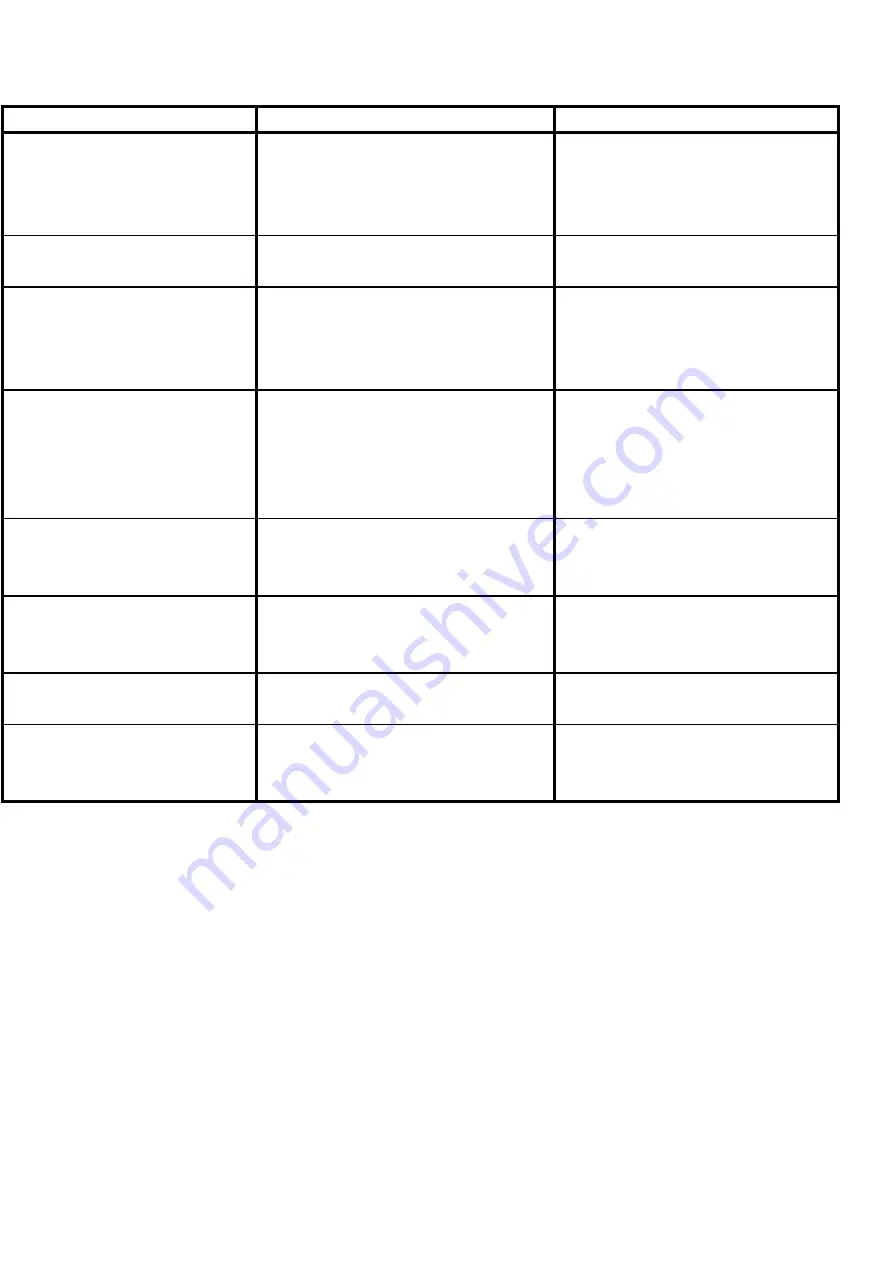
PROBLEM
POSSIBLE CAUSE
SOLUTION
Sanding belt clogs too quickly
1. Grit of sanding belt is too fine
1. Replace with larger grit
2. Sanding overload
2. Reduce sanding load.
3. Too much oil, dirt on wood surface
3. Clean wood, or use better work
Too many roundings created along the
1. Too much material being removed
1. Reduce the amount of material being removed
edge while sanding solid wood
Uneven thickness between the left and
1. Conveyor table not parellel with contact roller
1. Adjust conveyor table / contact roller to
right sides of the workpiece
2. Conveyor belt worn out
parallel
3. Graphite cloth and carpet on the pad are
2. Replace conveyor belt
worn out
3. Replace graphite cloth and carpet
Uneven thickness between the front and rear
1. Feed speed too fast
1. Reduce rate of feed
ends of the workpiece
2. Sanding overload
2. Reduce sanding load
3. Grit of sanding belt too fine
3. Use large grit sanding belt
4. Unequal position of pressure plate
4. Adjust pressure plate to produce equal
pressure on stock
Workpiece slips on the conveyor belt
1. Too much pressure from pressure plate
1. Reduce force from pressure plate
2. Dirty conveyor belt
2. Clean conveyor belt
3. Conveyor belt is worn out
3. Replace conveyor belt
Straight notches on workpiece surface
1. Dirty pressure plate
1. Clean pressure plate
2. Contact drum is scratched
2. Replace drum
3. Graphite cloth and carpet on the pad are worn out
3. Replace coth and carpet
Snake markings on workpiece
1. Sanding belt partially damaged
1. Repair/replace sanding belt
2. Worm area on sanding belt
2. Replace sanding belt
Cross-parallel stripes across the entire width
1. Sanding belt joint is too thick
1. Replace sanding belt
of workpiece
2.Worn areas on sanding belt
2. Replace sanding belt
3. Sanding load not less than 0.0mm
3. Reduce sanding load to less than 0.0mm
LUBRICATION AND MAINTENANCE:
1. The machine interior should be thoroughly cleaned every day after work. It is important to remember to remove the sanding belt beofre
cleaning and replace it afterwards.
2. The bearings should be greased after every 150 work hours.
3. If the machine is equipped with a hydraulic power system, the hydraulic oil should be renewed after after every 6000 work hours.
4. The water should be released from the filter cup regularly
5. Make sure that there is an adequate oil film on the table jack screws (support screws) at all times.
6. The oil inside the gear reducer should be changed after the first 300 hours of operation, and every 2500 hours of use thereafter.
Recommended oil is #140 gear oil.
16
Содержание MSANWB43X75-2RK-25-0197
Страница 2: ......
Страница 12: ...MAJOR PARTS OF THE MACHINE 7...
Страница 14: ...CONTROL PANEL FEATURES Figure 6 Figure 7 9...
Страница 22: ...GENERAL ELECTRICAL DIAGRAM 37 1K SINGLE PHASE 17...
Страница 23: ...18...
Страница 25: ...20...
Страница 27: ...22...
Страница 29: ...24...
Страница 31: ...26...
Страница 33: ...28...
Страница 35: ...30...
Страница 37: ...32...
Страница 39: ...ELECTRICAL PARTS 37 1K SINGLE PHASE 34...
Страница 41: ...36...