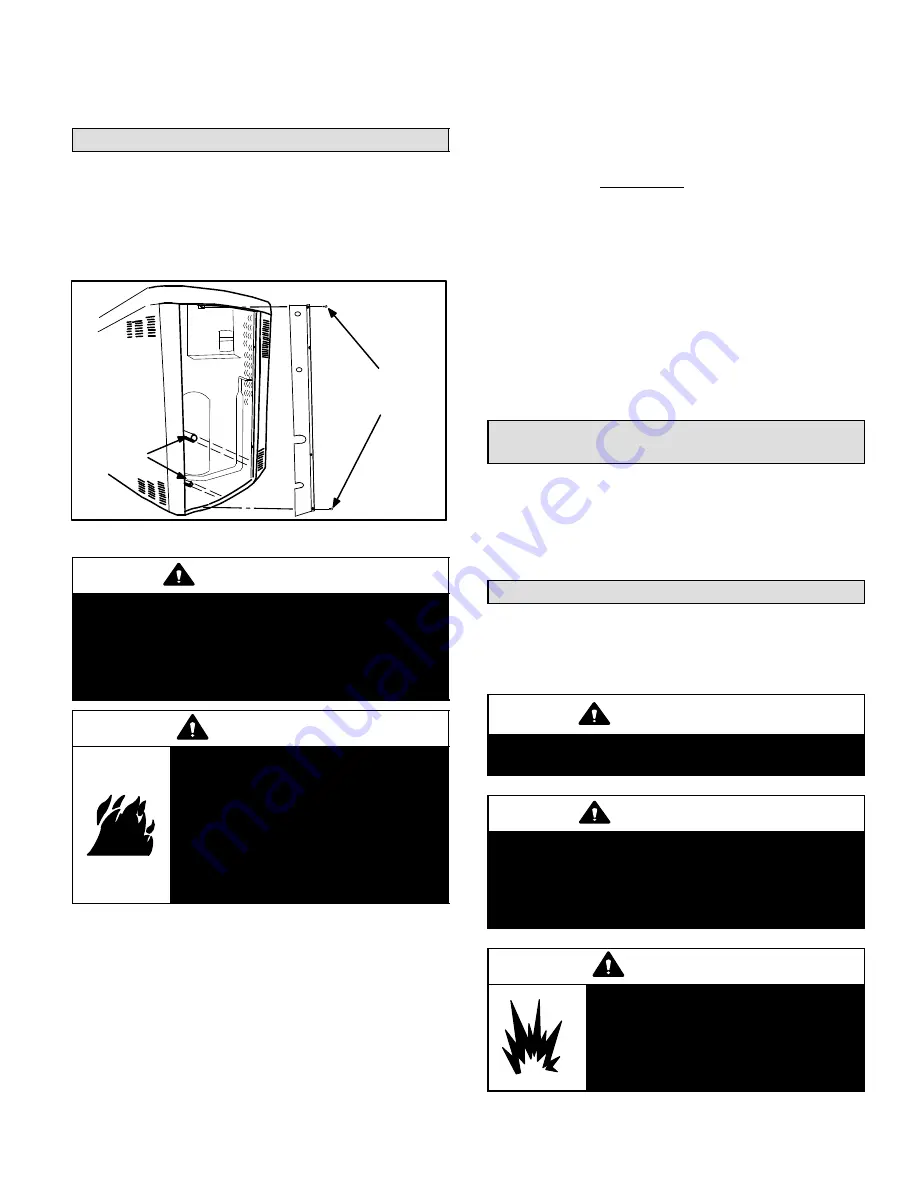
Page 11
XP15 SERIES
ISOLATION GROMMETS
Locate the provided isolation grommets. Slide grommets
onto vapor and liquid lines. Insert grommets into mullion to
isolate refrigerant lines from sheet metal edges.
Brazing Line Set Connections
Use the following procedure to braze the line set to the new
outdoor unit. Figure 19 is provided as a general guide for
preparing to braze the line sets to the outdoor unit.
Before brazing, remove the access panel as illustrated in
figure 11; then remove the narrow piping panel to prevent
burning off the paint as illustrated in figure 20.
REMOVE TWO SCREWS
AND REMOVE PANEL
BEFORE BRAZING.
PIPING
PANEL
LINE SET
CONNECTION
POINTS.
Figure 20. Piping Panel Removal
WARNING
Polyol ester (POE) oils used with HFC−410A
refrigerant absorb moisture very quickly. It is very
important that the refrigerant system be kept
closed as much as possible. DO NOT remove line
set caps or service valve stub caps until you are
ready to make connections.
WARNING
Danger of fire. Bleeding the
refrigerant charge from only the high
side may result in the low side shell
and suction tubing being
pressurized. Application of a brazing
torch while pressurized may result in
ignition of the refrigerant and oil
mixture − check the high and low
pressures before unbrazing.
1. Cut ends of the refrigerant lines square (free from
nicks or dents). Debur the ends. The pipe must remain
round, do not pinch end of the line.
2. Remove service cap and core from both the vapor and
liquid line service ports.
3. Connect gauge low pressure side to liquid line service
valve.
4. To protect components during brazing, wrap a wet
cloth around the liquid line service valve body and
copper tube stub and use another wet cloth
underneath the valve body to protect the base paint.
Also, shield the light maroon R−410A sticker.
5. Flow regulated nitrogen (at 1 to 2 psig) through the
refrigeration gauge set into the valve stem port
connection on the liquid line service valve and out of
the valve stem port connection on the vapor service
valve. The CTXV metering device at the indoor unit
coil will allow low pressure nitrogen to flow through the
system.)
Note: Use silver alloy brazing rods with five or six percent
minimum silver alloy for copper−to−copper brazing or 45
percent silver alloy for copper−to−brass or copper−to−steel
brazing.
6. Braze the line set to the liquid line service valve. Turn
off nitrogen flow. Repeat procedure starting at
paragraph 4 for brazing the vapor line set to service
valve.
After brazing the vapor line set to the service valve,
disconnect gauge from service port, remove wrapping and
replace service port cores.
Removing Existing Refrigerant Metering
Device
Remove the existing HCFC−22 refrigerant flow control
orifice or thermal expansion valve from the indoor coil.
Existing devices are not approved for use with HFC−410A
refrigerant and may prevent proper flushing. Use a
field−provided fitting to reconnect lines. See figure 23 on
page 13 for disassembly and typical removal instructions.
Testing for Leaks
After the line set has been connected to both the indoor
and outdoor units, check the line set connections at both
the indoor and outdoor units unit for leaks. Use the
following procedure to test for leaks:
IMPORTANT
Leak detector must be capable of sensing HFC
refrigerant.
WARNING
Refrigerant can be harmful if it is inhaled.
Refrigerant must be used and recovered
responsibly.
Failure to follow this warning may result in personal
injury or death.
WARNING
When using a high pressure gas such
as dry nitrogen to pressurize a
refrigeration or air conditioning
system, use a regulator that can
control the pressure down to 1 or 2
psig (6.9 to 13.8 kPa).