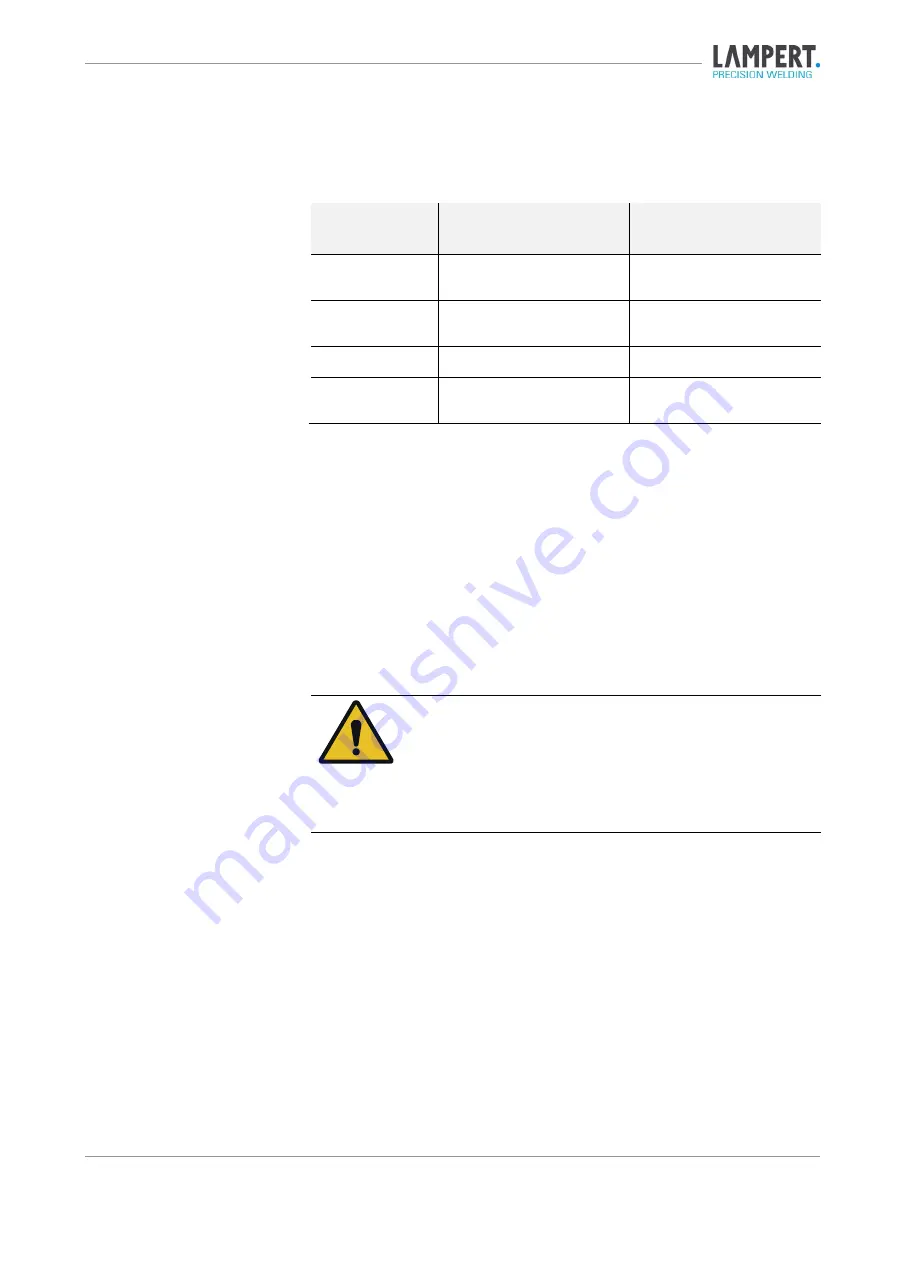
1 About this operating manual
Issue EN 2022/05 PUK 6 Operating manual
8/56
1.3
Structure of the warnings
Signal word
Avoidance of ...
Possible consequences if
the warning is not heeded:
DANGER
Personal injury
(imminent danger)
Death or severe injuries!
WARNING
Personal injury
(potentially hazardous situation)
Death or severe injuries!
CAUTION
Personal injury
Light or minor injuries!
NOTE
Property damage
Damage to the device or its im-
mediate surroundings!
Tab. 1.1 Warning levels
The warnings are structured as follows:
•
Warning sign with signal word in accordance with the warning level
(see Tab 1.1)
•
Type of hazard (description of the hazard)
•
Consequences of the hazard (description of the consequences of the
hazard)
•
Hazard prevention (measures to prevent the hazard)
DANGER!
Type of hazard
Consequences of hazard
Hazard prevention