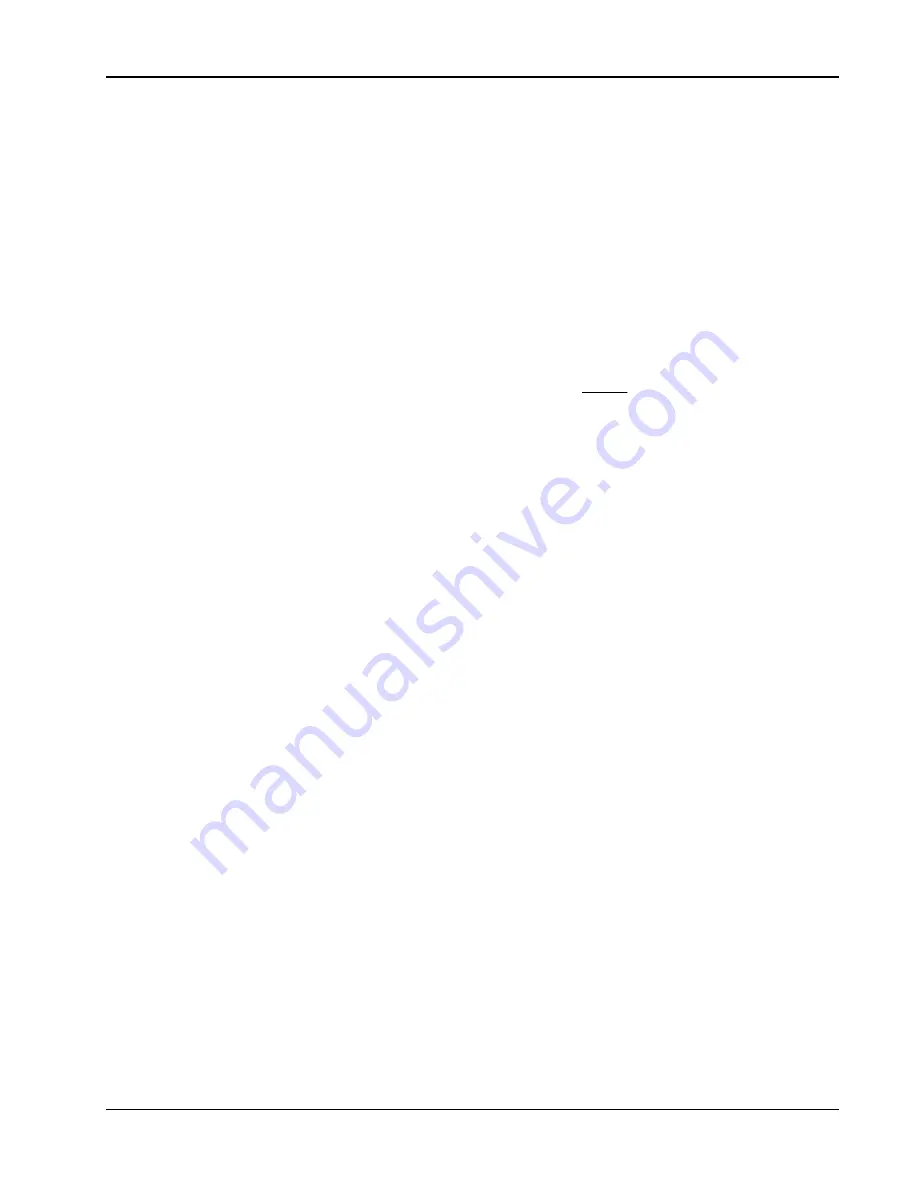
Lake Shore Model 332 Temperature Controller User’s Manual
3.7.4
Loop 1 Heater Output Noise
The heater output circuitry in the Model 332 must be capable of sourcing 50 W of power. This type of
circuitry can generate some electrical noise. The Model 332 was designed to generate as little noise
as possible but even noise that is a small percentage of the output voltage or current can be too
much when sensitive measurements are being made near by. If the Model 332 heater leads are too
noisy and the above wiring techniques do not help, Lake Shore offers the Model 3003 Heater Output
Conditioner that may help. Refer to Paragraph 7.4.
3.7.5
Loop 2 Output
The Model 332 has a second control loop called Loop 2. Loop 2 has a different output than Loop 1.
Loop 2 output is a single range, variable DC voltage source that can vary from 0 V to +10 V. The
output can source up to 1 A of current providing a maximum of 10 W of heater power.
3.7.6
Loop 2 Output Resistance
The power delivered by the Loop 2 output is calculated as:
P
V
R
heater
=
2
The output is rated for no more than 1 A of current. For the maximum of 10 W output power use a
10
Ω
resistive heater with a power rating greater than 10 W. Smaller resistance values should not
be used, but larger resistances can be used for lower power applications.
3.7.7
Loop 2 Output Connector
The connector for the Loop 2 output is on the RELAYS and ANALOG OUTPUT Terminal Block. See
Pins 7 and 8 in Figure 3-5. Twisted pair of 30 gauge or larger wire is recommended.
3.7.8
Loop 2 Heater Protection
The output is short protected so the instrument is not harmed if the heater resistance is too small. It is
not recommended because the additional load on instrument power supplies causes noise on internal
circuits. The second control loop has fewer features than the first including software protection and
limits. The user must be careful to build a robust system and account for the voltage range and power
up state of the control output.
3.7.9
Boosting Output Power
There are temperature control systems that require more power than the Model 332 can provide. An
auxiliary DC power supply can be used to boost the output. Programmable power supplies are
available that use a low current programming voltage as an input to control a high current voltage
output. Loop 2 output provides an ideal programming voltage for an auxiliary power supply.
The only drawback with using the loop 2 output to program auxiliary supplies is it only has one
voltage range. The heater output for Loop 1 has several ranges that can improve resolution, but its
output is in current not voltage. To use Loop 1 to program a larger power supply, a programming
resistor can be placed across the heater output to produce a programming voltage. The programming
voltage is related to output current by:
V
R
I
program
program
output
=
×
The resistor must be chosen to convert a full scale current from the highest heater output range being
used to the full scale programming voltage of the auxiliary supply. For example, if the auxiliary supply
has a full scale programming voltage of 10 V and the maximum current for the highest heater output
range being used is 0.3 A the programming resistor should be 10 V / 0.3 A = 33
Ω
. The programming
resistor must be rated for the power being dissipated in it which is:
Power
I
R
output
program
=
×
2
or 3 W. The “Low” heater output range can be selected to reduce the power dissipated in the
programming resistor.
Installation
3-9