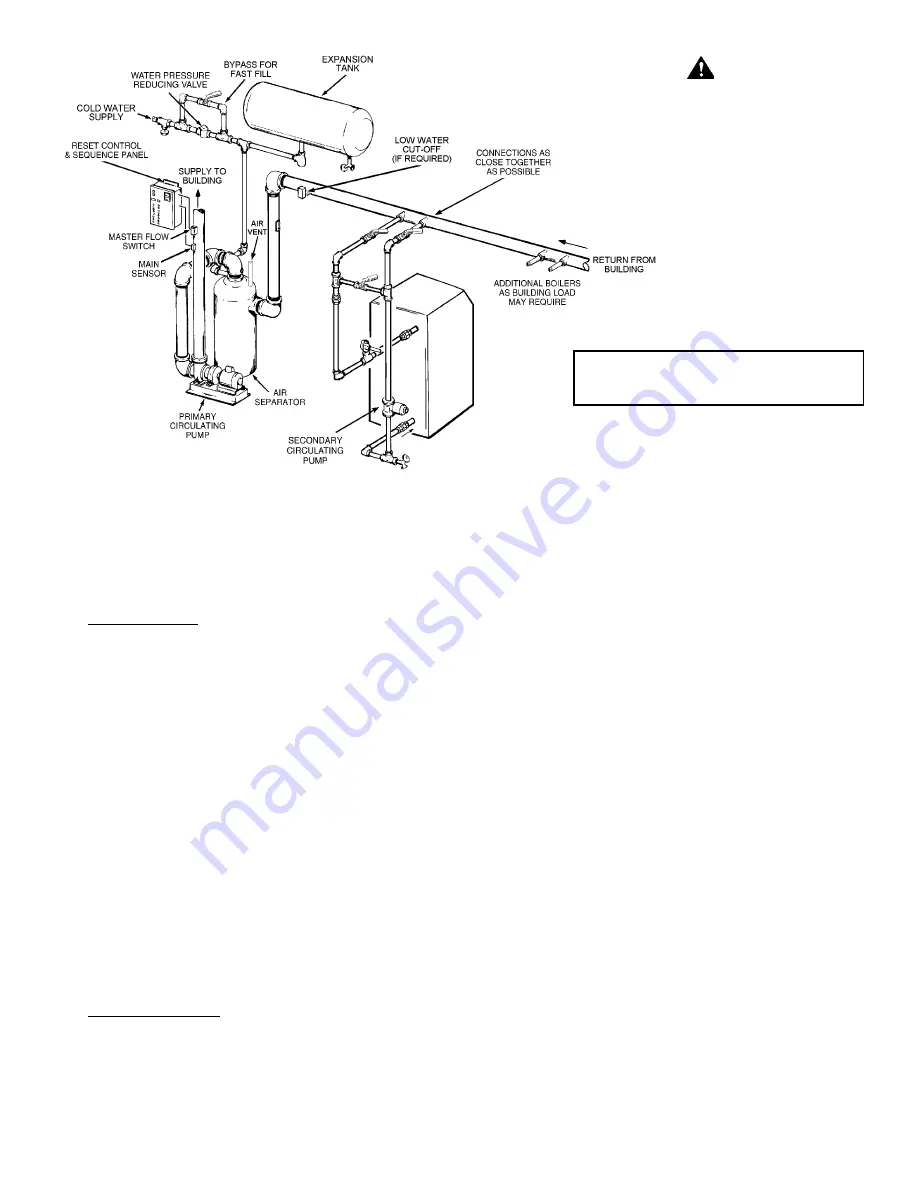
17
Manifold headers are recommended for split systems with or
without zone values and also those installations with zone
circulators. If the system is to be split at remote points, good
practice requires special attention be given to main pipe sizing
to allow balancing of water flow.
5. COOLING PIPING
When the boiler is used in conjunction with a refrigeration
system it must be installed so that the chilled medium is piped
in parallel with the boiler. Appropriate flow control valves,
manual or motorized, must be provided to prevent the chilled
medium from entering the boiler.
Water temperature in the heating system must be reduced to
less than 100°F (38°C) before cooling system is started, or
damage to the chiller unit may occur.
If the boiler is connected to chilled water piping or its heating
coils are exposed to refrigerated air, the boiler piping system
must be equipped with flow valves or other automatic means
to prevent gravity circulation through the boiler during the
cooling cycle.
Primary/secondary pumping of both the chiller(s) and the
boiler(s) is an excellent winter-summer change-over method,
because cooling flow rates are so much more than heating
flow rates. In this way each system (heating or cooling) is
circulated independently.
6. CIRCULATING PUMP
FOR HOT WATER HEATING SYSTEMS - LB MODELS
, the
circulating pump is NOT provided and must be field-installed.
NOTE: If a system pump is to be installed on a Legend LB
model, the maximum rating of the pump motor must not
exceed 1 hp.
INTERNAL CONTAMINANTS
The hydronic system must be internally cleaned and flushed after
a new or replacement boiler has been installed, to remove
contaminants that may have accumulated during installation. This
is doubly important when a replacement boiler is installed into
an existing system where Stop Leak or other boiler additives
have been used.
Failure to clean and flush the system can produce acid
concentrations that become corrosive, cause gases to form that
block water circulation or lead to formation of deposits on the
boiler surfaces, any of which could result in damage to the system
and circulator.
All hot water heating systems should be completely flushed with
a grease removing solution to assure trouble-free operation. Pipe
joint compounds, soldering paste, grease on tubing and pipe all
tend to contaminate a system
Failure to flush contaminants from a system can cause solids to
form on the inside of boiler exchangers, create excessive amounts
of air and other gases to block circulation, foul various system
accessories and even deteriorate circulation seals and impellers.
HOT WATER SUPPLY BOILER SYSTEM-
GENERAL WATER LINE CONNECTIONS
This section provides detailed installation diagrams for a typical
method of application for the unit.
Piping diagrams will serve to provide the installer with a reference
for the materials and methods of piping necessary for installation.
It is essential that all water piping be installed and connected as
shown on the diagrams. Check the diagrams to be used
thoroughly before starting installation to avoid possible errors
and to minimize time and material cost.
It is essential that all water piping be installed and connected as
shown on the diagrams. Check the diagrams to be used
thoroughly before starting installation to avoid possible errors
and to minimize the time and material cost.
FIGURE 12. TYPICAL PRIMARY, SECONDARY PIPING
• INSTALL IN ACCORDANCE WITH ALL LOCAL CODES.
• WHEN BLOW DOWN VALVE IS REQUIRED, INSTALL
IN PLACE OF THE DRAIN VALVE SHOWN.
DANGER
TEMPERATURE SETTING SHOULD NOT EXCEED
SAFE USE TEMPERATURE AT FIXTURES. SEE
WATER TEMPERATURE CONTROL WARNING ON
PAGE 28. IF HIGHER PREHEAT TEMPERATURES
ARE NECESSARY TO OBTAIN ADEQUATE
BOOSTER OUTPUT, ADD AN ANTI-SCALD VALVE
FOR HOT WATER SUPPLIED TO FIXTURES.
Содержание LB 1000
Страница 22: ...22 FIGURE 16 CONNECTION DIAGRAM ...
Страница 23: ...23 FIGURE 17 SCHEMATIC DIAGRAM ...