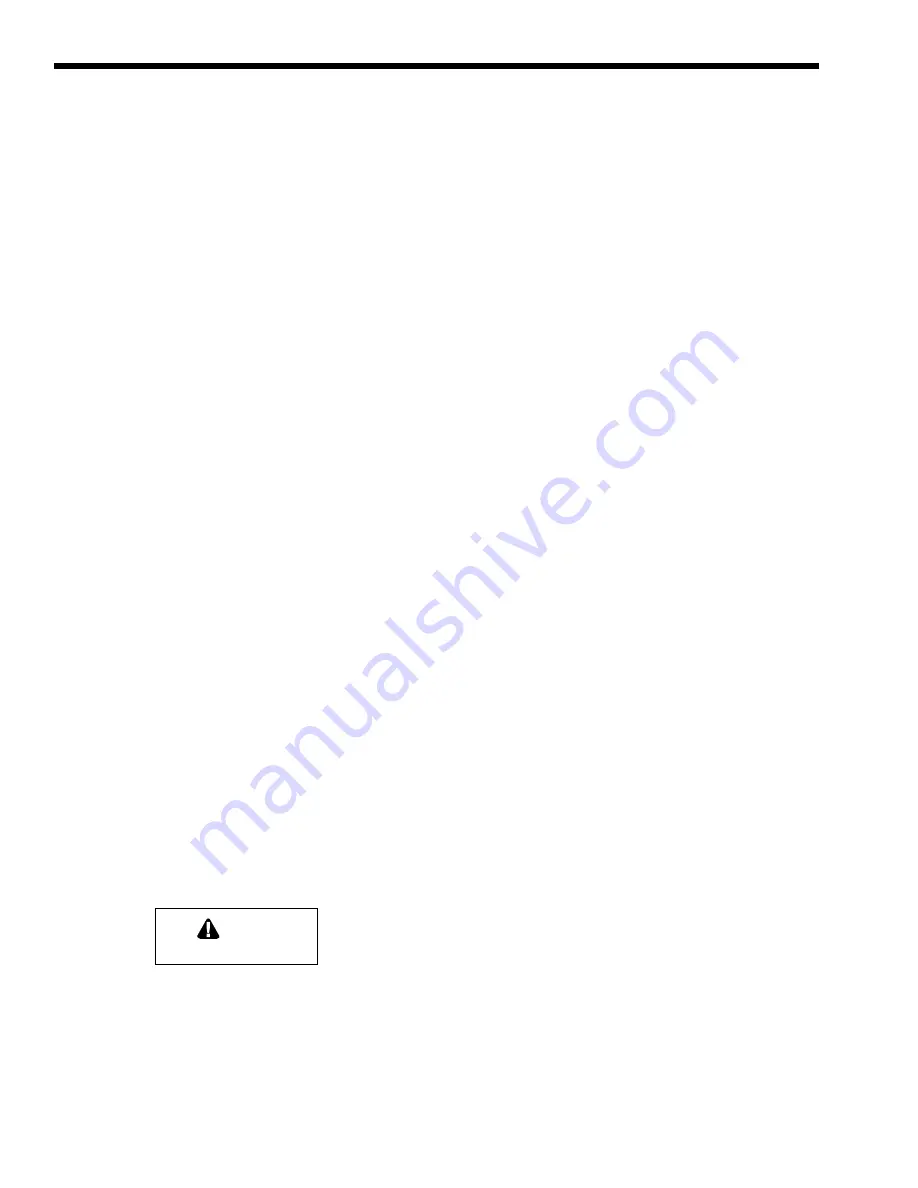
Page 30
LAARS Heating Systems
The control displays the supply temperature, by
default, and the user can access the heat exchanger
inlet temperature, tank temperature (EBP models),
heat exchanger delta T, outdoor air temperature (if
reset is used), and all of the setpoint and differentials
that are set on the boiler. 7 fault codes can also be
displayed, for diagnostic help.
To replace the boiler control, shut off 120V
power to the Endurance. Remove the two sheet metal
screws from the controller mounting bracket. Pull the
controller, attached to the mounting bracket out, to
access the electrical connectors.
Remove the electrical connectors from the
control. Pull out the tabs on the retaining clip, while
pulling the controller out through the front.
Replace in reverse order.
8.5 Ignition Control
The ignition control controls the hot surface
ignitor and proves that the flame signal is appropriate
for powering the gas valve. It also controls the
blower’s pre-purge and post-purge timing. It works
with the boiler control to ensure proper and safe
operation of the Endurance.
To replace the ignition control, shut off the 120-
volt power to the appliance. Remove the cover to the
Endurance control panel. Remove the electrical
connectors from the ignition control. Take out the
controller’s mounting screws, and pull the controller
out. Replace in reverse order.
8.6 Ignitor / Flame Sensor Assembly
The ignitor is a hot surface ceramic composite
device. It is energized whenever there is a call for heat
and switched off when ignition is established.
The flame sensor is a remote sensing flame rod
which is connected directly to the ignition control. The
ignitor should read 50 to 100 ohms resistance when at
room temperature.
If the ignitor fails and the assembly must be
replaced, always install a new ignitor gasket with the
replacement assembly.
For sequence of operation, see Section 9.1,
Servicing.
Caution
Ignitor gets hot.
8.7 Transformer
The control transformer accepts 120 VAC line
voltage and provides 100 VA of 24 VAC control
voltage for the boiler control ONLY. It is NOT
capable of supplying control voltage for external
devices such as zone valves, which MUST have their
own separate power supply.
Should the transformer require replacing, shut off
the 120 volt power. Unplug the transformer wires from
the transformer, unscrew the two fixing screws and
remove the transformer.
Fit the replacement transformer in reverse order.
8.8 PWM Board
The PWM board converts the 0-10V modulating
signal that comes from the boiler control to the PWM
(pulse width modulating) signal that is sent to the
blower to control the blower speed, and hence, the
modulating point of the Endurance.
This board also converts 24V AC to 24V DC,
which is used to power the boiler.
To replace the PWM board, shut off the 120 volt
power. Unplug the two electrical connectors to the
PWM board. Depress the barbs on the four standoffs
to free the board, and pull it out. Replace in reverse
order.
8.9 Blower
The combustion air blower is a high pressure
centrifugal blower. It is powered by a 24VDC motor
which is controlled by the boiler control with voltage
that has been converted by the PWM board. Its speed
will be varied according to the temperature of the
boiler flow.
If a blower change is required, turn off the 120
volt power and unplug the wires from the blower
motor. Remove the four nuts from the blower
discharge flange and the four screws that secure the
gas manifold to the gas valve. Remove the complete
assembly. Unscrew the combustion air inlet assembly
and register plate from the fan.
Fit the replacement fan in reverse order, ensuring
that all joints are made correctly and sealed.
After replacement the combustion should be
checked for correct air fuel ratio (see Section 10).
8.10Transfer Tank (EBP)
The transfer tank contains approximately 20
gallons of boiler water. It functions as an energy
storage vessel to reduce boiler cycling on small output
heating zones and to provide additional heat for
domestic hot water through the domestic hot water
(DHW) plate heat exchanger.
If a tank change is necessary, access to the tank is
possible by removing the jacket’s front door. This is
done by removing the screws that hold the panel at the
top and lifting the panel away. Isolate the appliance
and drain down using the drain cock at the base of the
tank. Remove the tank sensor. Undo the union and the
pump flange bolts that connect the tank to the boiler,
unscrew the panel between the upper and lower
compartments, support the upper components and
remove the tank. Installation of the new tank is done in
the reverse order. After installation purge all air from
the boiler before restarting.