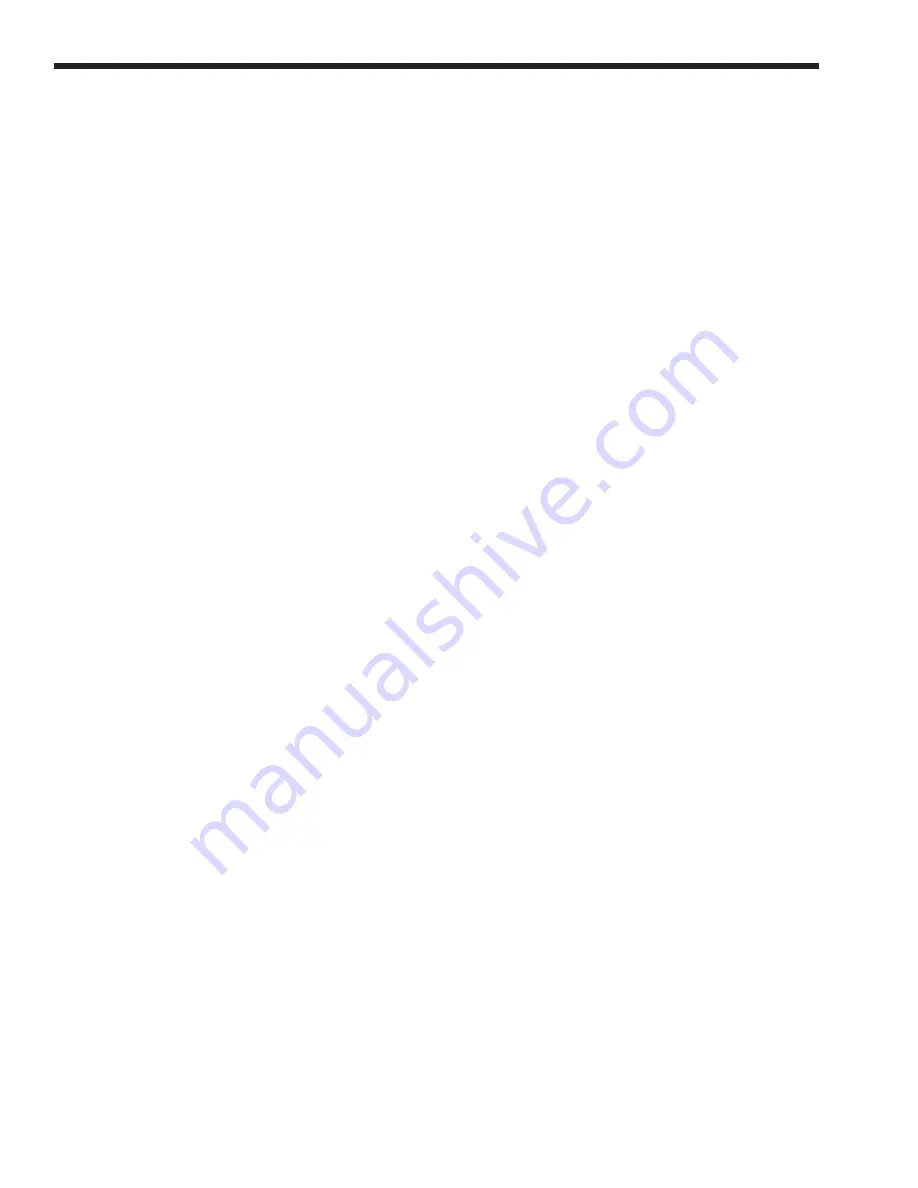
LAARS HEATING SYSTEMS
Page 10
speed. Do not operate a summer exhaust fan.
Close fireplace dampers.
4.
Place in operation the appliance being inspected.
Follow the lighting instructions. Adjust
thermostat so appliance will operate
continuously.
5.
Test for spillage at the burner opening after five
minutes of main burner operation.
6.
After it has been determined that each appliance
remaining connected to the common venting
system properly vents when tested as outlined
above, return doors, windows, exhaust fans,
fireplace dampers and any other gas burning
appliance to their previous conditions of use.
7.
Any improper operation of the common venting
system should be corrected so the installation
conforms with the National Fuel Gas Code,
ANSI Z223.1. When re-sizing any portion of the
common venting system, the common venting
system should be re-sized to approach the
minimum size as determined using the
appropriate tables in Appendix G in the National
Fuel Gas Code, ANSI Z223.1.
1I. Water Piping of Boiler System
Figure 9 shows ‘typical’ plumbing installations.
It is recommended that unions and valves are used at
the boiler inlet and outlet so it can be isolated for
service. Check local codes for specific plumbing
requirements before beginning the installation.
An ASME pressure relief valve is supplied on all
JV boilers, and is pre-set at 30 PSI (207 kPa). The
relief valve outlet piping must discharge to a drain.
Under no circumstances should the relief valve piping
be a closed circuit.
A pressure reducing valve (automatic feed) must
be used to maintain system at constant proper pressure
(see Figure 9). Supply properly installed purge valves
to eliminate air from each circuit.
A drain valve is supplied with the boiler, and can
be found in the plastic bag shipped with each boiler.
This valve is to be installed on the lower right side of
the boiler (see Figure 2) and is used for draining the
unit. To drain the boiler completely, open the drain
valve and remove the two drain plugs located on the
lower left side of the boiler.
Be sure to include air vent devices located at the
highest point in the system to eliminate trapped air,
and an air elimination device near the outlet side of
the JV boiler. Manual vent valves are recommended.
Hot water piping should be supported by suitable
hangers or floor stands, NOT by the boiler. Due to
expansion and contraction of copper pipe,
consideration should be given to the type of hangers
used. Rigid hangers could transmit noise through the
system caused by the piping sliding in the hangers. It
is recommended that padding be used when rigid
hangers are installed.
A properly sized expansion tank must be
included in the system. Laars offers an air-charged
diaphragm-type expansion tank, with an automatic
feed valve, which includes a pressure regulator set at
12 psig.
1I-1. By-Pass Piping
The following information and suggestions are
made on by-pass piping as it affects the temperature
rise at the boiler. A boiler temperature rise must be
taken on all JVi boiler installations. If the temperature
rise exceeds 30°F (17ºC), it is an indication that the
boiler is not receiving adequate water flow. Check the
pump for any obstruction, replace the pump with a
larger size where necessary, or install a system by-
pass (illustrated in Figure 9).
On JVi sizes 125, 160, and 225 with a multiple
zone system, a by-pass is required to ensure proper
flow in addition to properly sized circulator and piping
system.
NOTE: On JVi sizes 160 and 225 a primary/
secondary piping system is recommended. In this
system, a circulator is dedicated to pumping the boiler
only. This circulator should be sized for the boiler
head loss and flow rate.
The two above piping configurations can also
apply to JVi sizes 50, 75 and 100, but generally, these
units require flow rates which are easily obtained
without a by-pass.
All precautions must be taken by the installer to
insure that a maximum temperature rise through the
boiler does not exceed 30°F (17ºC). The temperature
rise on boilers installed in multi-zone systems using
zone valves must be taken when the zone of the
longest length and/or the zone of the highest head loss
is open.
Please note that a 1" (25mm) diameter by-pass
with balancing ball valve must be installed if a return
water temperature of below 110°F (43ºC) is expected
under operating conditions (see Figure 9).
1J. Chilled Water Systems
If the boiler is installed in conjunction with
refrigeration systems, it shall be installed so that the
chilled medium is piped in parallel with the heating
boiler with appropriate valves to prevent the chilled
medium from entering the heating boiler.
When boiler piping is connected to heating coils,
which are in close proximity to refrigerated air
circulation, there must be flow control valves or other
automatic methods to prevent gravity circulation of
the boiler water during the cooling cycle.
Содержание Mini-Therm JVi JVH
Страница 11: ...Mini Therm JVi Page 11...
Страница 13: ...Mini Therm JVi Page 13 Figure 11 Wiring Diagram JVP Figure 10 Wiring Diagram JVH...
Страница 27: ...Mini Therm JVi Page 27...