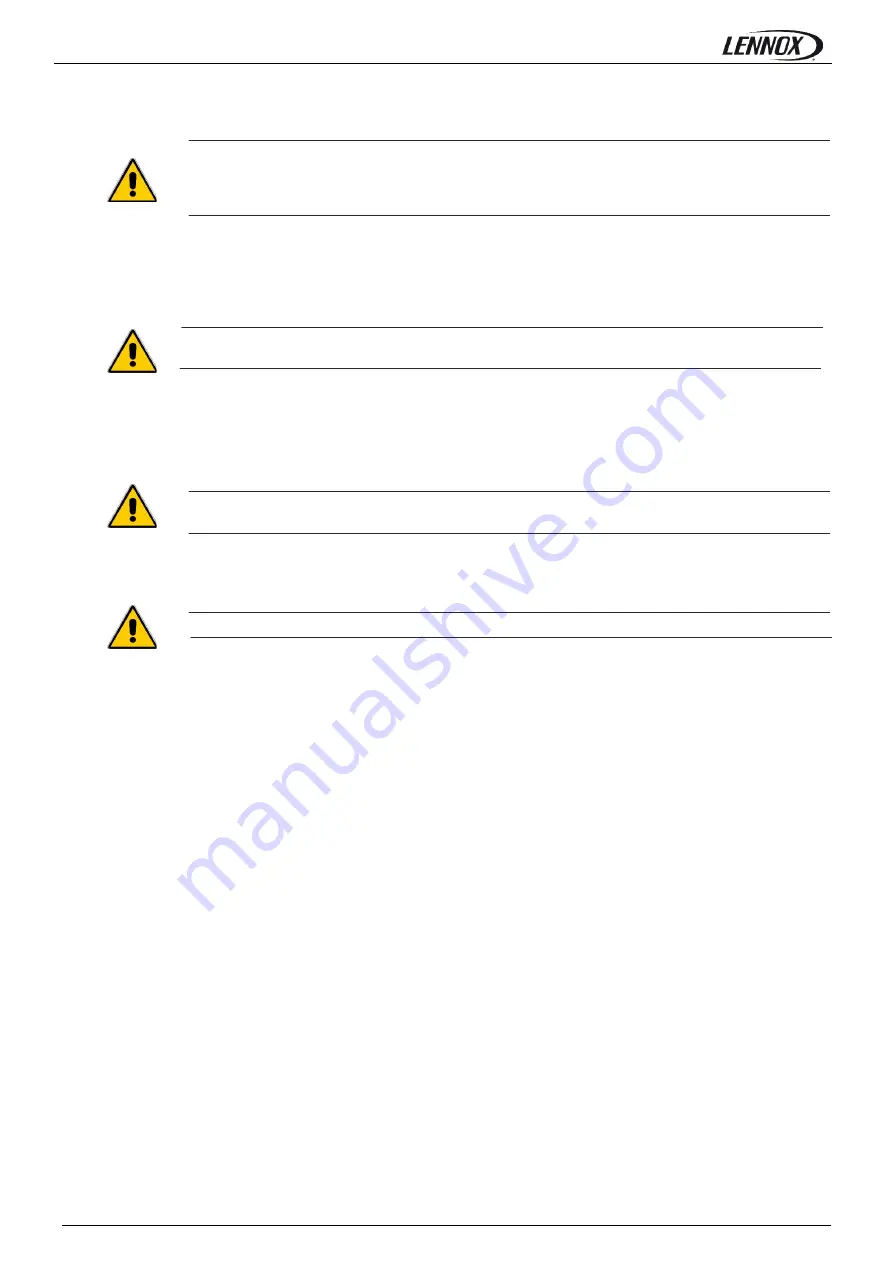
INNOV@ ECFAN DMR -AGU-0912-E
•
19
•
9.5 Repairing the cooling circuit
Warning:
While performing repairs on the cooling circuit or maintenance work on the compressor
make sure the circuit is left open for as little time as possible. Even if briefly exposed to
air, ester oils tend to absorb large amounts of humidity, which results in the formation of
weak acids.
If the cooling circuit has undergone any repairs, the following operations must be carried out:
D
tightness test;
D
evacuation and drying of the cooling circuit;
D
charging with refrigerant.
If the system has to be drained, always recover the refrigerant present in the circuit using suitable
equipment; the refrigerant should be handled exclusively in the liquid phase.
9.6 Tightness test
Fill the circuit with anhydrous nitrogen supplied from a tank with a pressure-reducing valve until the pressure rises to 20
bars.
During the pressurisation phase, do not exceed a pressure of 22 bars on the compressor low pressure
side.
The presence of any leaks must be determined using special leak detectors. Should any leaks be detected during the
test, empty out the circuit before repairing the leaks with suitable alloys.
Do not use oxygen in the place of nitrogen as a test agent, since this would cause a risk of explosion.
9.7 Hard vacuum and drying of cooling circuit
To achieve a hard vacuum in the cooling circuit it is necessary to use a pump capable of generating a high degree of
vacuum, i.e. 150 Pa of absolute pressure with a capacity of approximately 10 m
3
/h. If such a pump is available, one
evacuation
will
normally
suffice
to
achieve
an
absolute
pressure
of
150
Pa.
If there is no such vacuum pump available, or whenever the circuit has remained open for long periods of time, you are
strongly recommended to adopt the triple evacuation method. This method is also recommended when there is a
presence of humidity within the circuit. The vacuum pump should be connected to the inlets.
The procedure to be carried out is as follows:
D
Evacuate the circuit until you reach an absolute pressure of at least 350 Pa: at this point inject nitrogen into the
circuit until you reach a relative pressure of about 1 bar.
D
Repeat the step described above.
D
Carry out the step described above for the third time, but in this case attempting to reach the hardest vacuum
possible.
Using this procedure you can easily remove up to 99% of pollutants.
9.8 Recharging with refrigerant R407C
D
Connect the tank of refrigerant gas to the male 1/4 SAE inlet situated on the liquid line after discharging a little gas to
eliminate air in the connection pipe.
D
Fill with refrigerant in liquid form until you reach 75% of the total charge.
D
Then connect to the inlet on the pipe between the thermostatic valve and evaporator and complete the charging
process with the refrigerant in liquid form until no more bubbles can be seen on the liquid level indicator and the
operating parameters specified in section 8 have been reached.
Содержание INNOV DM R Series
Страница 2: ......
Страница 32: ......
Страница 49: ...INNOV ECFAN DHR AGU 0912 E 17 6 Operating Diagrams DISPLACEMENT DOWNFLOW UPFLOW...
Страница 75: ...lennoxemeia com INNOV DM_C APPLICATION GUIDE Centrifugal close control unit 6 22 kW INNOVA CENT AGU 0912 E...
Страница 76: ......