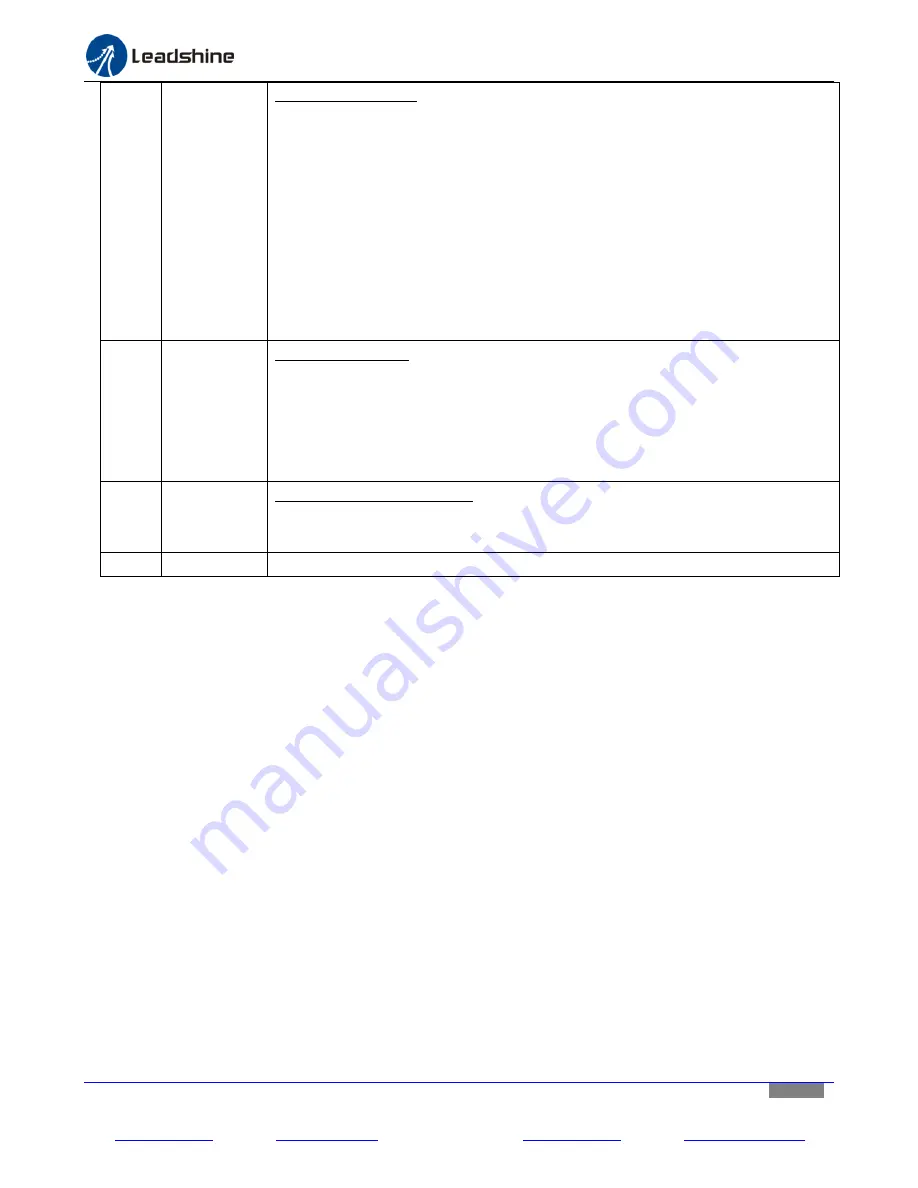
Hardware
installation manual of the multi-axis drive MX3660
Leadshine Technology Co., Ltd
Leadshine America, Inc.
Page 21/25
11/F, Block A3, iPark,
No.1001 Xueyuan Blvd, Nanshan District, Shenzhen, China
25 Mauchly, Suite 318, Irvine, CA 92618, USA
Tel:
86-755-26409254
Fax: 86-755-26402718
Tel: 1-949-608-7270
Fax: 1-949-608-7298
Web
:
www.leadshine.com
Email:
Web:
www.leadshine.com
Email:
15
FAULT
Fault signal output. The fault pin connection is optional. Pin 15 is a
Pull-Down-Connection.
TTL level high: Fault
TTL level low: No fault.
TTL level high will be in one of the following scenario:
•
Any of the 3 stepper drive module is in protection mode including over voltage and
over current. Read “Protection” detail in the MX3660 datasheet.
•
The connected external E-Stop switch in the digital input is pressed.
With the receiving of a fault from the MX3660, a controller can be notified an
abnormal event has happened. It can then react, such as shutting down the whole
control machine/device for machine damage.
16
CHARGE
PUMP
General digital input. A watchdog timer to enable/disable the MX3660. When “Pulse
Switch” (Figure 3) is set to “OFF” position (Charge pump feature not turned off), the
MX3660 will be only enabled with 10 KHz signal receiving at this PIN. Otherwise (no
such signal received), the MX3660 will be disabled. For example, in Mach3 controlled
CNC applications, the MX3660’s enabling/disabling will depend on the receiving of
“Charge Pump” signal from Mach 3.
17
INPUT 1
General purpose digital input. It is connected to “Output 1” of the digital output
connector (CN7 on Figure 3). Used to forward an input signal sent from the connected
motion controller to the device connected at “Output 1”.
18-25
GND
Ground