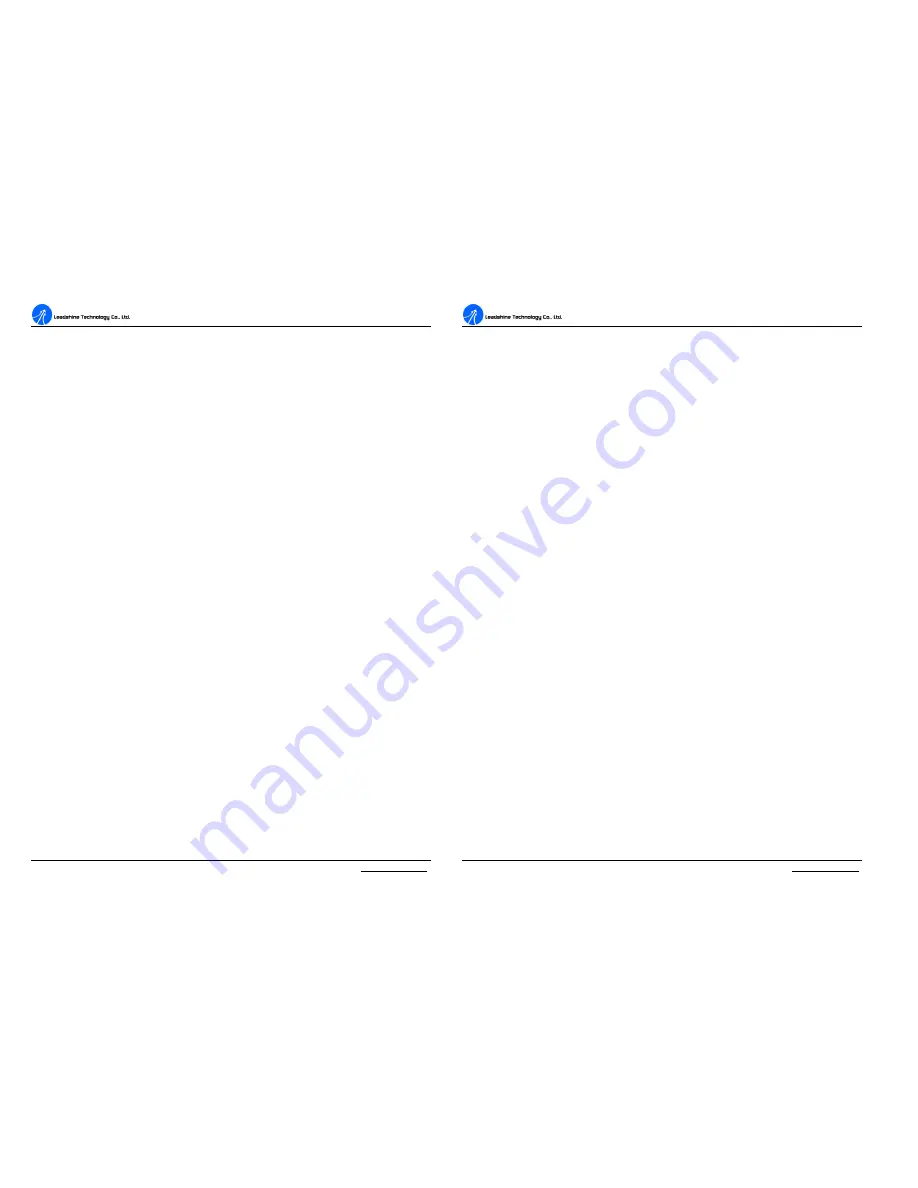
A
A
C
C
S
S
6
6
0
0
6
6
D
D
i
i
g
g
i
i
t
t
a
a
l
l
A
A
C
C
S
S
e
e
r
r
v
v
o
o
d
d
r
r
i
i
v
v
e
e
M
M
a
a
n
n
u
u
a
a
l
l
R
R
e
e
v
v
1
1
.
.
0
0
Tel: (86)755-26434369
12
Website: www.leadshine.com
Cable Routing
All content sensitive signal wires should be routed as far away from motor power
wires and Drive power wires as possible. Motor power and Drive power wires are
major sources of noise and can easily corrupt a nearby signal. This issue becomes
increasingly important with longer motor power and Drive power wires lengths.
Twisted Wires
Twisted wires effectively increasing noise immunity. The successive twists eliminate
noise transients along the length of the cable. Both signal cables and power cables
should be of the twisted and shielded type. Differential signal wires should be twisted
as a pair. The combination of twisted pair wires and a differential signal significantly
adds to noise immunity. Power wires should be twisted as a group along with the
ground (or chassis) wire, if available.
Cable Shielding
All signal wires should be bundled and shielded separately from Drive power and
motor power wires. Power wires should also be bundled and shielded. When
grounding a shield, the rule-of-thumb is to do so at the
‘
source
’
of power while
leaving the other shield end open. For example, in the case of motor power wires, this
would be the drive side. Ideally, twisted pairs should be individually shielded and
isolated from the outer shield, which encompasses all wires within the cable. However,
since this type of stringent shielding practice is often not required, typical cables do
not provide isolation between inner and outer shields.
System Grounding
Good grounding practices help reduce the majority of noise present in a system. All
common grounds within an isolated system should be tied to PE (protective earth)
through a
‘
SINGLE
’
low resistance point. Avoiding repetitive links to PE creating
ground loops, which is a frequent source of noise. Central point grounding should also
A
A
C
C
S
S
6
6
0
0
6
6
D
D
i
i
g
g
i
i
t
t
a
a
l
l
A
A
C
C
S
S
e
e
r
r
v
v
o
o
d
d
r
r
i
i
v
v
e
e
M
M
a
a
n
n
u
u
a
a
l
l
R
R
e
e
v
v
1
1
.
.
0
0
Tel: (86)755-26434369
13
Website: www.leadshine.com
be applied to cable shielding; shields should be open on one end and grounded on the
other. Close attention should also be given to chassis wires. For example, motors are
typically supplied with a chassis wire. If this chassis wire is connected to PE, but the
motor chassis itself is attached to the machine frame, which is also connected to PE, a
ground loop will be created. Wires used for grounding should be of a heavy gauge and
as short as possible. Unused wiring should also be grounded when safe to do so since
wires left floating can act as large antennas, which contribute to EMI.
Power Supply Connection
NEVER
connect power and ground in the wrong direction, because it will damage
the ACS606 drive. The distance between the DC power supply of the drive and the
drive itself should be as short as possible since the cable between the two is a source
of noise. When the power supply lines are longer than 50 cm, a 1000
µ
F/100V
electrolytic capacitor should be connected between the terminal
“
GND
”
and the
terminal
“
+VDC
”
. This capacitor stabilizes the voltage supplied to the drive as well
as filters noise on the power supply line.
Please note that the polarity can not be
reversed.
It is recommended to have multiple drives to share one power supply to reduce cost if
the supply has enough capacity. To avoid cross interference,
DO NOT
daisy-chain
the power supply input pins of the drives. Instead, please connect them to power
supply separately.
5. Tuning the Servo
Testing the Servo
You may wish to secure the motor so it can
’
t jump off the bench. Turn on the power
supply, the green (Power) LED will light. The ACS606 has default parameters stored
in the drive. If the system has no hardware and wirings problem, the motor should be
locked and the drive should be ready.