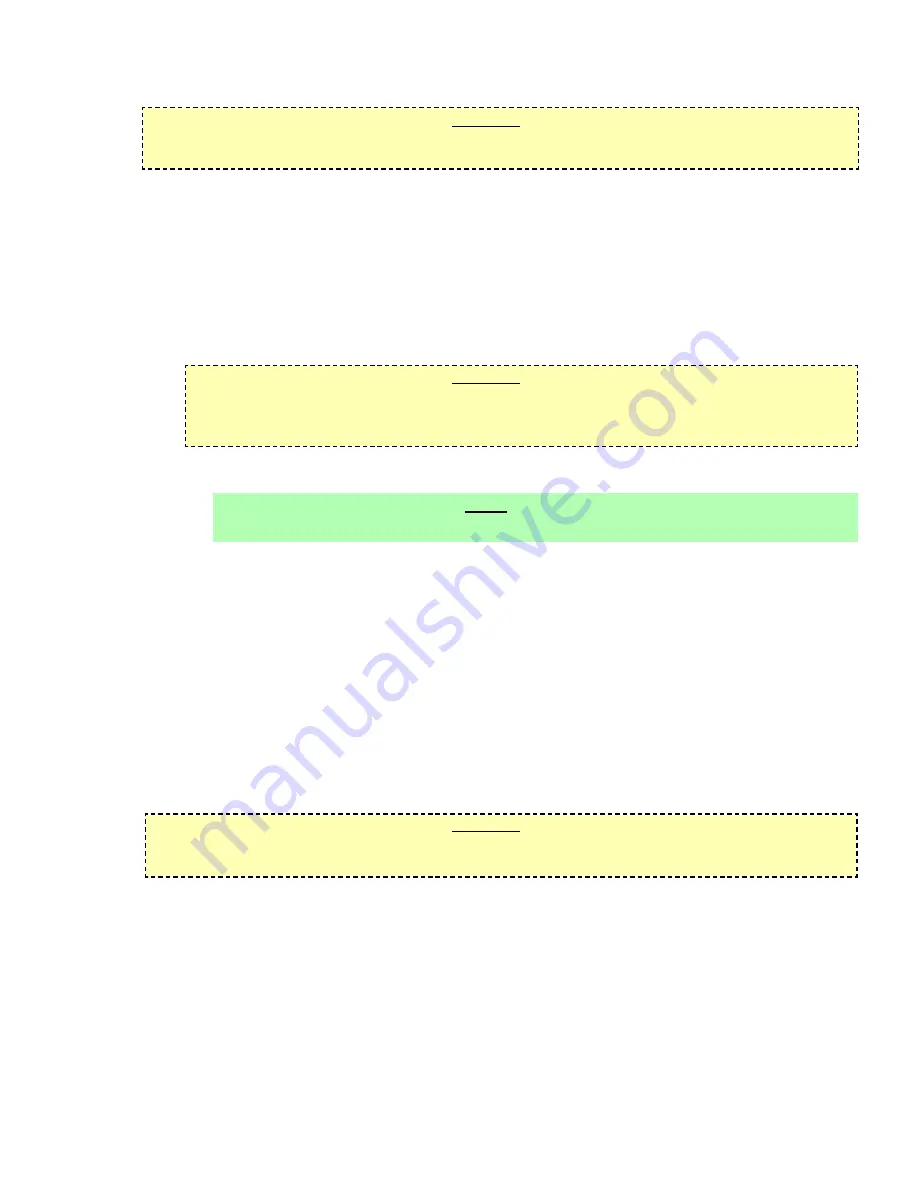
5
2.
SCHEDULED MAINTENANCE
CAUTION
DO NOT USE ANY POWDERS OR ABRASIVE CLEANING COMPOUNDS WHICH CAN DAMAGE THE
FINISH.
2.1
DAILY
A. Remove the nozzle and diffuser from each valve and wash them in warm water.
B. Remove the cup rest and wash in warm soapy water.
C. Pour warm soapy water into the drip tray and wipe with a clean cloth.
D. With a clean cloth and warm soapy water, wipe off all exterior surfaces of the unit.
E. Reinstall the cup rest, valve diffusers and valve nozzles.
2.2
WEEKLY
A. Check the flow and brix of each valve following the brixing instructions given in Sections 1.15
and 1.16.
CAUTION
THE WATER BATH COMPARTMENT MUST BE FILLED WITH WATER BEFORE PLUGGING IN
THE UNIT, OTHERWISE THE COMPRESSOR DECK AND CONDENSER FAN MAY NOT
OPERATE PROPERLY.
B. Remove the unit’s bonnet and check the level of water in the water bath. Replenish as required,
and reinstall the bonnet.
NOTE
Do NOT use distilled water to fill water bath.
2.3
MONTHLY
A. Unplug the dispenser from it’s power source.
B. Remove the bonnet, and clean the dirt from the unit’s condenser using a soft brush.
C. Reinstall the bonnet and plug in the unit.
2.4
EVERY SIX (6) MONTHS
A. Clean and sanitize the unit using the appropriate procedures outlined in Section 3 of this
manual.
2.5
YEARLY
A. Clean water bath interior, including evaporator coils and refrigeration components.
B. Clean the entire exterior of the unit.
C. Sanitize syrup lines.
3.
DISPENSER CLEANING AND SANITIZING
CAUTION
BECAUSE OF DIFFICULTY IN RINSING, DETERGENT SOLUTIONS SHOULD NOT BE INTRODUCED
INTO THE CARBONATOR.
3.1
AMBIENT PROCESS
A. The ambient process is the most common method for cleaning and sanitizing dispenser
equipment. The detergent should be caustic-based and the sanitizer should be a low pH (7.0)
chloride solution.
B. Disconnect syrup containers and remove product from tubing by purging with carbon dioxide.
C. Rinse the lines and fittings with clean room temperature water to remove all traces of residual
product.
D. Fill lines with a caustic-based (low-sudsing, non-perfumed, and easily rinsed) detergent solution.
The solution should be prepared in accordance with the manufacturers recommendations, but
should be at least 2 percent sodium hydroxide. Make sure the lines are completely filled and
allow to stand for at least 10 minutes.