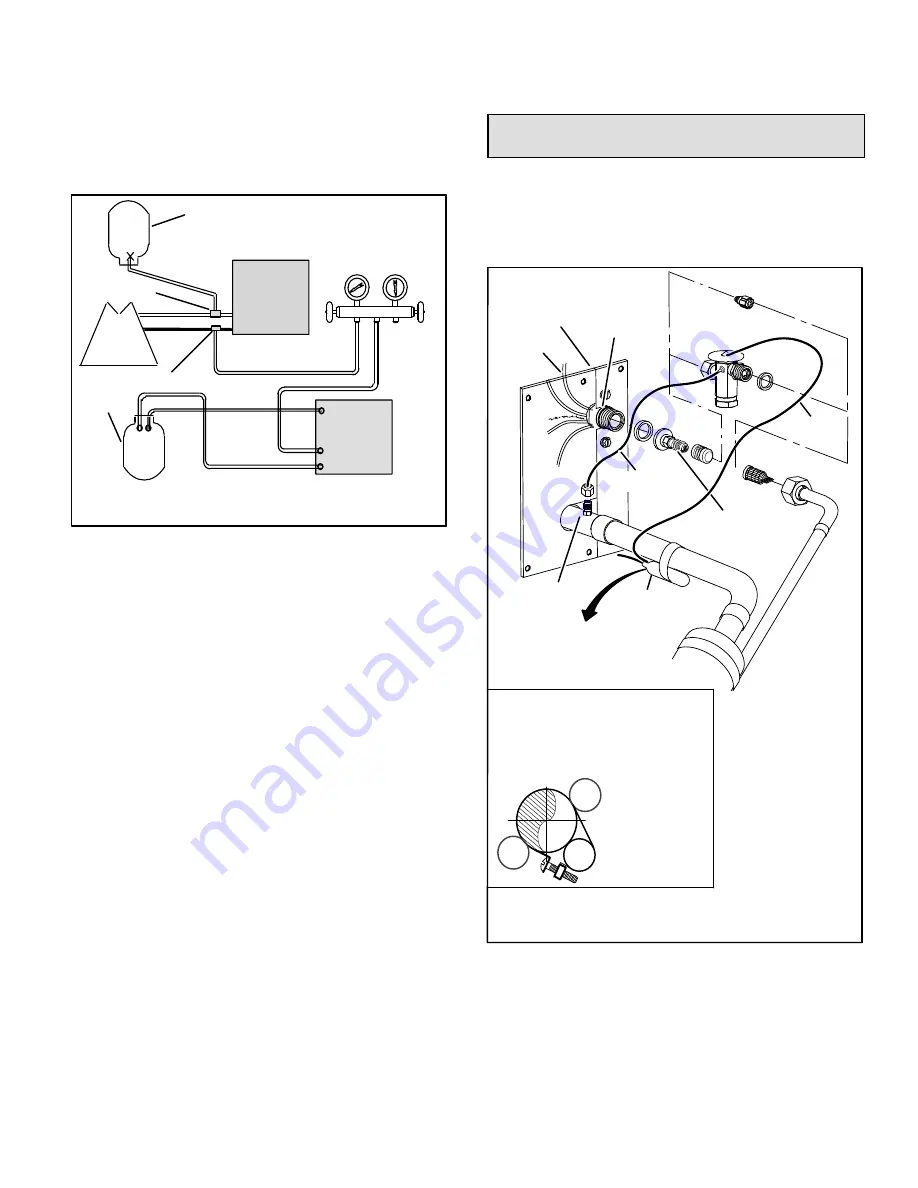
Page 13
XP15 SERIES
REQUIRED EQUIPMENT
Equipment required to flush the existing line set and indoor
unit coil:
S
Two clean HCFC−22 recovery bottles,
S
Oilless recovery machine with pump-down feature,
S
Two gauge sets (one for HCFC−22; one for
HFC−410A).
LOW
PRESSURE
HIGH
PRESSURE
EXISTING
INDOOR
UNIT
GAUGE
MANIFOLD
INVERTED HCFC−22 CYLINDER
CONTAINS CLEAN HCFC−22 TO
BE USED FOR FLUSHING.
LIQUID LINE SERVICE VALVE
INLET
DISCHARGE
TANK
RETURN
CLOSED
OPENED
RECOVERY
CYLINDER
NOTE − The inverted HCFC−22 cylinder must contain at least the same
amount of refrigerant as was recovered from the existing system.
RECOVERY MACHINE
NEW
OUTDOOR
UNIT
SUCTION LINE
SERVICE VALVE
SUCTION
LIQUID
Figure 22. Typical Flushing Connection
PROCEDURE
1. Verify that the existing HCFC−22 refrigerant flow
control device has been removed before continuing
with flushing procedures. Existing devices are not
approved for use with HFC−410A refrigerant and may
prevent proper flushing.
2. Connect an HCFC−22 cylinder with clean refrigerant to
the vapor service valve. Connect the HCFC−22 gauge
set to the liquid line valve. Connect a recovery
machine with an empty recovery tank to the gauge set
as illustrated in figure 22.
3. Set the recovery machine for liquid recovery and start
the recovery machine. Open the gauge set valves to
allow the recovery machine to pull a vacuum on the
existing system line set and indoor unit coil.
4. Invert the cylinder of clean HCFC−22 and open its
valve to allow liquid refrigerant to flow into the system
through the vapor line valve. Allow the refrigerant to
pass from the cylinder and through the line set and the
indoor unit coil before it enters the recovery machine.
5. After all of the liquid refrigerant has been recovered,
switch the recovery machine to vapor recovery so that
all of the HCFC−22 vapor is recovered. Allow the
recovery machine to pull a vacuum on the system.
NOTE − A single system flush should remove all of the
mineral oil from the existing refrigerant lines and indoor
unit coil. A second flushing may be done (using clean
refrigerant) if insufficient amounts of mineral oil were
removed during the first flush.
Each time the system is
flushed, you must allow the recovery machine to pull a
vacuum on the system at the end of the procedure.
6. Close the valve on the inverted HCFC−22 drum and
the gauge set valves. Pump the remaining refrigerant
out of the recovery machine and turn the machine off.
Installing New Refrigerant Metering
Device
XP15 units are used in check thermal expansion valve
(CTXV) systems only. See the indoor unit coil installation
instructions and the Lennox Engineering Handbook for
approved CTXV match−ups and application information.
Table 3 on page 9 lists liquid and vapor line sizes and
corresponding line sets.
NOTE − If necessary, remove HCFC−22 flow control device (fixed
orifice/check expansion valve) from existing line set before instal-
ling HFC−410A approved expansion valve and o−ring.
REMOVE AND DISCARD
SEAL ASSEMBLY (IF
APPLICABLE)
TWO PIECE PATCH
PLATE(UNCASED
COIL ONLY)
VAPOR
LINE
ORIFICE
HOUSING
DISTRIBUTOR
TUBES
LIQUID
LINE
SENSING BULB
(INSULATION REQUIRED)
ACCESS FITTING
(NO VALVE CORE)
SENSING
LINE
EQUALIZER
LINE
ORIFICE
OR
EXPANSION VALVE
(SEE NOTE)
O−RING
STRAINER
(Uncased Coil Shown)
On smaller vapor lines, bulb may be
mounted on top or side-mounted (prefer-
ably at 3 o’clock position).
On 5/8" and larger lines, mount bulb
approximately at the 4 or 8 o’clock posi-
tions; never mount on bottom of line.
12
3 o’clock
9
VAPOR-
Line
Bulb
O−RING
Figure 23. Typical Metering Device Installation
The thermostatic expansion valve or check / thermostatic
expansion valve, can be installed internal or external to the
indoor coil. In applications where an uncased coil is being
installed in a field provided plenum, install the CTXV and
provide an access for field servicing of the CTXV. Refer to
Figure 23 for reference during installation of CTXV.
1. On fully cased coils, remove the coil access and
plumbing panels.