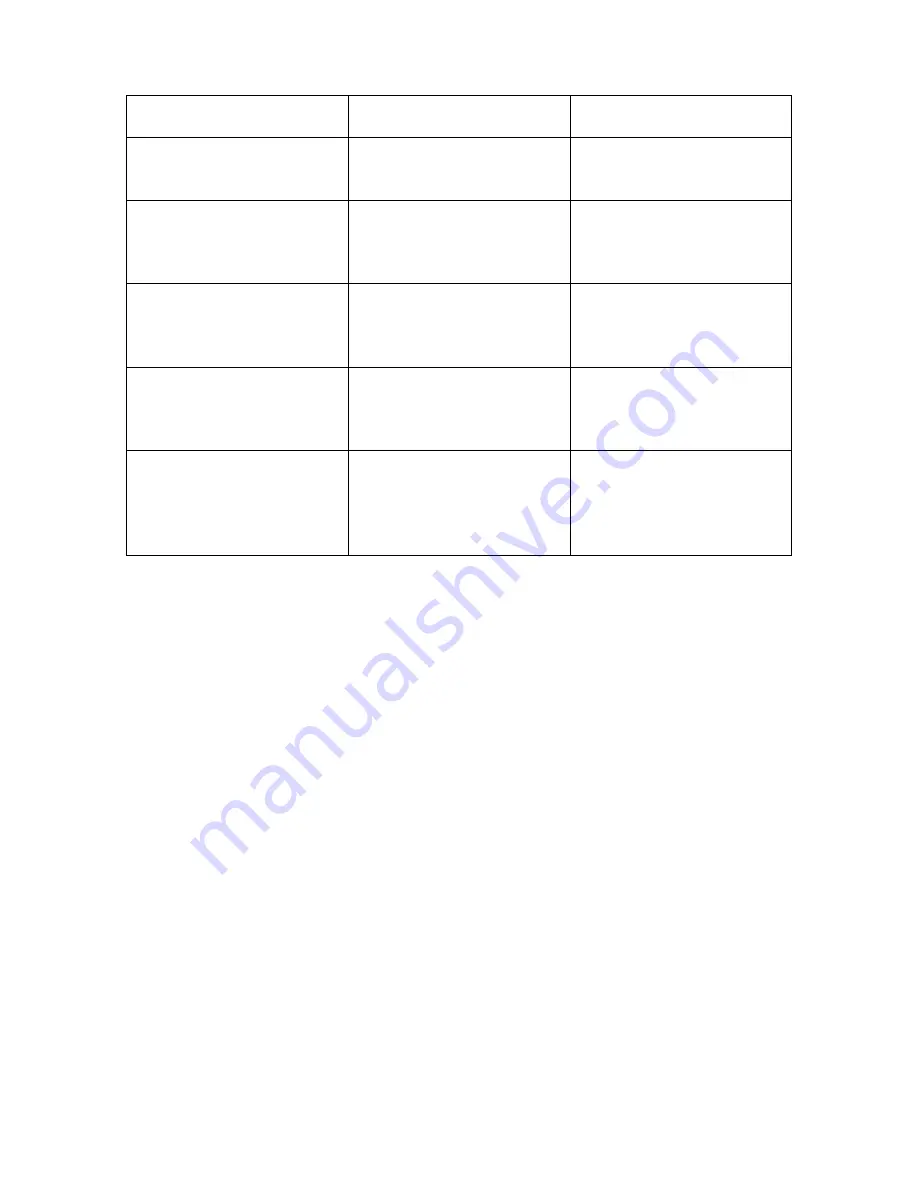
21
2. Too fine a cut.
2. Increase the depth of
cut.
Chip marks, random
pattern.
1. Chips not removed
from cutter head.
1. Use a dust collection
system. Or a stronger
dust collection system
Board edge is concave
or convex after jointing.
1. Job not held with even
pressure on in feed
and out feed table during
cut.
1. Hold job with even
pressure as it moves
over the cutter head.
2. Job started too
uneven.
2. Take small cuts to
remove the extreme high
spots before doing a full
pass.
3. Board has excessive
bow or twist along its
length.
3. Surface plane one face
so there is a good
surface to position
against the fence.
4. Insufficient number of
passes.
4. It may take 3 to 5
passes to achieve a good
edge, depending on
starting condition of
board and depth of cut.
Содержание MJO6012-0800-1phCSA
Страница 2: ......
Страница 22: ...22 Electrical drawings Exploded view drawings...
Страница 23: ...23...
Страница 24: ...24...
Страница 25: ...25...
Страница 26: ...26...
Страница 27: ...27...
Страница 28: ...28...
Страница 29: ...29...
Страница 30: ...30...
Страница 31: ...31...
Страница 32: ...32...