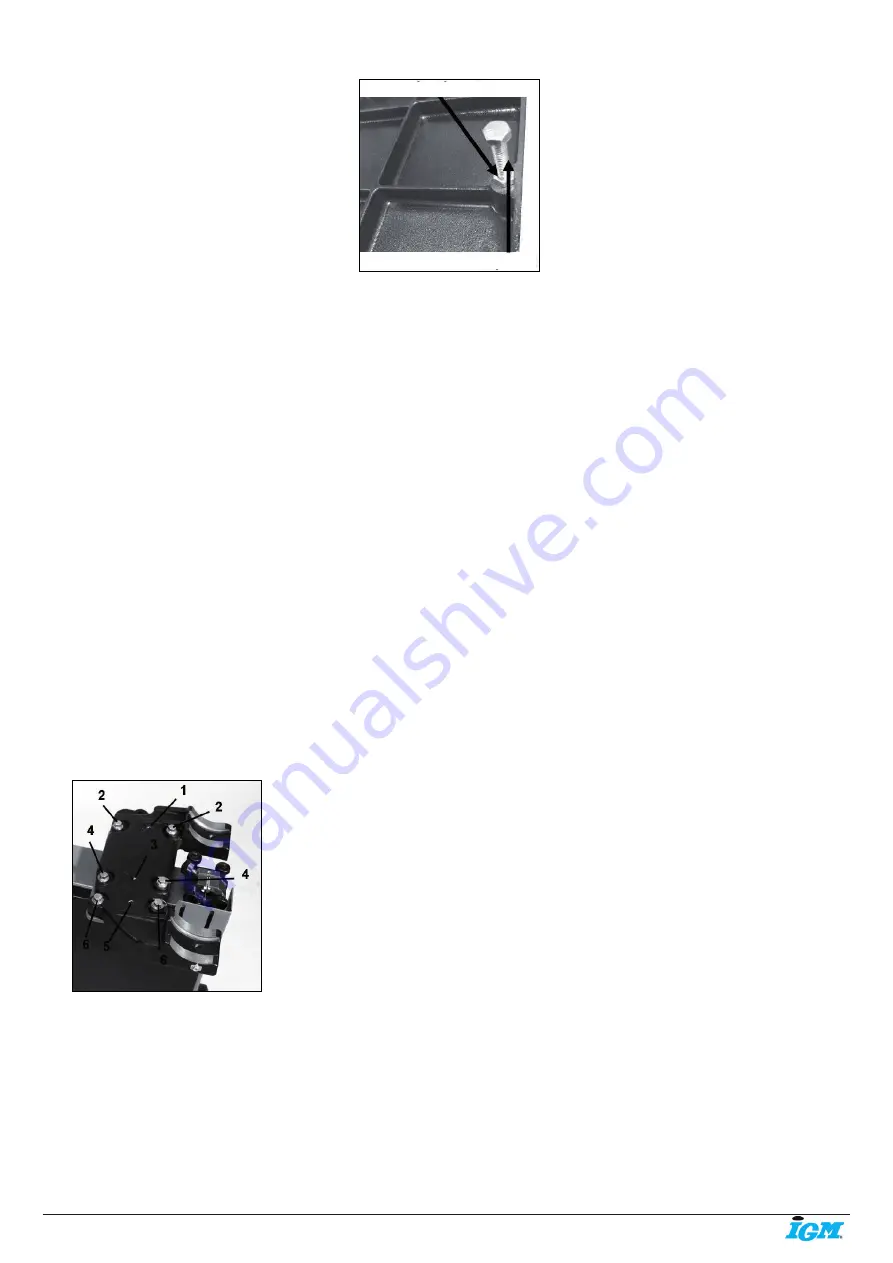
-17-
www.igmtools.com
Adjusting the table square to the bandsaw
blade
Note.
The machine is set in the factory and no
adjustment should be required but during
transportation movement may occur.
To access the adjustment screws, you will
have to tilt the table up to 45 degrees and lock
in position.
The adjustment is made with the jacking
screws 1 & 3 only. Jack screw 5 and clamp
screws 6 are used for support only.
1.
Set the table to 90 degrees and place an
engineer‘s square on the table and check if the
blade is leaning forward or backward. The
blade will be parallel and it is easier to check
the blade at the back.
2.
Tilt the table up to 45 degrees and lock in
position.
3.
Loosen jack screw 5 and clamp screws 6
[only used for support and not adjustment].
4.
If the top of the blade is leaning forward [gap
at the top of the engineers square], the back
of the table will have to be adjusted up. Slightly
loosen set screw 3 and the two hex head
screws 2, when loosening the clamp hex head
screws ensure that they are loosened the
same amount. Then fully tighten set screw 1
and the two hex head screws 4. Only make very
small adjustments as a small movement of the
jack screws makes a large adjustment of the
table. Move the table back to 90 degrees, clamp
in position and check if the blade is square to
the table with the engineers square. Repeat
adjustment if required.
5.
If the top of the blade is leaning back [gap at
the bottom of the engineers square], the front
of the table will have to be adjusted up. Slightly
loosen set screw 3 and the two hex head
screws 2. Then fully tighten set screw 1 and the
two hex head screws 4. Only make very
small adjustments as a small movement of the
jack screws makes a large adjustment of the
table. Move the table back to 90 degrees, clamp
in position and check if the blade is square to
the table with the engineers square. Repeat
adjustment if required
6.
Once adjustments have been completed,
lightly tighten set screw 5 and the two clamp
hex head screws 6. Do not over tighten as this
will bend the steel support plate and may affect
the adjustment that you have
made.
Adjusting the table square to blade.
1. Check that the stop bolt is in contact with the
tilt-blanking disc.
2. Place an engineers square on the table top
and bring up to the side of the blade.
3. Check if the blade is square to the table.
4. If adjustment is required loosen the lock nut
on the tilt-stop bolt and adjust in the required
direction.
Note.
Only adjust the tilt-stop bolt in very small
steps.
5. Tighten the lock nut and recheck
the blade square to the table.
Lock nut
Tilt stop bolt
6. If additional adjustment is required repeat
above steps.
10. Troubleshooting
Bandsaw will not start.
1. Check that the start switch is fully pulled out.
2. Check that the yellow safety plug is fully
engaged.
3. Check that the electrical power cord is
plugged into the power outlet.
4. Check that the electrical supply is on (reset
the breaker).
5. Check that you have the correct power.
The machine will not stop.
This is a very rare occurrence, as the machine
is designed to be fail-safe. If it should occur
and you cannot fix the fault, seek professional
assistance. The machine must be
disconnected from the power and never run
until the fault has been rectified.
1. Stop switch faulty. Replace the stop switch.
2. Internal breaker faulty. Replace the breaker.
Motor tries to start but will not turn.
1. With the power disconnected from the
machine, open the doors and try to turn the
wheel by hand. If the wheel is not turning, check
the reason for the jamming. Typical reasons
are: guides too tight, wood jammed in the
wheel. Adjust guides or remove jammed wood.
2. Capacitor faulty. Replace the capacitor.
3. Motor faulty. Replace the motor.
Motor overheats.
The motor is designed to run very hot, but
should it overheat it has an internal terminal
overload protector that will shut it down until the
motor has cooled down and then it will reset
automatically. If the motor overheats, wait until it
has cooled down and restart. If the motor
shuts down constantly, check for the reason.
Typical reasons are dull blade, overfeeding the
wood, motor cooling fan clogged or faulty, motor
cooling fins clogged and excessive ambient
temperature.
Squeaking noise.
1. Check that the motor cooling fan is not
contacting the fan cover.
2. Check the bearings.
3. Check the drive belt.
4. Check that the guides are adjusted correctly.
Upper guide shaft is tight or loose.
1. Clean and lubricate.
2. Adjust rack and pinion.
3. Bent rack. Replace the rack.
Blade slows down during a cut.
1. Loose drive belt. Re-tension the belt.
2. Dull blade. Replace the blade or have it re-
sharpened.
3. Feeding the wood too fast. Slow down the
feed rate.
4. Insufficient set on the teeth (wood nipping the
blade). Change blade for a blade with the
correct set.
5. Oil or dirt on the drive belt. Clean or replace
the drive belts.
6. Fence not aligned correctly. Align fence.
Blade will not track on flywheels.
1. Bad blade. Change the blade.
2. Crown on the wheels worn or damaged tire.
Dress the tires.
The blade kicks.
Bad blade. Replace the blade.
The blade makes a clicking noise.
Bad weld. Dress the weld or change the blade.
Blade overheats.
1. Dull blade. Change the blade or resharpen
the blade.
2. Pitch is too small for the depth of cut. Change
to a blade with the correct pitch.
3. Guides too tight. Adjust the guides.
4. Wood too hard for the selected blade.
Change the blade.
5. Blade too thick for the diameter of the
wheels. Change the blade.
Machine vibrates.
1. Machine not level on the floor. Re-level the
machine ensuring that it has no movement.
2. Damaged drive belt. Replace the belt.